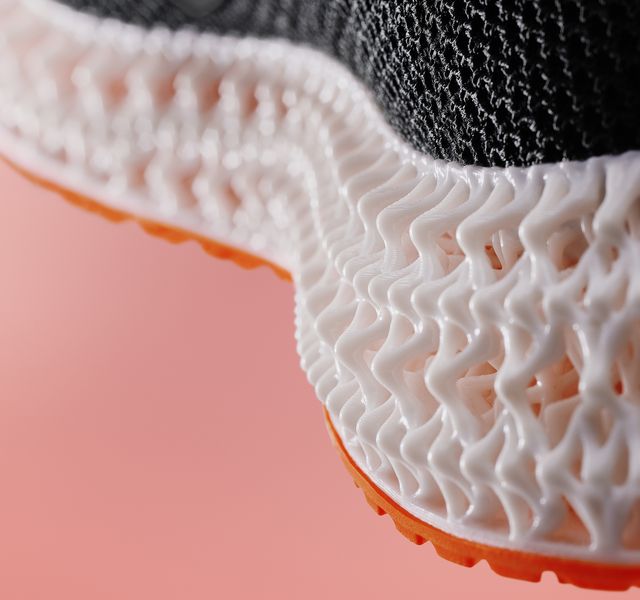
Adidas announced a new partially 3D printed shoe, the 4DFWD.
The footwear giant has partnered with Carbon for several years to develop precisely-engineered lattices for the new product. These offer a more lightweight solution, yet provide a great deal of designed function.
And they look very cool, too.
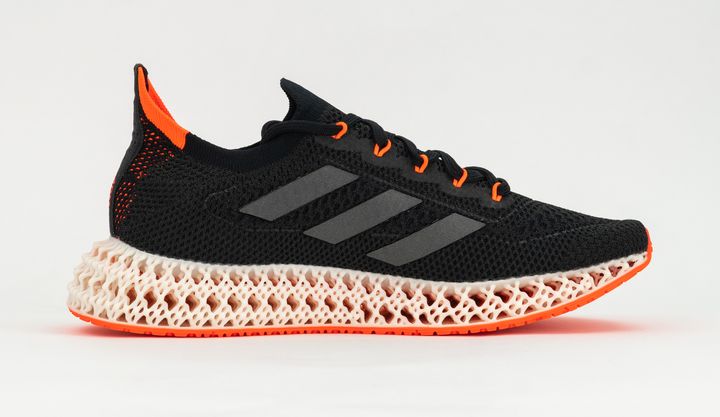
Adidas made extensive use of the Carbon Design Engine, a purpose-built software tool to create engineered lattice structures. It generates 3D models that can then be quickly 3D printed on Carbon 3D printers.
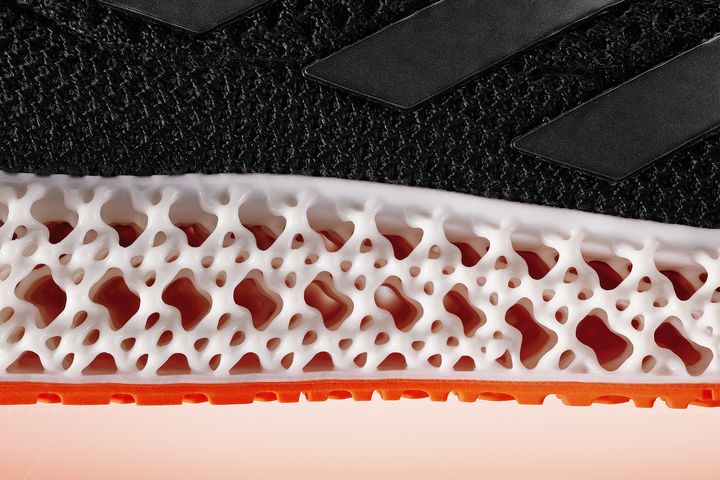
Some years ago I spoke with Carbon’s Philip DeSimone and realized the company is as much a software company as they are a 3D printer hardware manufacturer.
The idea is this: manufacturers will not adopt AM technologies unless they can provide value. Value from AM is mostly derived from the ability to produce “impossible” parts that cannot easily be made in other manufacturing processes. Thus a company must somehow design innovative and complex 3D models in order to leverage the technology.
However, almost all companies have a hard time doing so because they don’t know how. It takes not only imagination to think up solutions in ways never considered previously, but also software tools to do so.
That’s why Carbon has spent years developing their Carbon Design Engine, which makes it far easier for a manufacturer to develop complex 3D printable components. In a big way, this software opens the door for AM adoption by many companies.
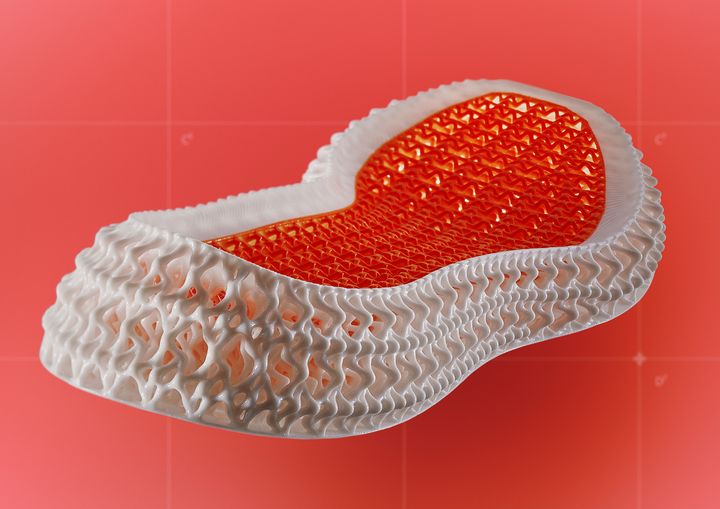
Carbon has been working with Adidas for several years on this basis, and now it seems that Adidas is fully leveraging the potential of the technology. The new 4DFWD product seems to have a number of very interesting properties that have largely been the result of the highly-engineered lattice structure. They explain:
“Born from this process is the new adidas 4DFWD lattice midsole. Identified from one of five million possible lattice structures and made of 39% bio-based material, the bowtie-shaped FWD CELL has been specifically coded to compress forward upon vertical impact. When compared to previous generations of 4D midsole, adidas 4DFWD generates three times as much forward motion under vertical loading in mechanical testing conditions. As a result, peak braking force experienced by the athlete during running is reduced on average by 15% as the midsole redirects these vertical impact forces into horizontal forward motion – delivering running economy comparable to that of Ultraboost midsoles in lab conditions.”
As you can imagine, designing a midsole lattice structure to accomplish that would be quite impossible without sophisticated software to assist. The complexities of a shoe have never been higher.
If you’re interested in obtaining a set of 4DFWD’s, there will be limited opportunities to do so. There will be a signup available through the Adidas app until the 16th, and then a “worldwide drop” in mid-August.
Just as it took the aerospace industry many years to finally recognize the viability and benefits of metal AM, the same transformation process may be underway in consumer products with the example set by Adidas.
Perhaps in the not-too-distant future we’ll see highly-engineered products of all sorts.