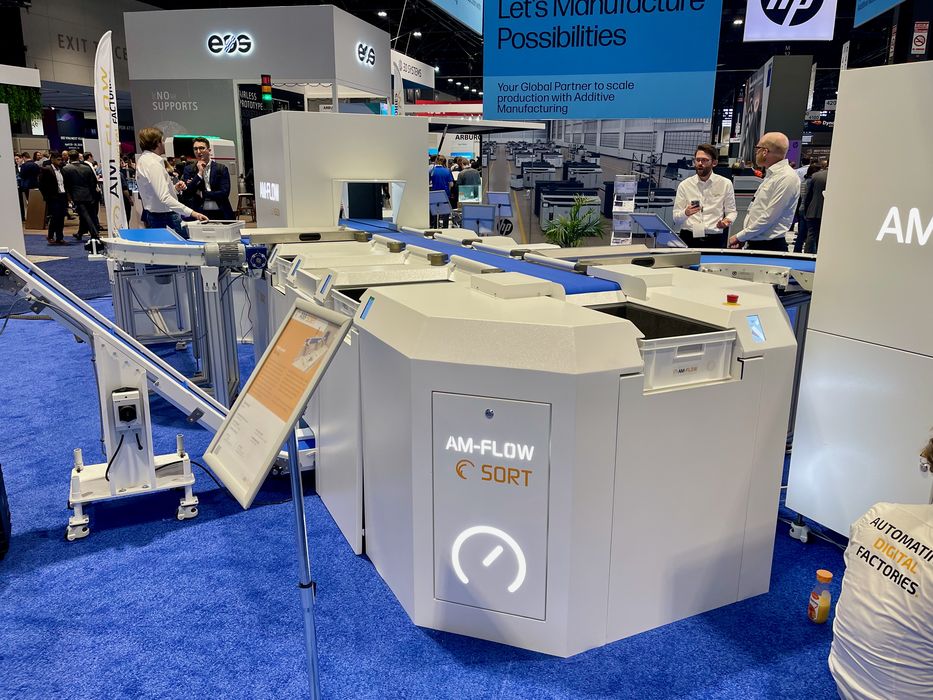
AM-Flow showcased an intriguing bagging system for 3D printed parts.
Producing parts in volume with 3D printing is far more complex than you might think, but it’s a business many companies are now diving into. Arrays of 3D printers accept print jobs from a dispatcher and rapidly print objects for requestors.
The outcome? High throughput — and a plethora of parts to handle after production.
Traditional Manufacturing vs. 3D Print Factories
This isn’t much of an issue with traditional mass manufacturing: all the parts are identical. Box them up, ship them out, and you’re done.
However, modern 3D print factories are a different story. They have the ability to produce a unique item each time a printer operates. This fundamentally different form of production requires handling unique parts that may not only differ but could also be destined for different customers.
AM-Flow’s Solution for Additive Manufacturing Lifecycle
AM-Flow has been developing a flexible solution for that part of the additive manufacturing lifecycle: what to do with completed parts?
Their system, which we’ve covered before, includes a conveyor belt system. Parts are poured in at one end, where they are 3D scanned. The scan system can match the CAD model, identify the part, and determine what to do with it. If the part doesn’t meet tolerances, it can be automatically sent to a disposal bin.
As the conveyor belt carries the part further down the line, robot arms flick the parts into bins, effectively sorting them at high speed.
The Inspiration Behind AM-Flow
Now for a quick aside: My discussion with AM-Flow at RAPID+TCT revealed something interesting — the inspiration for AM-Flow.
I shared my experience visiting Shapeways in New York back in 2013. At that time, I found the company’s 3D printers surrounded by manual workarounds to ensure parts were tracked through the process until shipping. It seemed laborious and error-prone.
To my surprise, the AM-Flow rep got quite excited and said that he had worked at Shapeways at that time, and the challenges they faced handling parts largely inspired the creation of AM-Flow.
AM-Flow’s Bagging Mechanism
Back to the present. AM-Flow demonstrated an interesting feature for their sorting system: a bagging mechanism.
Not only would parts be sorted, but they can also be bagged at that point. As you can see in the image, the bag can be uniquely labeled. This could be codes for further identification later, or even shipping information. AM-Flow said it’s up to the customer to decide what they need on the bags.
Upon examining AM-Flow’s system as a whole, it’s remarkable how much manual effort could be saved. Quite literally, the operator need only show up occasionally to pick up the bagged items for shipment.
Via AM-Flow