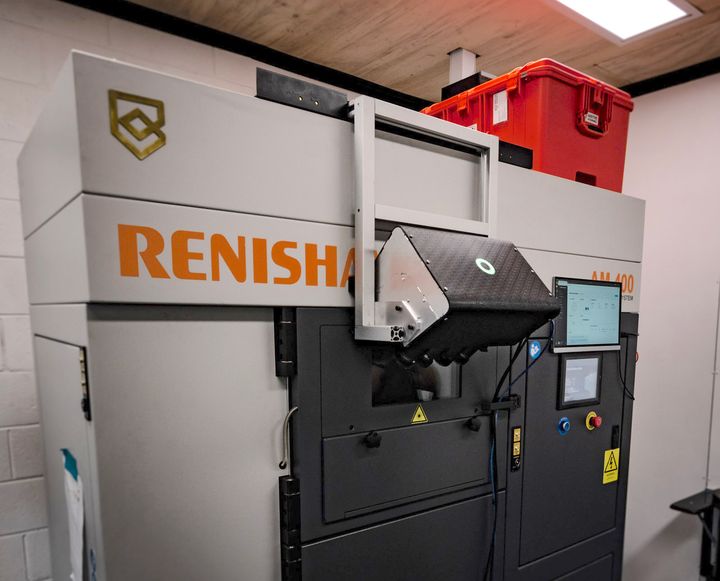
A startup company has developed a unique method of certifying the quality of 3D printed metal parts.
Australia-based Additive Assurance started in early 2016, but was operating in stealth mode until fall 2019, when they revealed themselves at Formnext 2019. Somehow we missed them at this event, but a year later it’s time to catch up.
I spoke with Dr. Andrey Molotnikov, who is one of the founders of the company, and now its Chief Scientist. In 2016 one of his students came up with a new concept for observing PBF operations, and they decided to form a company. That student, Marten Jurg, is now the CEO.
The question of part quality in additive manufacturing is quite timely, as an increasing number of industries now partake of the technology for production purposes. Unlike prototyping, production parts must meet quality specifications each and every time.
As clients move towards production usage, this has led several manufacturers of PBF metal 3D printers to develop quality systems. Typically this is done by adding a considerable amount of sensors in the machine that rapidly capture every detail of the operation.
For example, some quality systems painstakingly trace the movement and performance of the laser meltpool across the powder surface. By monitoring this activity, they hope to understand when the solidified metal particles aren’t quite correct.
But there’s a major problem with this approach: data size. Bajillions of data are collected in every print job, with plenty of sensors spewing data blocks in sub-second time. For larger print jobs or those with higher resolution, the data is so large it cannot be reasonably processed, and certainly there are challenges in doing so in real-time.
Additive Assurance AMiRIS
Enter Additive Assurance’s AMiRIS system. They describe it as follows:
“AMiRIS is an independent in-situ process monitoring solution for Laser Powder Bed Fusion Metal Additive Manufacturing from Additive Assurance.”
Okay, but how does it work? It turns out the answer to that question is quite amazing.
Rather than focusing on the minutiae of all machine operations, AMiRIS instead takes account of an entire layer at a time. The system is essentially an imaging apparatus that observes each layer’s full surface.
Their process is reminiscent of astrophotography, where long and repeated exposures are captured and then “stacked” together to form a more complete image. This is essentially what’s happening with AMiRIS: each layer gets a complete image of what actually happened. Here’s a screenshot of what sorts of things appear in such an image:
If you look closely you can see some variations in the colors of the part. This might represent different effective energy depositions, for example. By capturing images with different wavelengths and applying filters, multiple aspects can be observed. Molotnikov told me they can actually recognize “single tracks” of laser trails.
In a meltpool there are multiple points of data available so they can more deeply understand the physics of what’s happening during melting and solidification.
There is much more insight available with whole images, particularly when they are layered on top of each other to produce a kind of “CT scan” for the print job.
Now the interesting part happens: these are images, and they can be pushed through an AI-style image recognition system that may have been trained to identify issues and problems. Thus they can very quickly determine, for example, if a given print job has gone awry and allow the operator to stop the print and save some expensive material.
Hardware-wise, AMiRIS is simply an imaging box that is strapped to the side of a metal 3D printer so that it can observe through the machine’s optical window. Thus it is theoretically possible to attach it to any PBF machine with a window. Currently the company has developed solutions for several popular metal 3D printers.
I asked whether the solution could work for thermoplastic PBF processes, and Molotnikov said yes, that it was entirely possible technically, but the value of plastic parts is far less than their metal counterparts and thus it was not worth doing, at least at this stage.
There are many, many possibilities for this technology. For example, it might be possible to use the system to “learn” the best ways to 3D print a particular material on a given 3D printer through AI examination of these images. Then the optimal print parameters could be identified. In other words, this system could theoretically automatically generate print profiles!
Another possibility could be to actually rank the quality of parts produced on different machines in order to determine the “best” machine for the job. I’m not sure that Additive Assurance is considering this approach, but it would certainly be interesting if they did.
You might be wondering of the costs for AMiRIS. It turns out the hardware is provided at no charge, but you must subscribe to the company’s cloud processing system to receive results. I’m told the monthly fee is around US$4-5,000, which is actually an incredibly low cost when you consider that amount might be the cost of a single print failure. Additive Assurance also offers on-site installations for those companies more concerned with security.