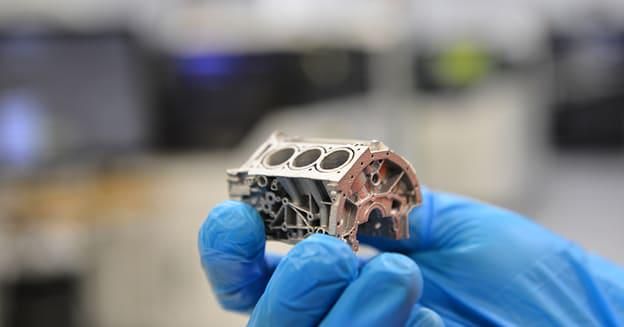
Ford and Audi have the latest implementations of 3D printing in car production.
To the additive outsider, it sometimes seems that there are two prevailing opinions on industrial 3D printing.
One side says that additive manufacturing (AM) is the wave of the future, disrupting where, why and how we make things on a global scale. The other says the technology is too slow and that it can’t be viable for mass production.
Like many sets of opinions, the truth lies somewhere in the middle—AM likely won’t supplant injection molding for mass production of many resin parts, but neither is it confined to the lab or design office. Recent news from the automotive industry shows as much. In many cases, AM’s role in the automotive industry is not to compete with established processes for production parts, but rather to solve other problems and support continuous improvements. AM’s niche can often be found in areas such as customization, jigs and fixtures and light weighting.
These recent pieces of news from major automakers including Ford, Audi and Porsche incorporating AM technology into their businesses are exciting examples of how engineers are continuing to find meaningful applications for AM in the industry.
Audi and the EOS M 400
A recent development partnership between Audi and EOS has reached a new milestone: Audi has moved entirely to AM for hot forming at its Metal 3D Printing Centre in Ingolstadt to produce selected tool segments. AM with EOS technology is used in 12 segments of four tools for hot forming. Plans call for significantly more segments to be printed this way. Audi uses the tool segments produced with the EOS M 400 system in its press shop to make body panels for models including the Audi A4. The company plans to use the same process for future electric vehicles. Several hundred thousand parts have already been produced using the 3D-printed tools and have been installed in select models.
Audi’s hot stamping tools and high-pressure die casting tool inserts measure up to 5 x 3 meters (approximately 16 ft x 10 ft), and the individual 3D-printed tool segments weigh up to 120 kg and are 400 mm long (264 lb and 15 in). Tool segments of this size and complexity typically require several weeks to manufacture, but 3D printing can speed up the process without sacrificing quality. It can also build conformal cooling channels into the part, providing more effective cooling and better quality parts.
“From initial qualification by EOS to internal further development and refinement of the entire process chain through to standardization of a new production method, we are now reaping the fruits of years of development within Audi’s production organization,” said Matthias Herker, technical project manager at the Audi Metal 3D Printing Centre. “Whenever conventional manufacturing methods reach their limit, we use additive manufacturing—which lets us meet quality standards and comply with production times.
ExOne and HP Additive at Ford
A new patent-pending process developed by ExOne and Ford Motor Company for binder jetting 6061 aluminum—one of the most commonly used aluminum alloys in the world—is purported to deliver final parts with 99 percent density and material properties comparable to traditional manufacturing.
In a project co-funded by Ford and ExOne, a team of engineers, material scientists and manufacturing experts has developed a process for rapid and reliable binder jet 3D printing and sintering of aluminum that delivers properties comparable to die casting.
Some aluminum alloys can be 3D printed today using lasers, but the process is much slower than the one developed by Ford and ExOne. The new process is expected to increase Ford’s efficiency by allowing the company to affordably produce complex parts uniquely designed for AM, enabling size and weight reductions, part consolidation and performance improvements.
“This is a breakthrough in making 3D printed and sintered parts for the auto industry,” said Harold Sears, Ford technical leader for additive manufacturing. “While the 3D-printing process is very different than stamping body panels, we understand the behavior of aluminum better today, as well as its value in light-weighting vehicles. High-speed aluminum 3D printing paves the way for other opportunities that we’re just now starting to take a look at because of the ability to do complex parts with aluminum that previously weren’t possible.”
The innovation came about through the process of binder jetting. It uses a digital file to quickly inkjet a binder into a bed of powder particles such as metal, sand or ceramic to create a solid part, one thin layer at a time. When printing metals, the final bound metal part must be sintered in a furnace to fuse the particles together into a solid object. The heating process reinforces the strength and integrity of the metal, and while the process for sintering stainless steel is well understood, achieving high densities has been a challenge for the technology.
Read more at ENGINEERING.com