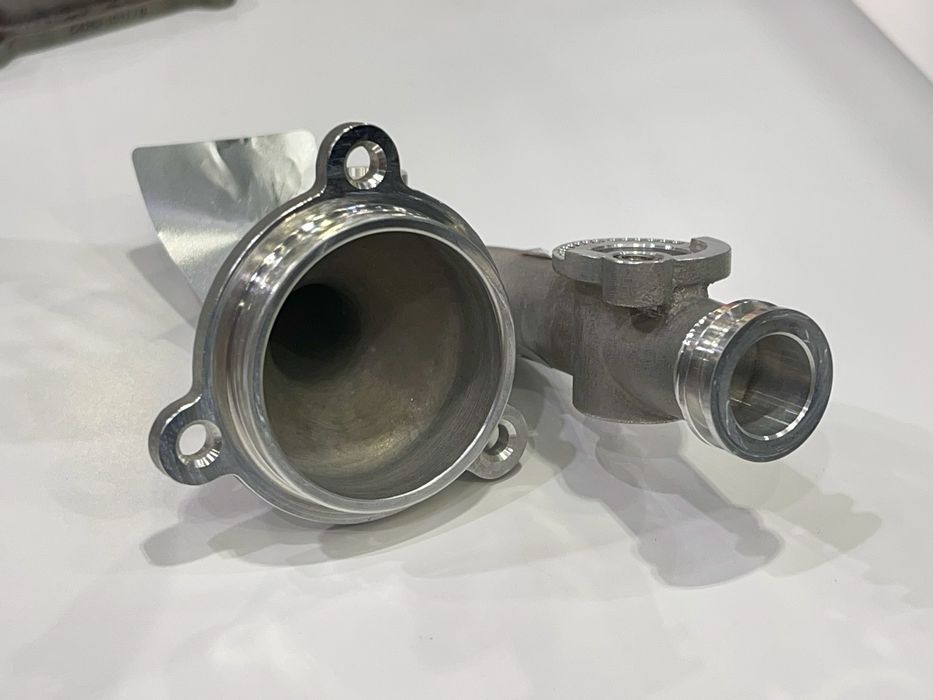
Additive Industries seems to be continuing with their never-ending quest for efficiency.
I had a chat with Kartik Raom, Additive Industries’ Strategic Marketing Director, and learned more about their recent progress. I’ve followed the company since their startup days years ago, and they were among the first to recognize the importance of efficiency.
Their system was perhaps the first having a design incorporating the several steps required for metal 3D print production. This enabled customers to easily shunt work through all stages in an efficient manner. Meanwhile, the competitors of the day were marketing only “the printer”, and leaving the rest to the clients to figure out.
That focus on efficiency seems to be still top of mind at Additive Industries. In discussion, I learned that their latest equipment is the only one on the market that has multiple print cores in the same production line. The use of multiple cores can significant increase capacity.
They’ve continued to tune their management software, and it is possible for a single operator to easily manage multiple systems. It’s important to remember that one of the major cost components of using 3D print technology is the operator time. While the unit cost of machinery may drop over time, the cost of labor tends to increase.
One of the key ways they’ve accomplished this is through a data service to the operator. They provide APIs through which management dashboards can be created. This allow operators access to highly focused information for their activities.
Additive Industries has also increased the number of redundant components within their systems. This not only makes failures less frequent, but also enables a unique capability: maintenance without shutting down everything. That’s critically important for production operations that usually want to keep running the hardware 24/7.
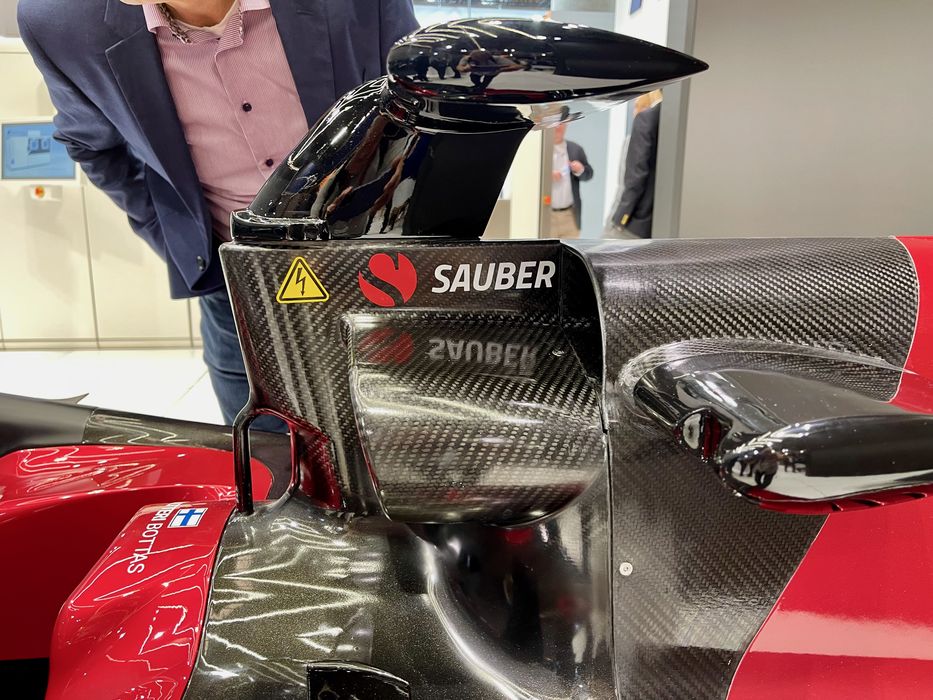
They’ve mostly been focused on the automotive sector, as evidenced by their partnership with the Sauber F1 team, and Alfa Romeo. Apparently they’ve produced over 250 different parts for F1 cars. However, a growing segment in their universe is aerospace, which has been dominated by a select few other providers. Here it seems that Additive Industries wishes to diversify their application areas.
Their focus on efficiency is not just with respect to machine operation. They’re also focusing on efficiency for the customer applications.
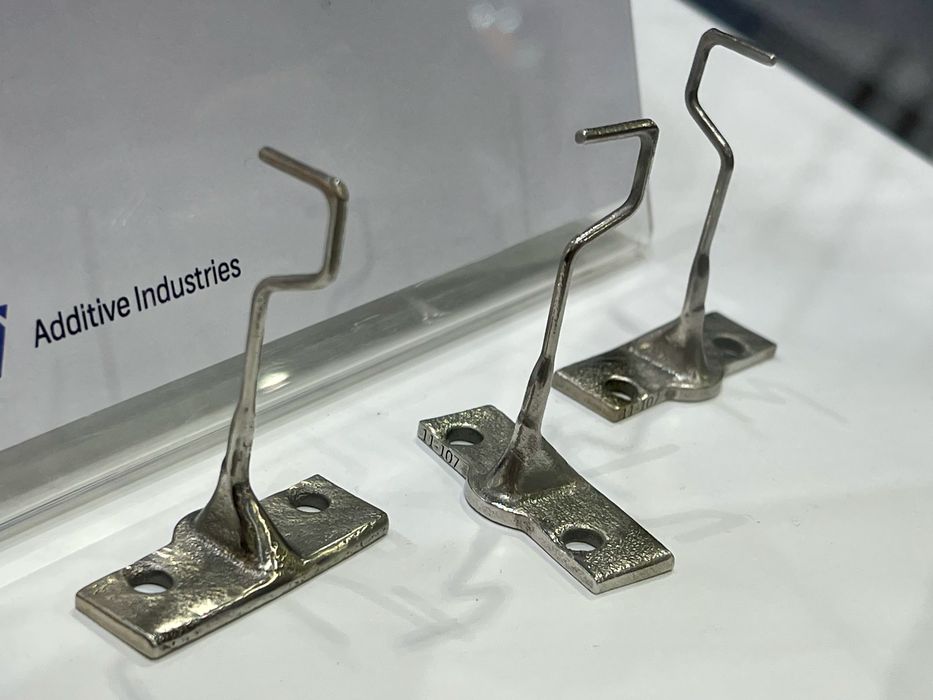
One example of this is shown above. What appears to be a rather straightforward part actually has quite a story behind it.
This is a special corrosion resistant needle for use by Volkswagen to deposit a line of glue for the rubber door seals. Printing this item would seem like a fairly standard design, but it’s carefully bent to integrate with the robot and part geometries.
However, the surprise here is that when this needle was made using conventional approaches, it was quite difficult. It involved precision welding of seven or eight tiny titanium segments, which was costly and difficult to do, as the needle requires a 1.3mm internal channel with 0.25mm walls.
Raom explained that this application in particular “opened the eyes” of VW for use of 3D printing technology in factory tooling, and it’s expected there’s more to come.
All of this has raised the profile of Additive Industries significantly in the eyes of the advanced automotive companies. Raom said that “blue chip companies now recognize them”. Apparently the company sold one system to a client specifically for use in making parts for a particular automobile design.
This is all good news for the company, and it seems their focus on efficiency has been paying off.