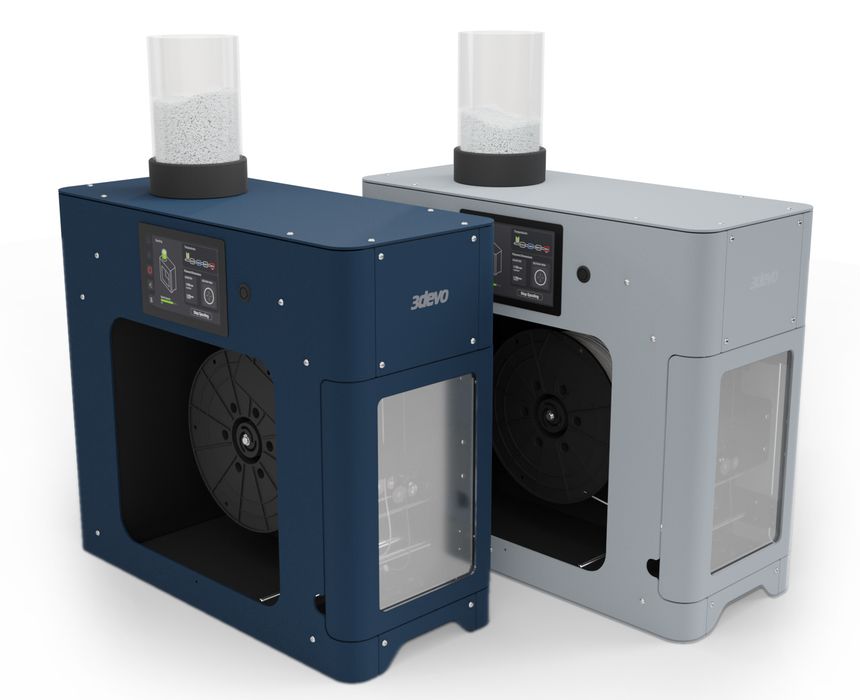
3devo introduced two new advanced filament production machines, the TWO Fusion and TWO High Flow.
The company is one of the very few that manufacture table-top filament extruders, with which one could produce their own spools of material. While there has been many attempts at making this type of equipment, it is extremely difficult to achieve. 3devo has figured out not only how to do this technically, but also found the right market for selling the equipment.
Unfortunately for desktop 3D printer operators, this equipment is not a way to “make cheap filament on your own”. The equipment is instead targeted at institutions and research operations where experimental filaments are required. The filament makers allow these groups to mix and match their own materials and produce high quality filament.
Two models of “TWO” are produced:
- Filament Maker TWO Fusion: intended for operators that require mixing of materials to create composite filaments
- Filament Maker TWO High Flow: Intended for operators with pre-mixed materials that just require the high quality filament
The main difference seems to be the type of screw used in each system. The Fusion has a special bit that seems to grind up input pellets, while the High Flow’s bit is designed for speed.
What’s different with the TWO series? Quite a bit, it turns out.
First, the TWO systems have much increased data and sensors. This is a critical element in producing quality filament: timing, speeds, temperatures must be absolutely perfect to create consistently high quality filament. The idea of “just extruding some filament” simply does not work, and 3devo has taken the precision of the practice to a new level with the TWO series.
3devo said the TWO series provides five times better resolution, meaning the output filament will have very good quality.
The systems are designed for easy use their a larger touchscreen that provides access to the myriad of control features on the system. It’s also designed to be easy to maintain, with modular components.
Another interesting feature is a longer cooling path. Normally freshly extruded material must be cooled in order to solidify and maintain its diameter. This cooling must be done in a very precise manner and a longer path should allow for better quality.
At the same time, the company announced something called “DevoJourney”, which is a customized education and service program for TWO clients. The idea is that creating quality filament requires some experience, and many 3devo clients won’t have that experience. Through the new program they’ll have access to 3devo experts that can help them on their filament journey.
Via 3devo