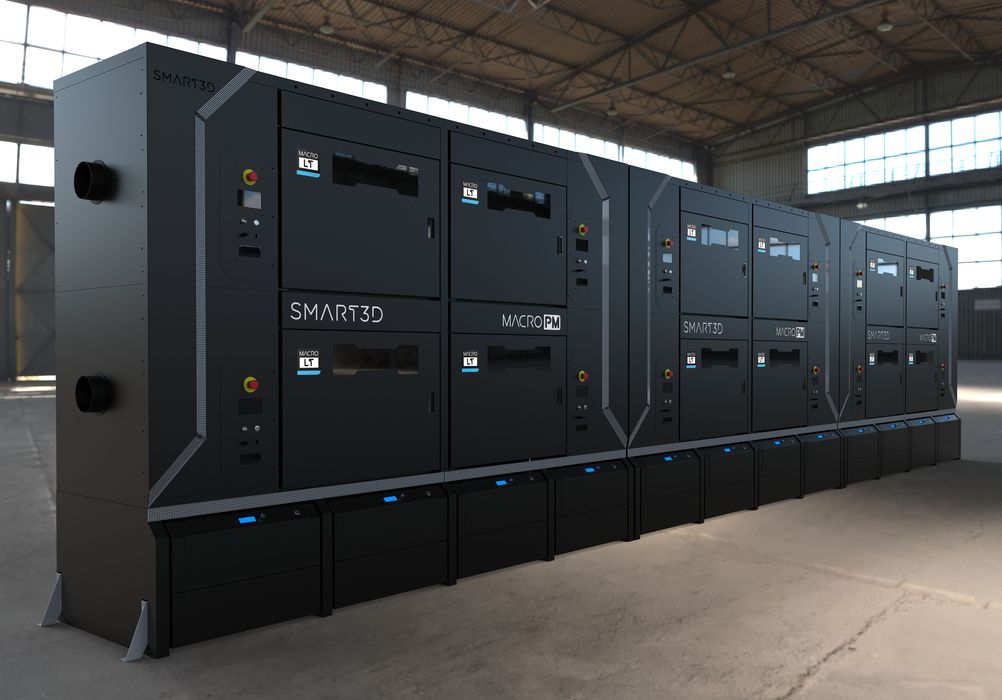
I had a look at Smart3D’s manufacturing system, the MACRO, which offers both regular and high temperature additive manufacturing options.
You may have heard of Smart 3D, as they are the Argentinian manufacturers of the well-regarded Kodak Portrait desktop professional 3D printer. Nowadays they have a separate line for industrial 3D printers that leverages their expertise.
The flagship product in their industrial line is the MACRO series, a system that’s designed in modules, with both LT and HT versions. Let’s break it down:
- The MACRO has two styles: PU and PM
- The PU is the prototyping unit, and is used to develop jobs intended for manufacturing
- The PM is the production unit, and is used to rapidly produce objects
- PM units can be added as required to grow throughput through parallel operation
- All units can be centrally controlled
- Massive 350 x 350 x 400 mm build volume
- Dual extrusion, enabling use of soluble support for highly complex 3D prints
- All units offer activated carbon and HEPA filters for safe use with engineering materials
- All machines provide remote monitoring and control, include a live camera views
- The LT’s nozzle can hit 500C, and build chamber 120C
- The HT’s nozzle can hit 500C, and build chamber hit 200C
- LTs can print with ABS, ASA, BVOH, PA 6/66, PA12, PAHT, PAHT CF, PC-ABS v0, PEEK, PET-g ESD, PP CF, PVA, Tough PLA, TPE 60A, TPU 98A
- HTs can print with all the above plus PEEK CF, PEKK, PEI ULTEM 1010, PEI ULTEM 9085, PPSU
- The LT’s accuracy is 0.2mm
- The HT’s accuracy is 0.05mm
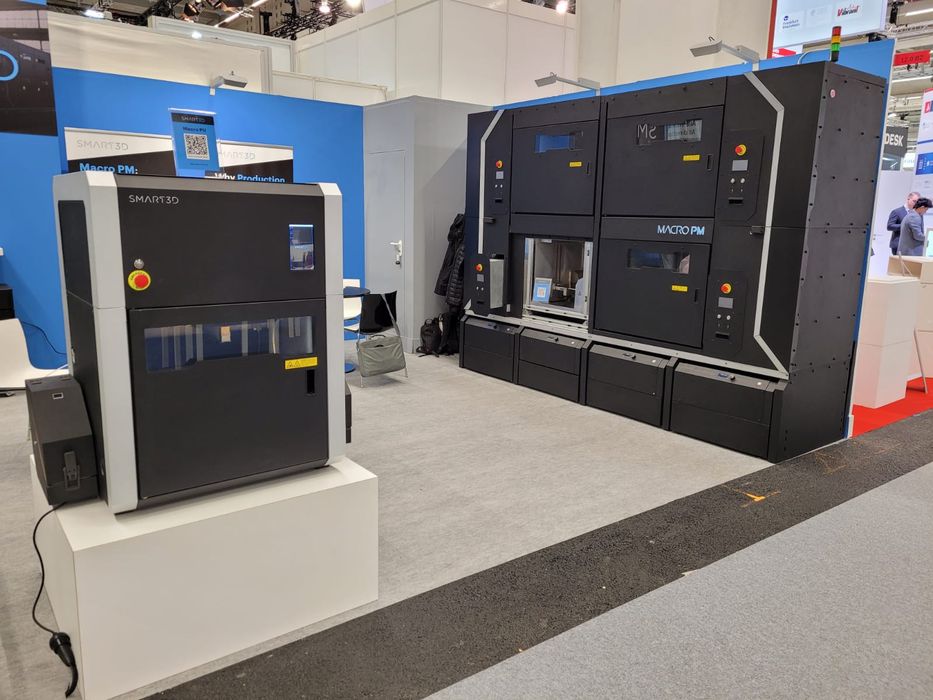
The idea is to build a configuration that matches the needs of the manufacturer. Typically there would be a PU for engineers to test out jobs and refine the print parameters to optimal state.
Then there would a number of PM units to match the manufacturing throughput needs. These could be either HT or LT types, depending on the specific needs of the operation. The throughput would be achieved by ensuring a sufficient number of build chambers to produce the required objects per week.
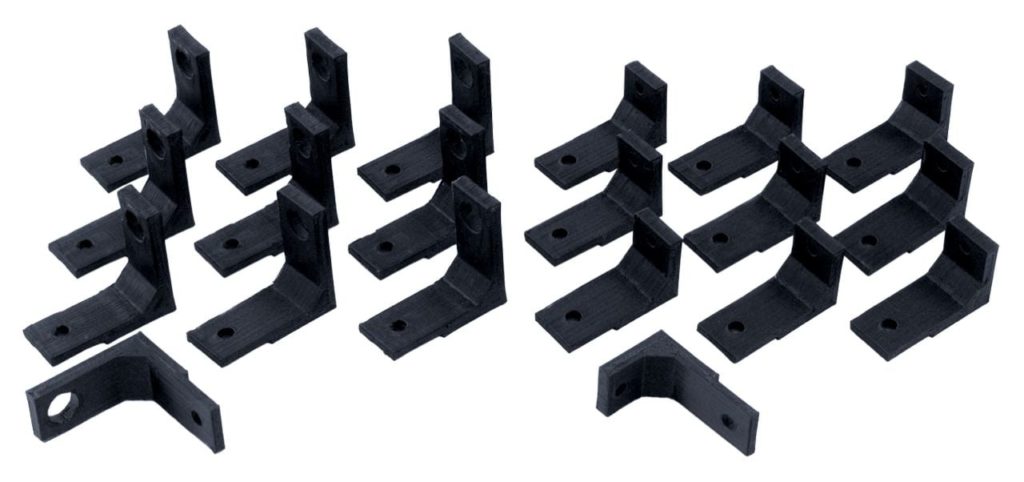
One of Smart3D’s clients, RGF in Germany, has been using the PM system for some time. Managing Director at RGF Thomas Meurers explained what they are using the system for:
“The first need was to build spare parts on demand. Our partners’ machines are very different from one another, and we have needed to build parts for hundreds of machines. Initially we worked with the parts we found would be easy to produce with additive and generate the higher time and/or cost savings. We have gradually become more proficient in the complexity of parts we can produce and are currently fully capable of designing for AM and working with multiple materials. The technology is really valuable for highly complex parts.”
He added:
“Our need was to be able to manufacture many equal or different parts at the same time. We compared the Macro platform to SLS solutions, but we were convinced by the strong and good- quality parts at much lower material costs. It also gives us a much wider range of end-use materials. We have only used the manufacturer’s materials so far, but having the ability to source any filament if a partner’s application requires it is a great benefit.”
3D printers are now specialized for use, and it seems that Smart3D’s MACRO system is definitely configured for manufacturers.
Via Smart3D