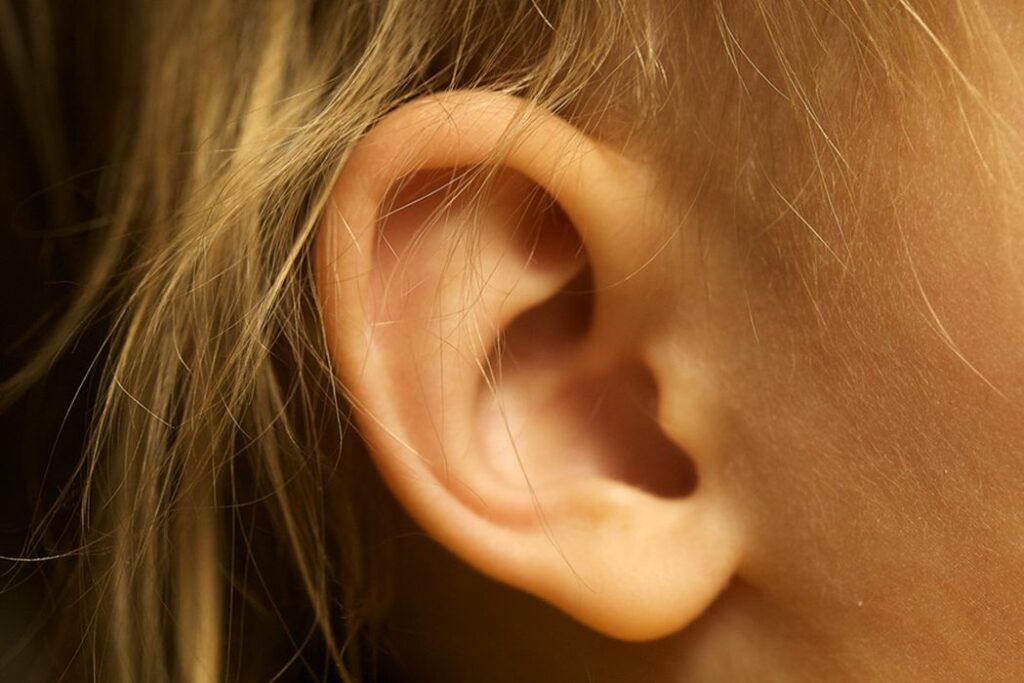
Charles R. Goulding and Julia Wallace examine the ramifications of the recent announcement of a successful 3D printed ear implant.
A Successful 3D Printed Implant
In March 2022, a woman born with a small, deformed ear (a condition known as microtia) was given a new ear, 3D printed by 3DBio Therapeutics from her own cells. Some of her chondrocytes (cells responsible for cartilage formation) were isolated from a biopsy and nurtured as they multiplied into billions of cells.
Next, they were mixed into a collagen-based bioink and inserted into a specialized 3D bioprinter. A mirror image of the patient’s healthy ear was printed in under ten minutes, then implanted under her skin on the side of her head. The skin was tightened there, and a healthy-looking ear now sits in that spot.
This technology has been in development since the 1990s when an ear was grown on the back of a mouse using cow cartilage. In 2016, the experiment was replicated by a Japanese team of researchers using human stem cells, successfully growing a 2-inch human ear on the back of a rat.
In recent years, human ears have been successfully 3D printed using human cells, presumably those of the potential implant recipient. Now, this technology has been used practically, with the ear actually being attached to a human head. This is part of a clinical trial of 11 patients, aged 6 to 25, who will be monitored for 5 years to ensure the safety and efficacy of this surgery.
This surgery is a huge win for the thousands of people with microtia and anotia (a condition in which the entire external ear is missing at birth). The only previous option of ear reconstruction for these people involves harvesting cartilage from the ribs, which is then carved into the shape of the ear by a surgeon before attaching it to the head.
This method causes pain to the cartilage donor (possibly the patient themself), and its aesthetic success is dependent on the artistic skill of the surgeon. 3D printing eliminates the inpatient cartilage-removal surgery and allows the new ear to be exactly symmetrical in design to the opposite one.
The Future of Organ Printing
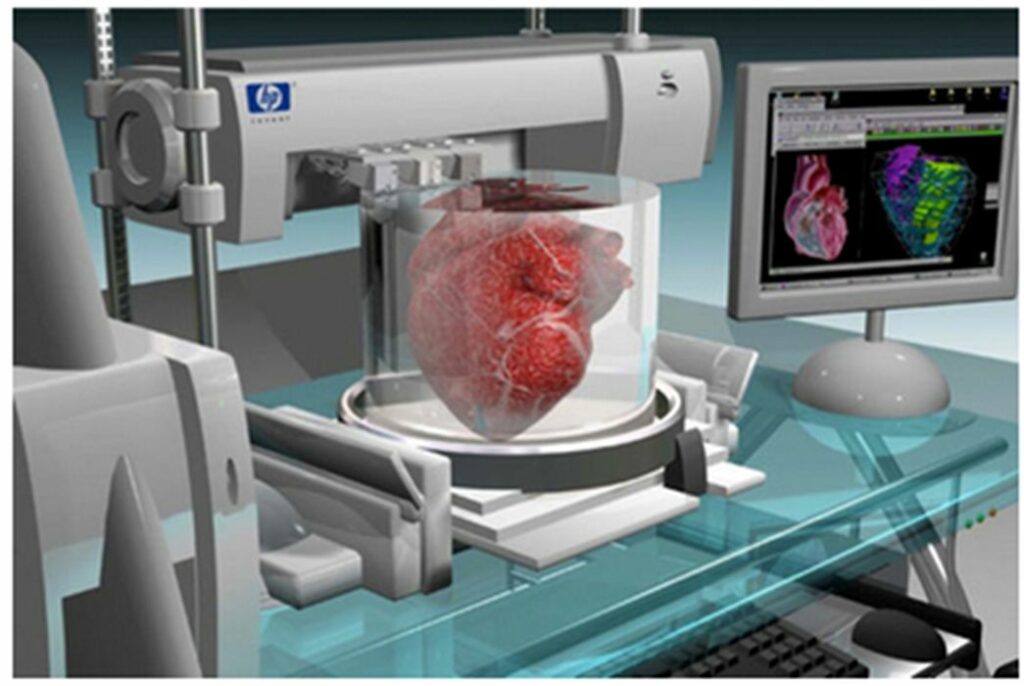
While the success of this implant does show tremendous success in the field of bioprinting organs, there is still a long way to go before more complex organs can be 3D printed and implanted into human patients.
As Dr. Adam Feinberg, professor of biomedical engineering and materials science and engineering at Carnegie Mellon University, said for a front-page article in New York Times, the jump from an ear, which is mostly just for cosmetic purposes, to a fully functional liver or spinal disk is huge, “. . . but it’s more realistic if you’ve got the ear.”
This sort of technology is being actively developed, though. Researchers have had success in printing full hands, and a full human heart has been produced in Dr. Feinberg’s lab.
The Research & Development Tax Credit
The now permanent Research and Development (R&D) Tax Credit is available for companies developing new or improved products, processes and/or software. Eligible costs include U.S.-based employee wages, cost of supplies consumed in the R&D process, cost of pre-production testing, contract research expenses, and certain costs associated with developing a patent. As of 2016, eligible startup businesses can use the R&D Tax Credit against $250,000 per year in payroll taxes.
3D printing can help boost a company’s R&D Tax Credits. Wages for technical employees creating, testing and revising 3D printed prototypes can be included as a percentage of eligible time spent for the R&D Tax Credit. Similarly, when used as a method of improving a process, time spent integrating 3D printing hardware and software counts as an eligible activity. Lastly, when used for modeling and preproduction, the costs of filaments consumed during the development process may also be recovered.
Whether it is used for creating and testing prototypes or for final production, 3D printing is a great indicator that R&D Credit eligible activities are taking place. Companies implementing this technology at any point should consider taking advantage of R&D Tax Credits.
Conclusion
The progress being made in 3D printing organs and the newfound success of implanting a 3D printed ear is clearing the way for safer and faster organ transplants. The reality of creating a new organ from a patient’s own cells severely lessens the chance of the patient’s body rejecting the transplant, and the speed at which the ear was made creates new hope for people who wait months or even years for organ donations.