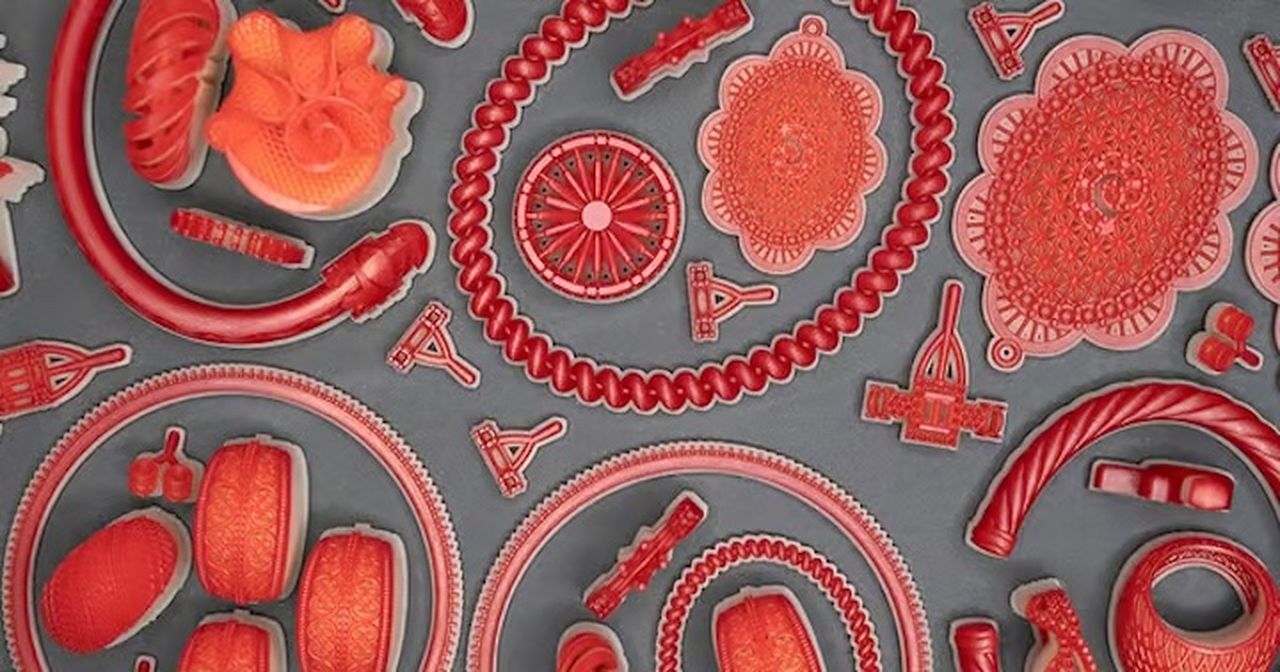
3D Systems announced a very interesting jewelry 3D printer, the ProJet MJP 2500W.
The jewelry market is quite large, US$25B in size, according to 3D Systems. The company hopes to capture even more of that business with the new ProJet MJP 2500W.
The ProJet MJP 2500W is a wax 3D printer, as are most jewelry devices. The idea is that a replica of a jewelry item can be produced in wax, then used in the lost wax process to make a metal equivalent. The wax print is placed in a plaster-like material, and then burned out through heat application. Then, liquid metal is poured into the void to form the item.
That’s actually not the end of the process: the resulting metal part must be first cut off from the sprue of metal formed during casting, and then extensively polished. This produces the shiny finish one would expect on any piece of jewelry.
3D Systems has enhanced their existing ProJet technology in the new ProJet MJP 2500W in a couple of ways that should be very attractive to jewelry designers.
First, the device provides 25% more throughput than prior devices. This means the machine can produce more jewelry per hour, making it more financially efficient. It’s like getting 1.25 machines for the price of one. 3D Systems said the machine can produce an object in only four hours when in “single lane” mode.
The second major enhancement is more interesting. The ProJet MJP 2500W includes a new feature they call “ZHD print mode”. This mode doubles the vertical resolution, likely by halving the layer height.
In ZHD print mode, the device has a resolution of 1200 x 1200 x 3200 dpi, which is extraordinary. Layer thickness is only 0.008mm!
Wax prints made in ZHD print mode would accordingly have smoother surfaces.
However, smoother surfaces imply less polishing is required. That further increases jewelry production throughput by lessening the amount of manual labor required after printing.
There’s another unique saving from this feature: because there’s less polishing, there is less waste of precious metals.
Polishing, at a micro scale, is literally carving off “hills” to bring the entire surface down to the level of the “valleys”. The material cut off becomes dust.
While polishing polymer prints simply produces waste, in the case of jewelry the dust is quite valuable. I’m sure that most jewelers would have a mechanism for recovering as much of that gold dust as possible, but producing less from polishing would greatly simplify the issue and perhaps even provide measurable materials savings.
Finally, 3D Systems suggests, and I think they’re correct here, that the smoother surfaces enables jewelry designers to attempt more complex designs that normally would be impossible to polish. Previously the unpolishable areas would be unacceptably rough, but not so with the new ProJet 2500W Plus.
3D Systems said the new 3D printer is available now, as well as VisiJet wax materials for it.
Via 3D Systems