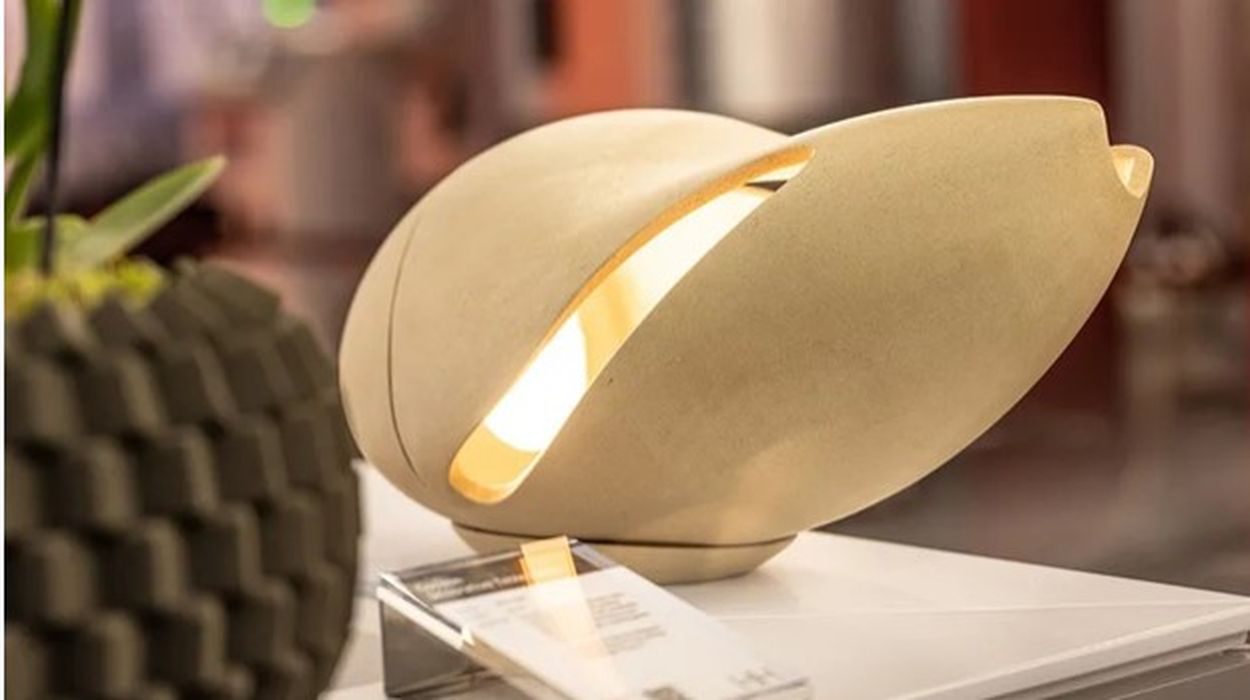
Forust Partners with design firm HagenHinderdael to demonstrate the beauty and sustainability of 3D printing with organics.
3D printing is transforming the mass production process, giving manufacturers in a wide range of industries the ability to create more intricate designs in a lower cost, on-demand format. Yet one challenge of the additive process is the scope of materials available. Plastics are the most common 3D printing material but metals, ABS, nylon, polycarbonate and polypropylene are also widely available.
While those materials are strong and versatile, they don’t necessarily fulfill demand for natural or sustainable products. However, a new class of organic materials is opening up possibilities for 3D printing. One such material, sawdust, is forming the basis for more eco-friendly 3D printing for sustainable products that helps put a common waste product to good use.
Founded in 2019, Forust, which was acquired by Desktop Metal in 2020, is at the forefront of 3D printing with sawdust. The company 3D prints products that are indistinguishable from conventional wood manufactured products, but are produced in a more affordable and environmentally responsible manner.
“The inspiration for Forust was to begin with sawdust and end with forests,” said Forust CEO Andrew Jeffery. “Our process is based on extensive research conducted over the past decade in the field of hardwood lumber, leading to complex and elegant finished structures. Through advanced CAD software, proprietary materials and Desktop Metal binder jetting mass production platforms, we can now manufacture beautiful, functional and innovative wood products for a variety of architectural, interior, and home goods applications from upcycled wood byproducts.”
Powered by Desktop Metal’s binder jetting 3D printing technology, Forust sources waste sawdust from woodworking facilities and mixes it with a bio-based binding agent derived from plant materials to create a composite material with structural integrity. The mixture is then extruded into a 3D printer which uses a nozzle to deposit the mixture in precise locations, following a digital 3D model. The material is then molded into the target form, layer by layer, until the final product is achieved. Once the object is printed, it is dried and cured to remove any excess moisture and strengthen the bond between the sawdust and binder. Finally, the object is sanded and finished to give it a smooth surface and the desired appearance.
The Shop System Forust Edition was the first commercially available 3D printing system to process up-cycled sawdust into functional, end-use wood parts using high-speed binder jetting technology. Some of the applications of the technology are luxury vehicles and high-end homes that possess a range of finishes and materials, including rare and exotic grain structures as well as wood fishes without a grain. One of the processes’ advantages is that the bio-epoxy resin used as a binder has a similar strength to wood with a 90 MPa.
For batch production, the Shop System features a compact, high-speed, single-pass print engine that’s suited for production of small- to-medium-sized wood components. For mass production with a large build volume (180 x 90 x 30 cm) a large format, single-pass printer called the RAM 336 is used, capable of high-throughput, wood part mass production.
One of the big benefits of 3D printing with sawdust is that it produces less waste compared to traditional 3D printing materials. Since the sawdust is a byproduct that would otherwise be discarded, it also has a lower carbon footprint than other materials or conventional wood manufacturing. Additionally, the end products are strong, durable and can have a unique and natural aesthetic that’s well-suited for products in which an artistic appeal is desired.
One of Forest’s earliest collaborations was with London-based design firm HagenHinderdael. Founded by architects Sofia Hagen and Lisa Hinderdael, the firm pairs product design with art, and from its inception during the pandemic has been focused on materials research. With factories closed in 2020, they turned to the possibilities of 3D printing for production.
Hagen said that they had learned about Forust 3D printing with sawdust and were immediately interested in the fact that the process doesn’t use any glues or chemicals. Instead, lignin, which is extracted from wood is used as a binding agent in the process.
“We just fell in love with the material and the fact that it’s 100% organic and biodegradable,” said Hagen.”
Read the rest of this story at ENGINEERING.com