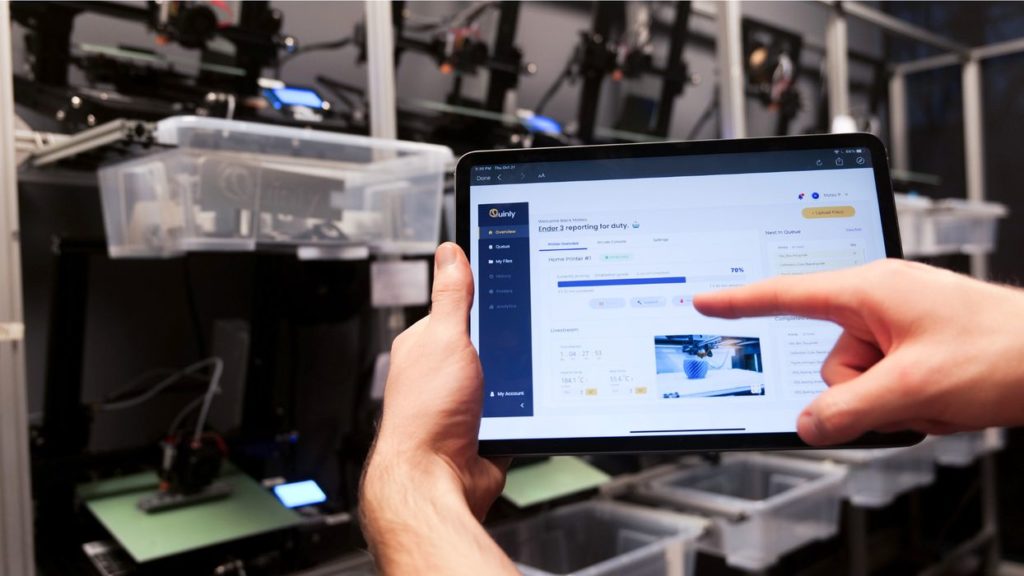
I spoke with 3DQue representatives to find out the latest on their unusual 3D printing technology.
The company was founded only a few years ago, with intentions of leveraging their VAAPR print bed adhesion automation technology in the manufacturing market. VAAPR allows a 3D printer to automatically release a completed print after the job finishes, meaning human labor is eliminated.
They have developed an implementation of the technology they call “qPod”, which is essentially an array of VAAPR-equipped machines. These would operate in parallel, pumping out part after part with only a requirement to feed the system new filament once in a while.
However, they got a bit sidetracked over the past year.
Quinly for Desktop 3D Printers
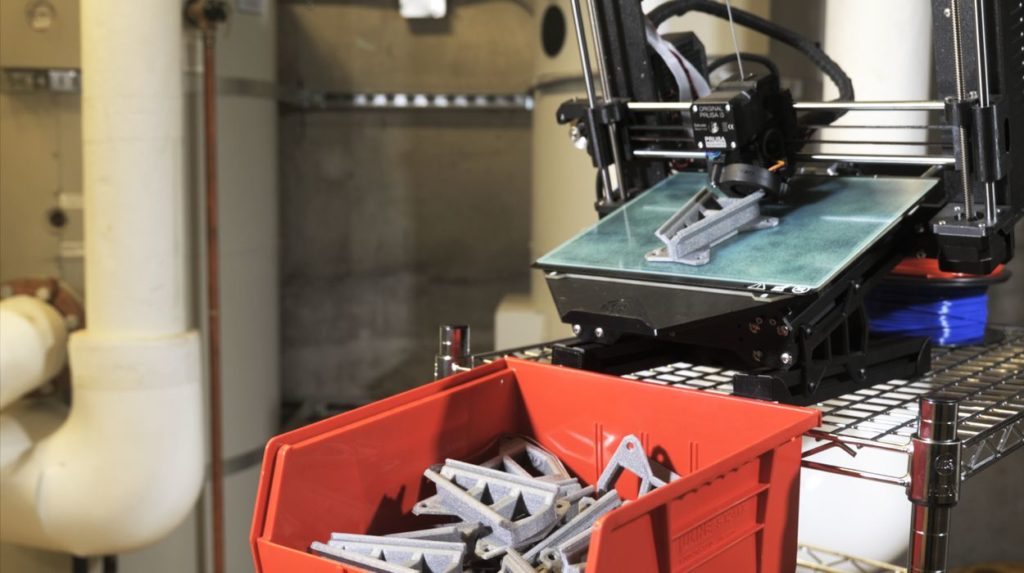
During the pandemic there was much distraction for manufacturers with destroyed supply chains. While some opted for well-established 3D print solutions to solve their missing component woes, it became challenging for 3DQue to install their innovative and unusual qPods.
They shifted to production of the Quinly, an implementation of VAAPR for inexpensive desktop 3D printers. These would put the device at an angle, where completed prints would literally slide off when done, effectively providing near-continuous production.
After developing Quinly versions for a variety of popular desktop machines, 3DQue is back at their original manufacturing goal to produce smart farms with fully automated 3D printers.
3DQue Manufacturing
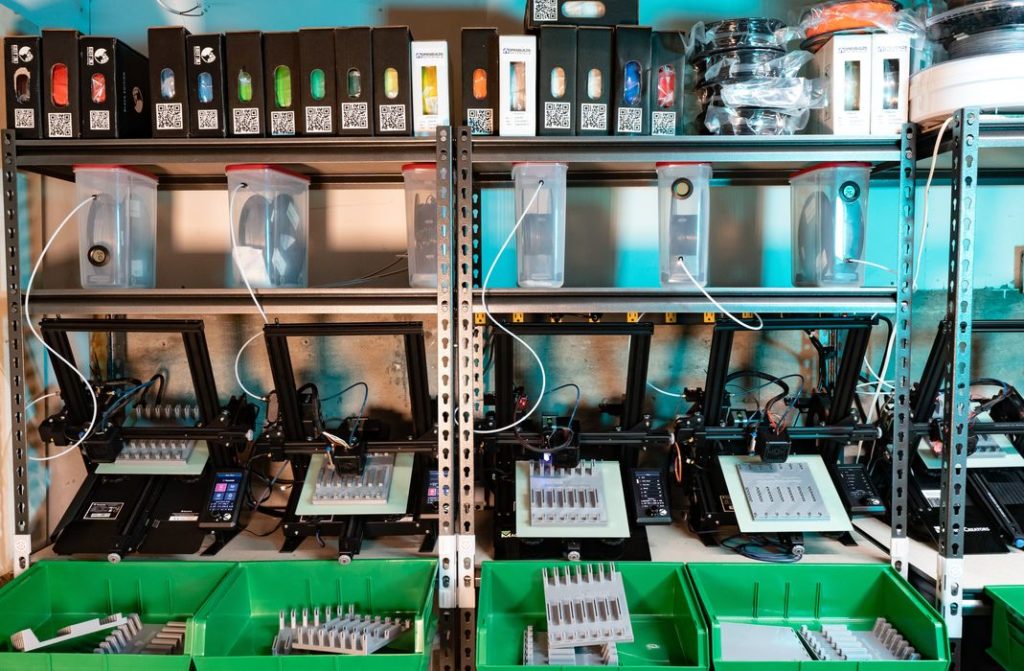
3DQue founder Mateo Pekic explained they now have suppliers putting qPod-powered 3D printers at customer sites on assembly lines, and that they are planning to do so at no less than ten different manufacturers, with up to 1000 machines in their customer manufacturing network.
One unnamed company is using a Quinsy-modified Prusa MK3S machine for their operation, and these pilot installations will typically use only one machine per site.
Pekic explained:
“We discovered the Quinly conversion kits are platform agnostic. They can work with any type of machine, and could automate metal or plastic 3D printing. This requires only slight machine modifications, and the rest is done in software.”
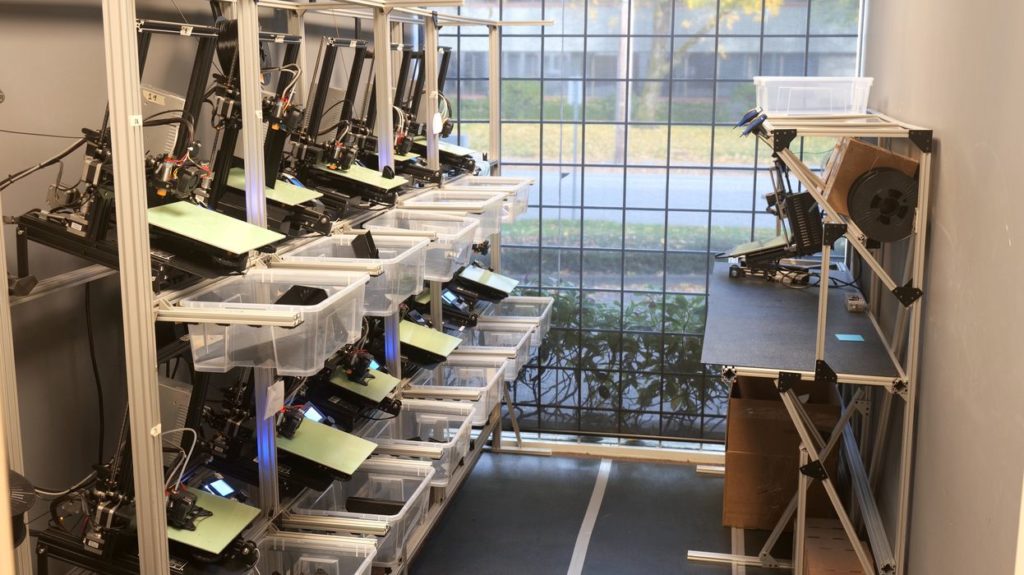
Now the company is leveraging that discovery in their manufacturing products by supporting different types of printers with their automation solution. Pekic continued:
“It’s tuned for every supported printer, and you end up with an automated farm system you can plug any system into. You don’t have to worry about specific hardware. It’s completely automated, even with mixed machine types. Our Pro and Enterprise options make the experience much simpler, and automatically route jobs to the appropriate machine.”
3DQue does offer a free version of their system, which supports a single 3D printer 24/7, and includes all tools required for job queuing and management. It even does basic checking of GCODE to remove interference from automation activities.
QuinlyVision
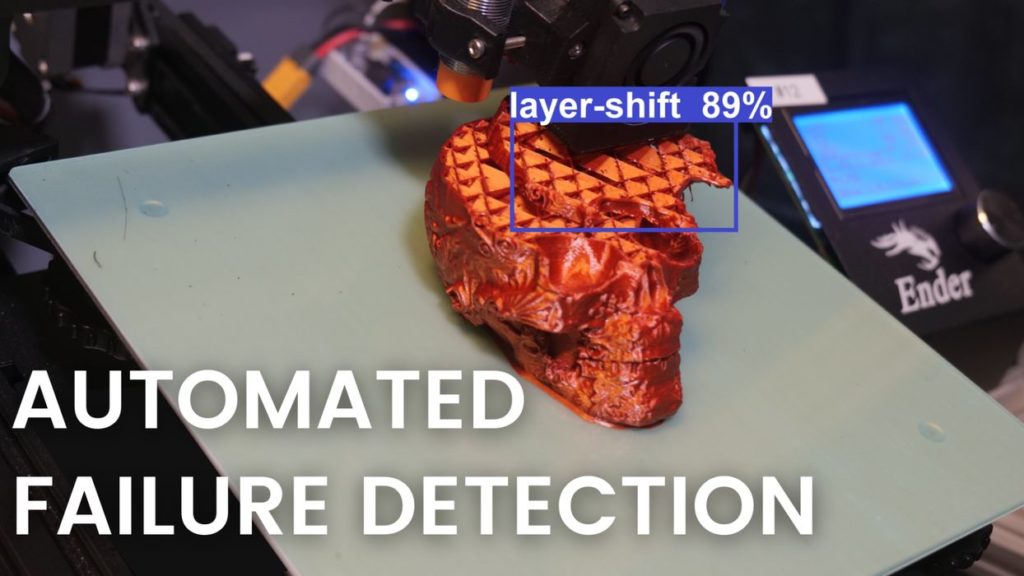
One of the more interesting features the company is developing is an AI-based failure detection system. They’ve captured over 250,000 images of different failures from their in-house operations, and fed them into a machine learning system. Pekic said the system can detect 14 different failure modes, such as print detaches, spaghetti, etc. Even better, it can also detect nozzle clogs, under extruding and more. The system is able to confirm that a part has been successfully removed from the bed.
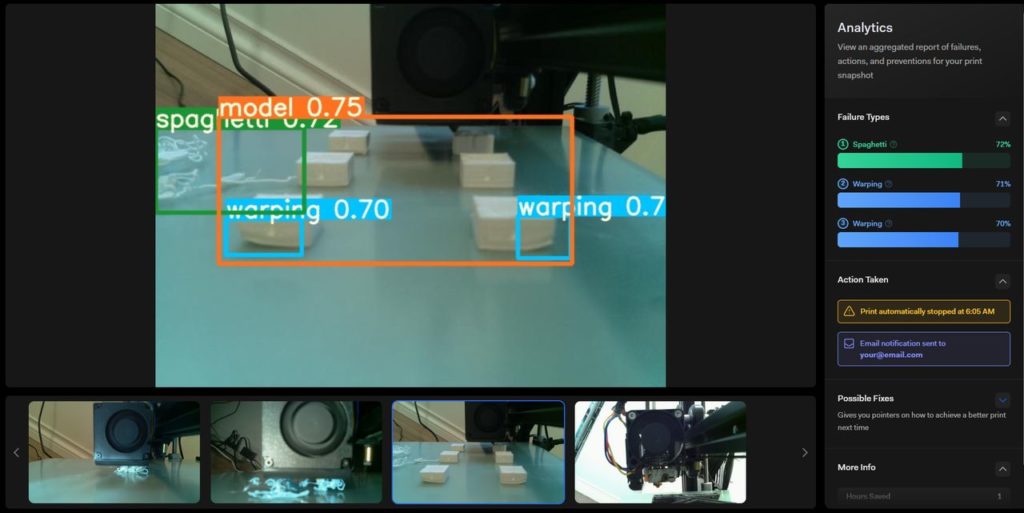
This is quite interesting, because their data has been collected from a wide variety of 3D printers of different models they’ve been using for their Quinly development. It may be they have the best image database of 3D printing failures on the planet.
This puts 3DQue in a very good position to market their manufacturing automation system to clients in all sizes of operations.
Via 3DQue