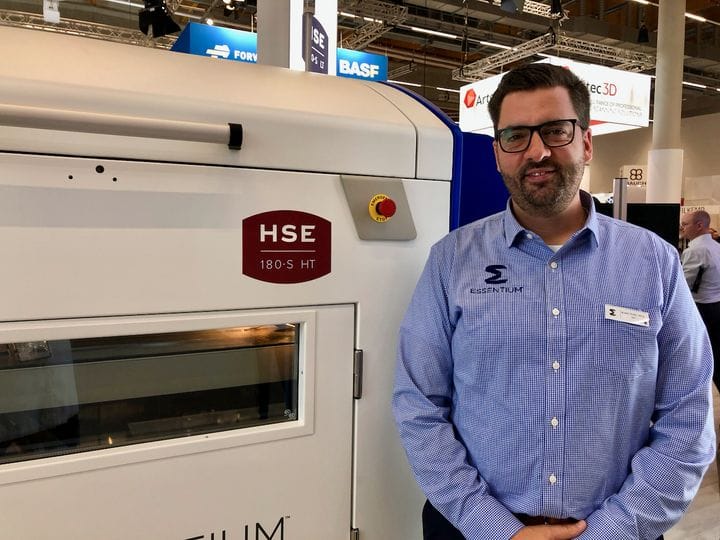
A chat with Essentium CEO Blake Teipel revealed something rather interesting about the additive manufacturing industry.
To many the advancement of AM technology has been superb; it’s a technology that grew from basically zero a few decades ago to today’s de facto standard use in several industries. We’ve seen the highest number of machines being used, most materials consumed, highest volume of parts produced with revenues at an all time high.
It’s a huge success.
Or is it?
My discussion with Teipel revolved around the company’s materials strategy. Like some other 3D printer manufacturers, Essentium uses what’s called an “open materials” strategy. But as the discussion proceeded, it became clear what Essentium means by “open materials” is quite different from what happens in other equipment.
First, let’s take a look at the two material strategies typically used by 3D printer companies.
Closed Materials
Closed materials is the go-to strategy for many 3D printer manufacturers these days. The concept is that only materials supplied or certified by the company may be used in the device.
This approach is either loved or hated by operators.
It’s loved because it provides operators with certainty. Print parameters are known and when the material is used on a specific machine, very consistent results will be obtained. This is a critically important factor for many using AM equipment for production purposes. Parts produced in most cases must meet specific engineering specifications, and variances are costly.
It’s hated because the manufacturers using this materials strategy tend to bump up the price of materials higher than those from third parties. The fact that there is “lock in” with the vendor for materials means there is lack of material choice.
Depending on your situation, closed materials might be a desirable feature that you would pay for, while in others it might be seen as an unnecessary expense.
Open Materials
In contrast, an open materials strategy means the 3D printer manufacturer is ok with the operator using any materials on the machine. This opens up the possibility of using inexpensive materials from unusual sources, inventing one’s own materials or obtaining unusual materials from third parties. It’s a far more flexible solution.
However, in most cases the operator is left to their own to figure out how to print consistently and correctly with the unknown material: the 3D printer manufacturer cannot be expected to test all possible materials. “Results are not guaranteed.”
Some manufacturers recently have begun preparing databases of print parameters for third party branded materials, making it a bit easier to get the “closed” benefits while still being “open”.
Essentium’s Take On Materials Strategy
Teipel’s explanation of Essentium’s materials strategy was a bit different from what I expected to hear. While their marketing materials say “open materials”, it’s really much more.
It turns out that Teipel spent years in a prior life working for a major manufacturer, Caterpillar. There they made heavy use of CNC milling machines to produce a wide variety of parts, but they were used in an entirely different way than 3D printers are typically used today.
Teipel believes most manufacturers seek to obtain the best results by fine tuning their manufacturing machines themselves; that’s why they employ squads of engineers.
But that’s not what today’s typical 3D printers do. Teipel explains:
“I don’t know the best way to make the best parts for an airplane. I don’t know the same for automotive parts, and so on.”
He’s right. It’s the people in those industries that do, not the 3D printer manufacturers.
But what does almost every 3D printer manufacturer do today? They show up with a machine, materials and say “Just trust our settings!”
Teipel said:
“At Caterpillar we would never buy systems that do that.”
Evidently Teipel has discovered this same sentiment in many discussions with major manufacturers. They don’t understand why “additive” has taken this different approach to materials and part making. It’s not at all like the CNC equipment business.
Teipel believes the AM industry could be vastly larger than it is today because years ago most of the major players chose to use a closed materials strategy.
Meanwhile, he listed several massive CNC equipment manufacturers that are much larger than their AM equivalents, even though they are only slightly older.
Teipel explained further:
“All companies want the same things: the keys to the car they bought. Why are the additive companies doing this? Doesn’t make sense.
I think the approach in AM has been backwards for a long time. The industry is so small. If we could open up more, then the whole industry could progress. It would benefit everyone because the space will be much bigger.”
Essentium’s Materials Strategy
Based on all this, what exactly is Essentium doing for materials?
It turns out they have a collaborative approach with their clients. In other words, they recognize that each and every customer likely has different goals and therefore might require different types of materials and unique printing parameters.
At that point in the conversation I realized that the simple print parameter databases being deployed by several other 3D printer manufacturers is not going to do the job because they assume everyone wants the same kind of results. Teipel said:
“Sometimes all they care about is speed and not at all about surface quality, while others absolutely need high quality cosmetic surfaces.”
How can a generic print profile possibly know this? This shows me that indeed many 3D printer manufacturers have it backwards. They are addressing those who don’t know how to operate 3D printers, rather than addressing the needs of actual professional manufacturers.
Essentium has set up their equipment so that it is easy to print sample bars for testing by clients, which goes along with their open architecture. They provide training for slicing software to enable clients to develop their own parameters, just like what is done for CNC equipment — and many of their clients will literally be CNC operators familiar with this approach.
Teipel explains the technical aspects of this tuning:
“We do pull back some operating parameters that work, and put them into our generic profiles for machines. But there is quite a lot of flexibility because our system is viscosity based, not temperature based. We provide a generic set to get started, then clients develop proprietary processes for themselves.
It becomes an advantage for the client.”
As the conversation concluded, I had only one thought.
We’ve been doing it all wrong.