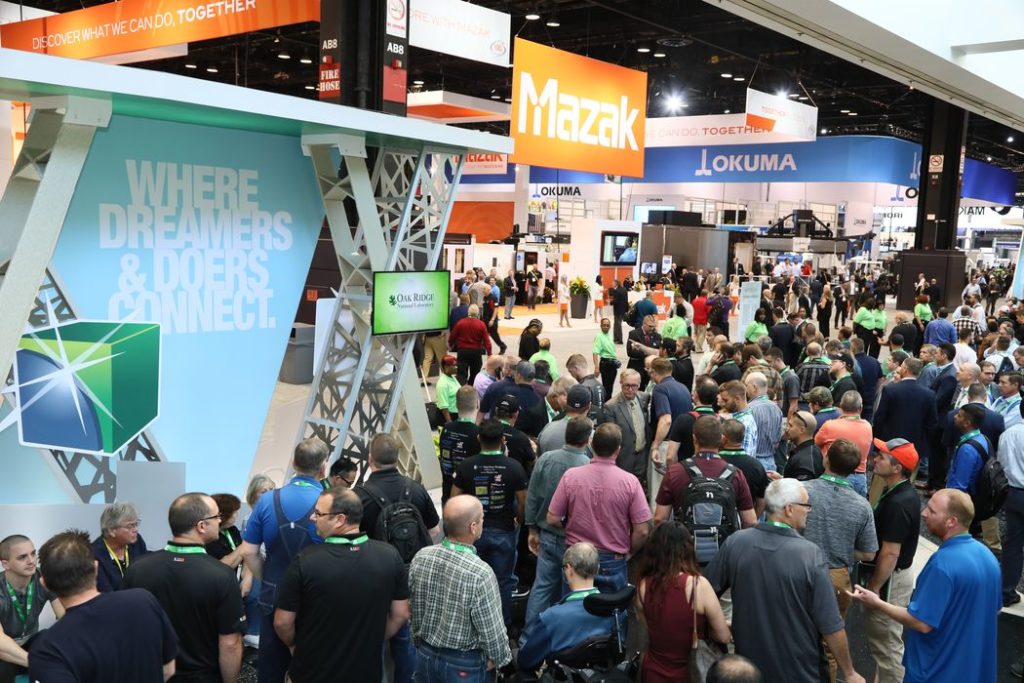
SPONSORED CONTENT
Additive manufacturing is relatively young as both technology and industry, growing rapidly to overcome hurdles to adoption.
As the technology and the industry surrounding it has matured, additive manufacturing (AM) has surpassed expectations as a viable manufacturing technology. Increasingly, industrial facilities will see 3D printers installed alongside traditional production equipment. 3D printing has seen great expansion in rapid prototyping, tooling, low- and mid-volume production, and some moves toward serial production. There remain, however, several hurdles to overcome for AM to achieve its full potential as a manufacturing technology.
For example, AM rapidly responded to impacts of COVID-19 on the supply chain through production of mask and face shield components. Even though that was true, companies that wanted to 3D print ventilator components struggled to find materials that were FDA-approved for extended contact with saliva with no out-gassing or VOC issues.
AMT – The Association For Manufacturing Technology has recognized and promoted the significant advancements that have been made to-date within AM and continues to see a high potential for even further advancement toward increased industrial adoption. AMT has identified four high-impact challenge areas for additive manufacturing that need to be addressed from an industry standpoint to accelerate this technology forward for future success in the manufacturing industry.
- Immature material availability
- Unstable production processes
- Inefficient paths to industrial certification/acceptance
- Relatively expensive unit-production calculations
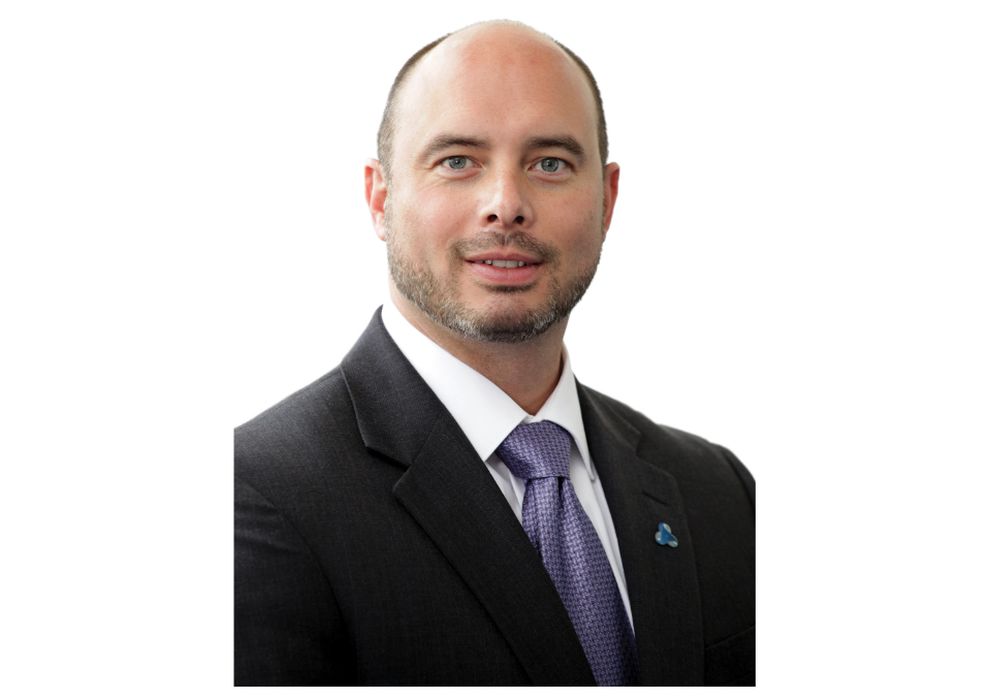
I spoke with AMT Vice President and CTO Tim Shinbara and Dave Burns, Senior Advisor, to AMT, and Principal and Founder, of Global Business Advisory Services.
Shinbara and Burns offer especially rich AM backgrounds. Shinbara has served as chair of ASTM’s F42.05 (Materials and Processes) and was a departmental technology thrust lead for additive manufacturing at Northrop Grumman. Burns was previously president and COO of the 3D printing company, ExOne, and is the former CEO of gear manufacturing giant Gleason Corporation.
In this first discussion, we will look into expert thoughts on materials and process considerations; in part two, we will delve into costs and acceptance.
Immature Material Availability
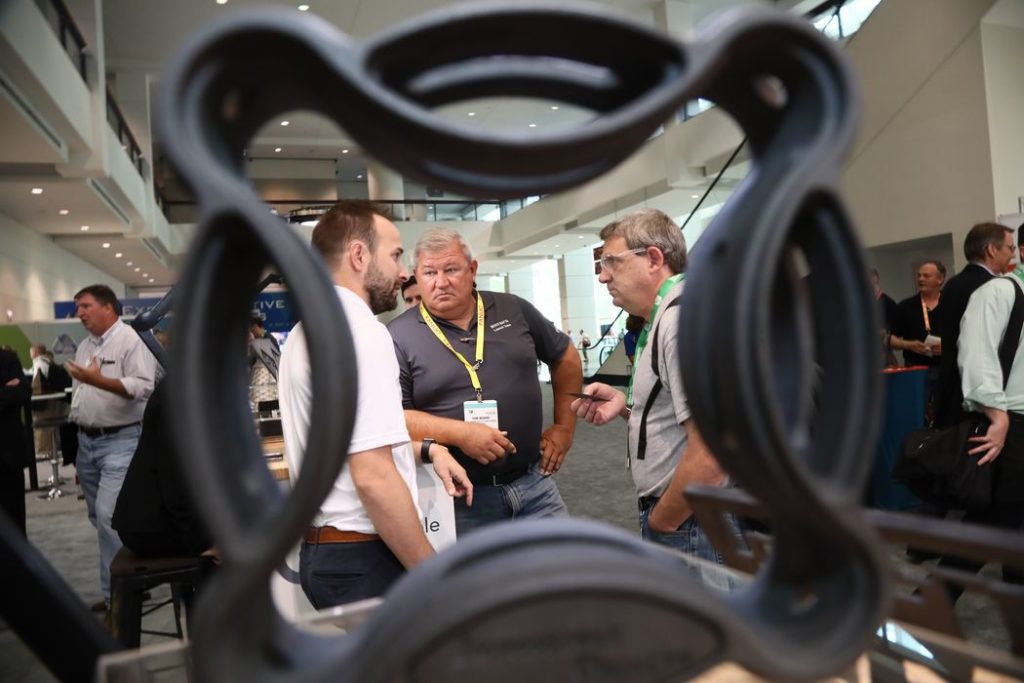
Shinbara starts our conversation by saying, “We’re still in a very high-potential world, so what effectively accelerates that path to adoption? It starts with AM material maturity.”
There has been steady, but slow, maturation of materials in both polymers and metals for additive manufacturing. Materials availability and predictable usage within a given system is a challenge not about standards development but, rather, insufficient predictability and consistency in material performance.
To draw a parallel with subtractive manufacturing, Burns points to 1018 steel, one of the most common, low-cost steel grades.
“Every piece of 1018 ordered is fundamentally qualified in the same way,” Burns said. “If I put it into three different machine tools, I get the same outcome. Now compare this to a metal powder for AM. Even though I can qualify it and make a powder that’s exactly 50 microns, if I put it in three different 3D printers, I’m going to get three different outcomes.”
Further, the metal powder is not finished once it exits the machine, and powders may yet react differently to post-processing on a machine-by-machine basis.
“It’s not enough to say that we can qualify or certify a material for AM. Why?” Burns asked. “Because we don’t yet know enough about what’s going on in the work zone to be able to control it to a level of predictability that is akin to machining 1018 bar stock.”
Beyond this initial layout there are additional material property issues. For example, if a material developer adds more nickel to increase tensile strength, does the enhanced material then have to be requalified?
Burns estimates that of the thousands of industrial materials that are commonly used in other processes every year, the percentage of those qualified for 3D printing is less than 20%. That represents a significant stumbling block for the production line.
“Just to get to the same place in materials qualification that we’re at today with other processes, we’ve got at least 80% to go,” said Burns. “That doesn’t even begin to talk about exploring nanoparticles and coated particles and all of these incredible things that are just going to change the way parts are ultimately made. The material side is immature but maturing, right? Fortunately, the distance between where we need to be and where we are is a straightforward but heavy commitment to R&D dollars.”
This R&D is already happening. Companies like EOS, for example, are working with predictive models, in-situ metrology, and analysis of melt pools, powder flows, and energy flows that are certainly enhancing material handling and process monitoring to ensure consistent results.
An Ipswich, Mass.., company called COSM offers custom-built Electron Beam (EB) wire metal 3D printing systems based on a new electron beam optics and control architecture that utilizes the electron beam as a simultaneous melt/measurement tool. Using its EB technology, it can monitor, measure, and control the process in real time. The company’s first prototype is being built for NASA as part of the Artemis moon project … because there is no separate metrology lab in outer space.
These types of development are helping 3D printer OEMs understand the mechanics of what works and why within their machines, and ongoing study is spreading these understandings across a broadening variety of both metal and polymer materials used on a variety of 3D printing technologies. Accurately developing, predicting, and using materials will see availability increase to a full suite of industrial AM materials that will eventually rival those seen in traditional manufacturing.
Unstable Production Processes
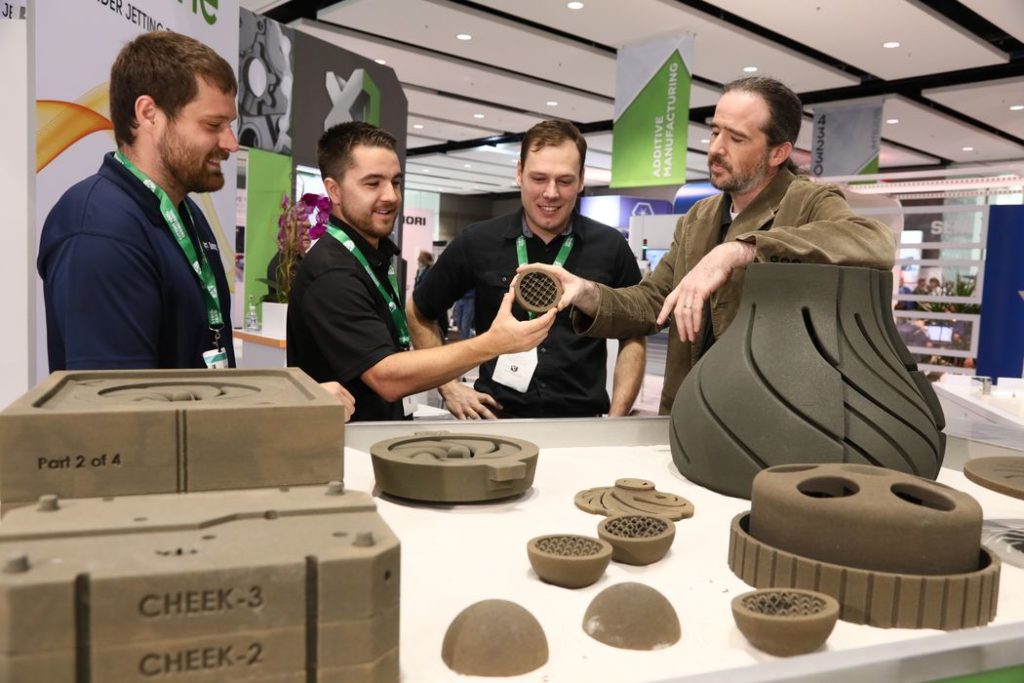
When it comes to production processes themselves in additive manufacturing, there remains continuing instability.
Acceptable results have been found in traditional technologies like CNC machining, where the industry has very good understanding of the physics and the physics are very straightforward. Whereas process capability metrics in other processes may be within 95% confidence to remain within parameters to get the same part, “We’re magnitudes off of that with additive,” Shinbara said. “Gauging repeatability and reproducibility (R&R) — understanding system variances, variance within individual machines, and production variances — are primary issues for the industry to move forward.”
Repeatability means: “Can a single instance repeat the same thing over and over and over again?” Reproducibility means: “Can I take a process and apply it to a different machine and get the same results?”
Shinbara explains the R&R concept of having a machinist use calipers to ensure that a manufactured part is within satisfactory variance.
“Can the manufacturer get the same measurement, within a particular tolerance, over and over again no matter who’s holding those calipers and no matter which comparable machine was used to make the part? Once this happens,” he said, “Tthe manufacturer has met the R&R standard and can therefore deploy it on the shop floor.”
Applying this to additive manufacturing for production is critical for getting this technology onto industrial shop floors. The goal is, of course, not to expect perfection; a total lack of variance is impossible. “We’re not scared of variance,” Shinbara said. “We’re scared of insufficient or widely varying results.”
Decreasing risk in the risk-averse manufacturing world is critical for management to approve seven-figure machine investments. These decision makers “have a lot of reasons not to go risky,” Shinbara acknowledged, and the AM industry “has to meet them halfway by showing stability.”
What that means is that ultimately error introductions need to be “very, very tight” while process capabilities should be “really, really wide.”
Burns noted that much of this will come with time — and investment.
“Many of the companies and people entering the additive space don’t have a background in higher volume manufacturing,” Burns said. “They extrapolate from successfully printing a part a few times and believe that they could repeat it one million times. There really is a gulf of understanding in what repeatability and reproducibility mean among those who were and were not brought up through the world of high-volume manufacturing.”
Secondly, another reason that the pace of AM innovation has been relatively slow within manufacturing technology is that it has been largely self-funded.
These gaps in both understanding and funding are proving key challenges for additive manufacturing to overcome when bringing new technologies to market.
“I think some of the disappointments we’ve seen is because venture capitalists have come in, made investments, and said, ‘I don’t understand why you’re not selling that thing you’ve got in your lab’,” Burns continued. “As a result, developers rush to a show and say, ‘See what I’ve got.’ A few people buy it and the next thing that happens is you see a review in a journal where somebody says,’ This thing doesn’t work.’ Well, it would’ve worked if we’d left it in development for another year and hadn’t forced it to market.”
The need to educate “impatient money” is an understudied phenomenon, according to Burns, because it hinders the development of stable, reliable, and repeatable processes and products ahead of bringing them to market. In short, that extra year in the lab could prove crucial to ROI.
These growing pains in a quickly-growing manufacturing technology can be, and are being, overcome as the additive manufacturing industry continues to mature.
In part two of this conversation, we continue to look at existing high-impact challenges that additive manufacturing is overcoming.
AMT and AM
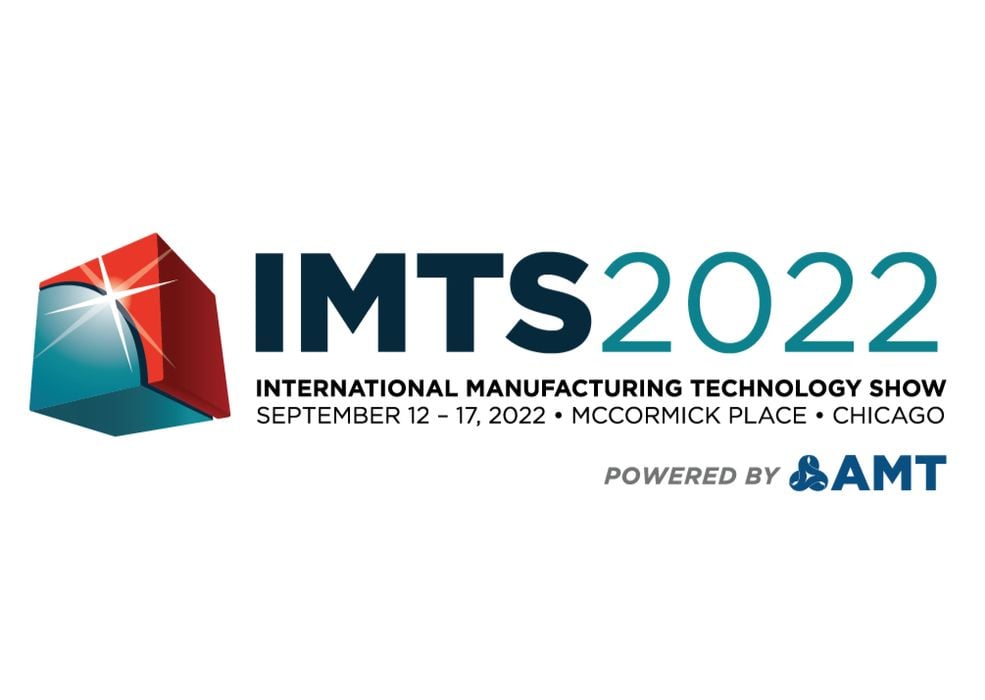
AMT represents and promotes U.S.-based manufacturing technology and its members — those who design, build, sell, and service the continuously evolving technology that lies at the heart of manufacturing. AMT also owns and produces IMTS – The International Manufacturing Technology Show, North America’s largest manufacturing technology event, owned and produced by AMT.
“Our main mission is to ensure that the manufacturing technology industry continuously improves,” said Shinbara. “We’re constantly looking at trends and making sure we provide forward-looking information that supports our members and increases their competitiveness. Right now, our members are focused on additive manufacturing because it has the highest potential for growing the overall size of the manufacturing industry and highest potential for accelerating that growth. However, it also has the highest challenges for adoption.”
Burns adds that COVID-19 thrust AMT to the forefront because “the capabilities of the U.S. manufacturing base went from being an interesting intellectual discussion to apparently a national priority. Where is the nation going to turn to answer that question? I think, logically, AMT is a perfect place to ask those questions because it has the resources and a decades-long history of answering those questions, including the role of AM within the larger manufacturing community.”
To address these challenges, AMT can help drive the industry conversation forward through such actions as facilitating committees to set standards, to set industry direction and to discuss future ways that the organizations can communicate. This is also exemplified through AMT’s events.
On Thursday, September 9, at 10 a.m. ET, AMT hosts the webinar, Starting up a 3D Printing Company, world-renowned researchers Thomas Kurfess, Ph.D. and Lonnie J. Love, Ph.D., from the Oak Ridge National Laboratory. They interview entrepreneur Austin Schmidt, co-founder and president of Additive Engineering Solutions – the first company to commercialize Large Format Additive Manufacturing (LFAM) as a contract service. (This is the first in a series of webinars AMT is hosting with Krufess and Love.)
November 2-5, AMT hosts MFG2021 + MTForecast in Denver, Colorado. The event brings together the manufacturing technology industry to network and gain insight on economic, market, and technology trends. In, Technology Insights – How Additive Manufacturing Can Catapult Your Business, successful AM entrepreneurs discuss how to harvest value from software technology and prepare for the interconnected ecosystem digital provides. Visit www.MFGMeeting.com.
Another example is AMT’s Emerging Technology Center (ETC) at IMTS. The ETC has promoted significant AM advancements and notably collaborated with the Manufacturing Demonstration Facility (MDF) from Oak Ridge National Laboratory. Most recently, AMT and the MDF produced two on-demand series of educational, informative, and even entertaining video programs: “Project Moonshot” and “Tom & Lonnie Chats.” The programs focus on how they tackle some of today’s biggest manufacturing challenges, including:
- AM substitutions for castings for machine tool bases, tooling, and large metal parts
- New technology that can boost metal removal rates by 300 percent
- Three different hybrid AM/subtractive machining centers and hybrid CAD/CAM technology
- An Overview of Metal Additive Manufacturing (AM) Systems: Pros and Cons
- Supply chain responses to COVID-19 featuring AM technology
- Computed tomography-based metrology solutions
- Cybersecurity, and much more
AMT and MDF will again collaborate for the ETC at IMTS 2022, which runs from September 12-17, 2022 in Chicago., Ill. Details will be announced closer to the show and posted on IMTS.com.
Via AMT