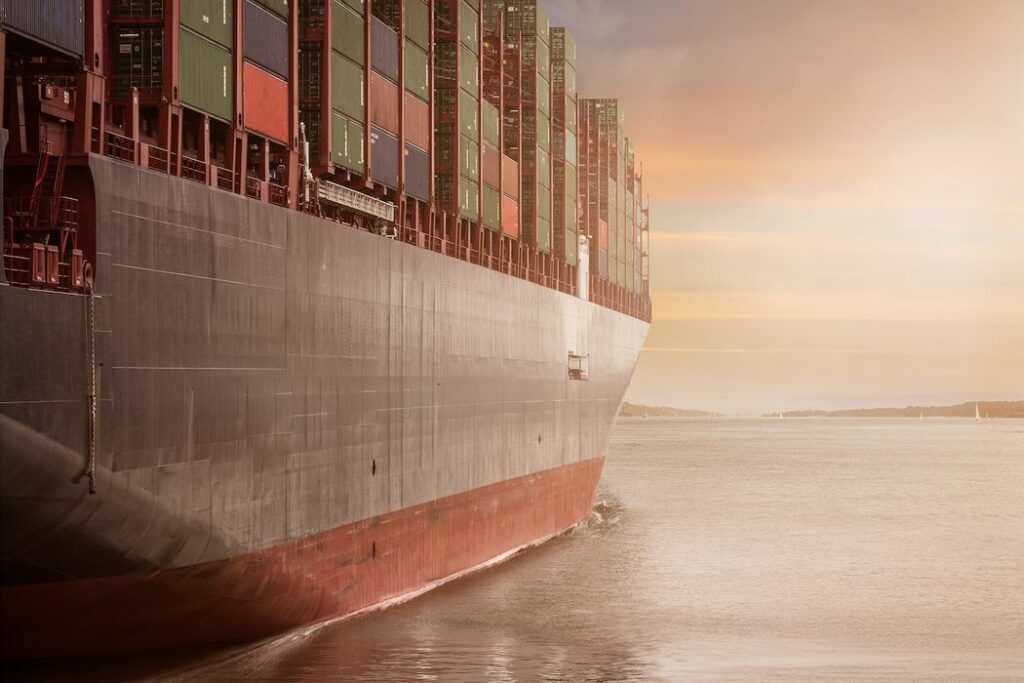
I’ve been doing some thinking about what might unfold in the next year or so.
But first, let’s look at what happened over the past couple of years.
It’s the pandemic, of course. That event changed everything in ways no one could have expected. One of the many societal changes that resulted from the pandemic is a significant increase in the use of 3D print technology by western firms.
The reason for this boost in usage is straightforward: these companies couldn’t source their parts from their usual suppliers overseas.
That happened because overseas factories temporarily shut down, and generated huge supply chain issues.
In this case, the supply chain really amounts to shipping. Parts made in, say, China, would normally be loaded into a shipping container and put on a ship bound for the Americas. However, there were no empty shipping containers to be had. The empty containers were tied up in ports everywhere, where the pandemic had closed port activity and generally messed up things on the receiving end. In some cases, companies went bankrupt and could not receive their shipment.
In any case, mountains of shipping containers went into limbo, driving up the cost of shipping. That’s because the fewer containers available could demand higher prices.
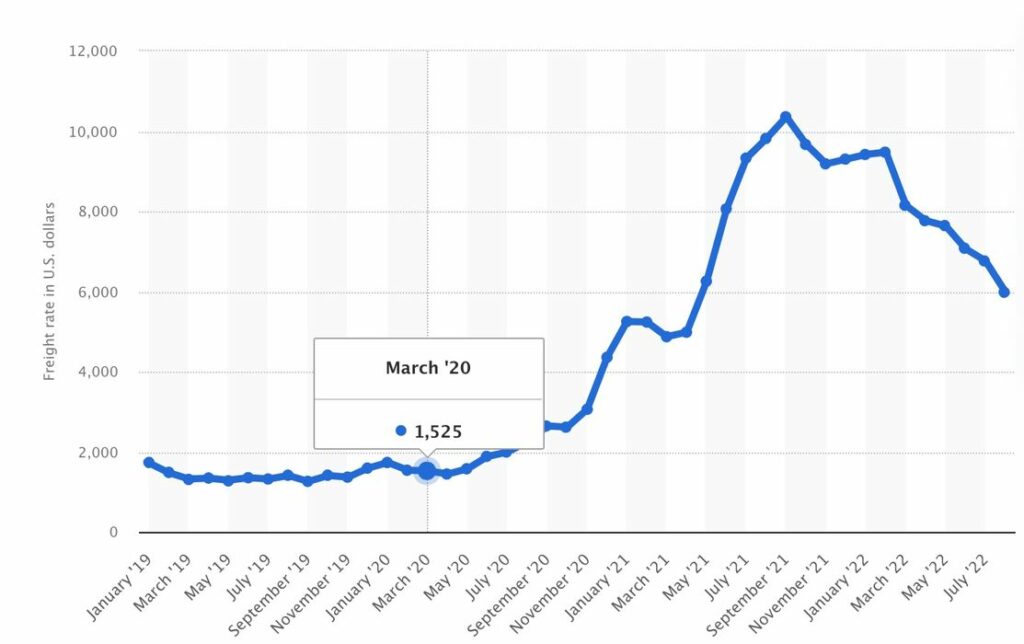
In this chart from Statista, we can see the average price of a shipping container moved significantly from US$1300 in 2019 to peak at over US$10,000 in 2021. I’ve heard anecdotally from 3D printer manufacturers that at times they were forced to pay over US$20,000 for a shipping container.
These are significant extra costs.
Consider that a standard 20ft container holds 33sm of volume. Now if you were shipping 3D printers in a 1m box, you’d be able to put about 30 on such a container. That means that each printer would have to carry an extra US$20,000 / 30 = US$666 each. If that was a US$1000 machine, then you’re looking at a price increase of almost 70% just for shipping costs alone.
These and other computations showed Western manufacturers that in fact it made financial sense to produce parts themselves (or with local providers) to avoid the excessive shipping costs. That approach also removed a huge risk factor. Previously the number one consideration was part cost. Going forward, it’s part cost AND risk.
As a result many manufacturers turned to 3D printing because it allowed near-instant turnaround of part production: no tooling is required. It also generated huge business for several notable manufacturing services that were able to leverage their expertise and capacity in additive manufacturing, where clients might not have been able to quickly learn the ropes of the tech.
In all this has been a very good season for 3D printing as this scenario has driven up demand for equipment and materials like nothing ever before.
But let’s look a bit more at what might happen as this plays out.
Recall that shipping container price chart above? Note that the price peaked. It’s going down now.
How low will it go? Probably at least back to “normal” levels, and likely even lower as demand for shipping is less than it used to be. This means that the equation manufacturers used to justify 3D printing on their own may flip.
It may very well be that some manufacturers turn back to overseas manufacturing if the effective unit cost per part drops sufficiently. This could mean a slowdown of 3D printer sales to production companies.
There will certainly be many companies that will stick to additive processes, having been exposed to them during the pandemic and liking what they saw. However, a key driver for new entrants to AM might become closed in a year or two.
That slowdown may very well affect the sales and valuations of several major 3D printer manufacturers, as well as some of the materials and service providers.