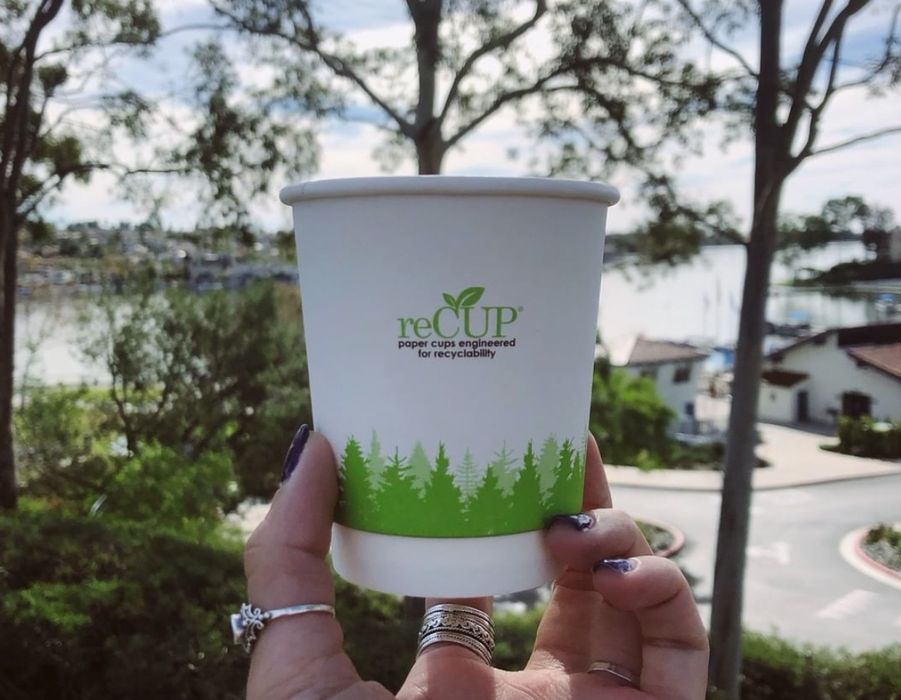
With the increasing emphasis on sustainability in industry, 3D printing may have to look towards unusual solutions.
A post by Carbon founder Joseph DeSimone on sustainability got me thinking. He posted on LinkedIn:
“One of the keys to sustainability in my opinion is more about creative business models (and less about technology). Don’t get me wrong, there are massive technological needs that need to be addressed in many areas of sustainability and recycling, however, there are many reasonably good technical solutions that have already been developed that are in need of an effective business model that if implemented, could make an important impact immediately.”
DeSimone pointed to a recent example by McDonald’s, which launched a reusable cup program in the UK. Customers pay £1 for a cup, but get that back when they return it. McDonald’s will “deep clean” the cups and lids and re-use them.
LinkedIn Member Ryan Gorman, Team Lead Product Management at Outdooractive, added:
“This is a similar process to Recup, a company here in Germany supplying low cost (I believe polypropylene) reusable cups to metro areas. The cup is given as a to-go in many coffee shops and can be returned to any participating store. They are then sanitized and the circle repeats.”
While many 3D printing companies work towards more sustainable solutions, they often focus on the technological: the materials, the energy used, and so on.
But are there non-tech methods for 3D printing companies to increase sustainability?
I think there are. One that is used by some companies is reuse of material containers. Stratasys, for example, will accept empty filament canisters for their Fortus equipment. Similarly, they also accept empty cartridges for their PolyJet equipment, which by the way, are tricky to dispose of otherwise due to the toxic nature of the resins.
I’ve seen a couple of initiatives where 3D print materials companies will accept empty spools, but by and large that’s not a feasible approach. That’s because the cost of the material is almost as much as the cost of shipping the spool back to the provider.
The “Recup” program described by Gorman works because it’s easy for customers to return the cups: ANY participating shop accepts the returns. That’s just not the case for 3D print material.
Unfortunately there are really no standard container sizes for 3D print materials. Many pieces of equipment use proprietary materials where the container is effectively part of the machine’s design, making it impossible for others to make use of the same container style.
There could be an opportunity with filament spools, but again that’s thwarted by the consistent divergence of spool designs between providers. There are different spool diameters, hub diameters, widths. I’ve seen them all.
If by some miracle an industry standard spool configuration were agreed upon, then users would have the possibility of easily returning used spools to local operations. If there’s even one physical store selling filament in a city, it could act as a depot for empty spools. If I were running such an establishment, I’d jump at the chance to be the depot because it would certainly bring a stream of potential customers to my store.
Alas, that is not likely happening within our lifetimes, unless something significant happens.
That significant happening could only be some kind of agreement between multiple major manufacturers of FFF 3D printers, and I don’t see even a hint of that happening.
At least not yet.