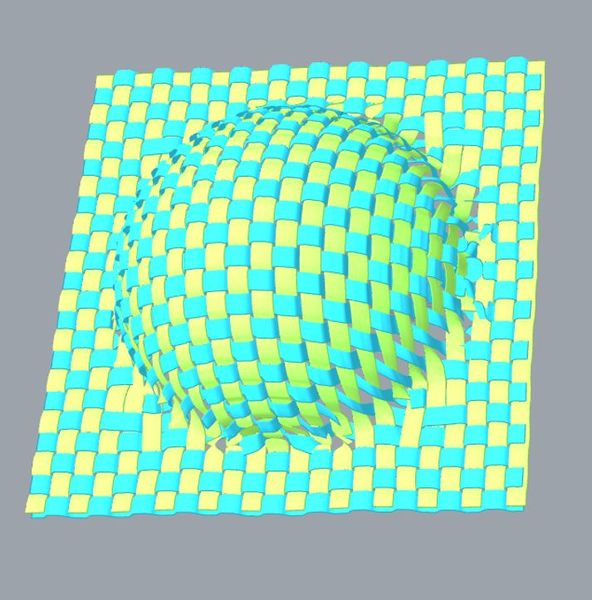
I’m looking at an unusual form of 3D printing involving textiles.
The company behind this tech is France-based 3DiTEX, a startup that hopes to open up new markets based on 3D textiles. I noticed they are one of the very few 3D printing companies exhibiting at CES 2021 next week.
This perhaps requires a bit of explanation, as textiles are, by definition, 2D objects. Today’s fashions are really assemblies of 2D sheets that have been cut, folded and joined. They are not really composed of “3D” fabrics; the 3D aspects only manifest due to the assembly.
But what if you could produce a true, 3D textile? That’s what 3DiTEX seems to be working towards.
This is how 3DiTEX describes their goal:
“3DiTex intends to revolutionize the way of producing technical textiles using its innovative 3D weaving technology. The ‘3D Weave’ technology includes algorithms and additive production machines allowing the production of textiles of complex shapes without tools or preforming operation.”
So it’s not quite like conventional 3D printing, where solid 3D objects are produced using various processes. Instead, 3DiTEX uses machinery that will “weave” textiles in a non-flat arrangement.
Take a closer look at the top image. There you’ll see the “2D” surface of the textile actual curves across 3D space. It’s not folded or molded into that shape; it’s literally constructed that way.
A textile woven in this manner would retain its 3D shape in a way that is unseen in conventional fabrics.
How does 3DiTEX manage to do this? So far they’ve published this chart that explains their process, at a high level:
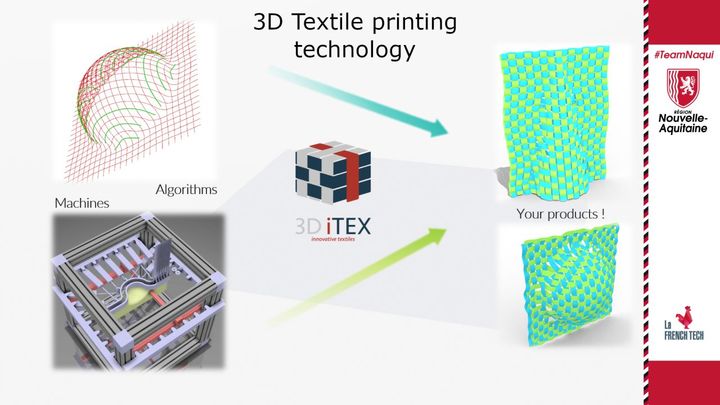
So high-level it is that it’s not entirely clear how they do this. While the relatively simple shape above is something one can imagine being produced, a 3D printing system that can make arbitrary shapes using this technique would be extremely complex.
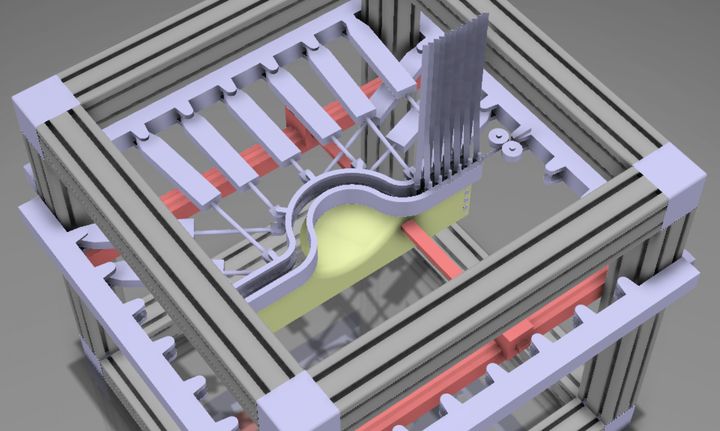
Some geometries would certainly be impossible to produce, but others could be — and they might be extraordinarily complex to plan in software. The mechanics of weaving would be interesting, but more than likely the software is the key to 3DiTEX’s system.
What do we know about their software? Not much. In fact, a recent post from 3DiTEX says:
“Dear network, digital CES is next week, the whole team is getting prepared for this event. We will disclose what our algorithms can do to transform a 3D surface into a 3D woven textile with iso-spaced trajectories (no gaps or overlaps except for the singularities). You will have to wait a little bit longer to see the machines under development.”
I’ll be watching closely to see more details on this from the company when they become available.
There’s more. You can’t just think about this technology in terms of fashion. There are many industrial products that can be made from fabric, and perhaps even more if one could make 3D textiles. 3DiTEX says:
“You could use our technology for 2D (kiting) or 3D net shape woven textile production. Think of it as a textile 3D printing machine for prototyping or full scale production depending on the machine and options! We can transform paper, metal, plastic and almost any kind of technical fibers or ‘tapes’.”
This could be another area enabled by a new technology, where the incumbents don’t yet understand how it could be used. I’ve seen this effect previously in several areas, such as ceramic 3D printing, construction 3D printing and even silicone 3D printing. If that’s the case, then 3DiTEX might have to withstand several years of educating clients and prospects on new approaches to product design.
Via 3DiTEX