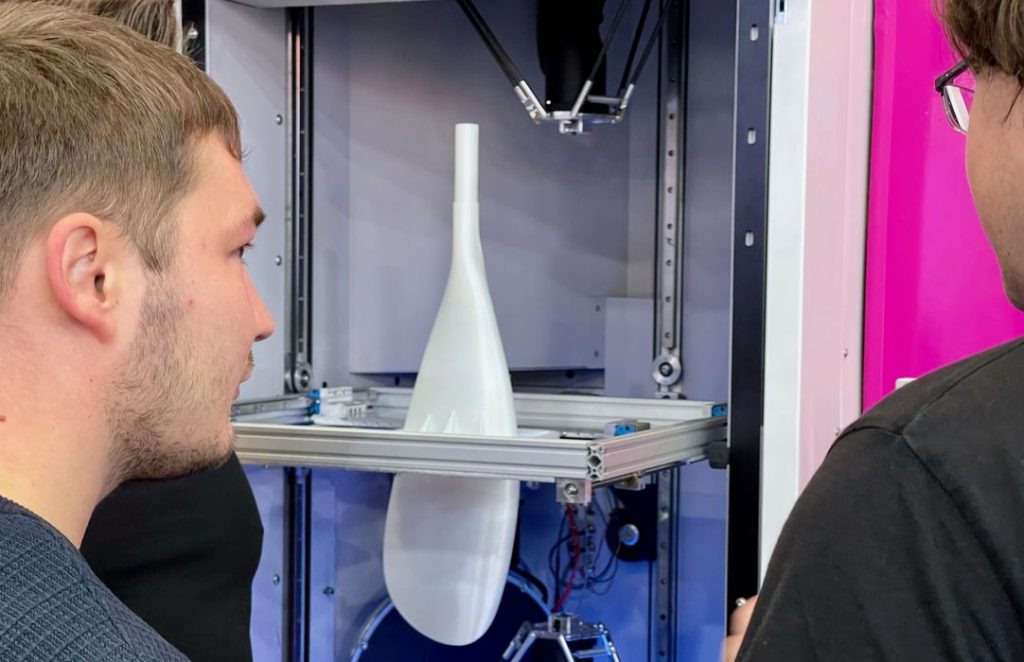
Duplex 3D has produced what could be one of the strangest — and fastest — FFF 3D printers on the market.
The German company, which launched only in 2016, produces two industrial 3D printers, the F2 and S2. The F2, an FFF device, is the subject of this post.
The Duplex 3D F2 uses a delta motion system, which is common among FFF devices. Delta motion systems allow for very tall prints, and also rapid print speeds because of the lightweight print head and easy ability for the motion system to respond to directional changes.
The odd thing about the F2 is that it uses TWO delta motion systems. And one of them is upside down. Don’t believe me? Look at this image:
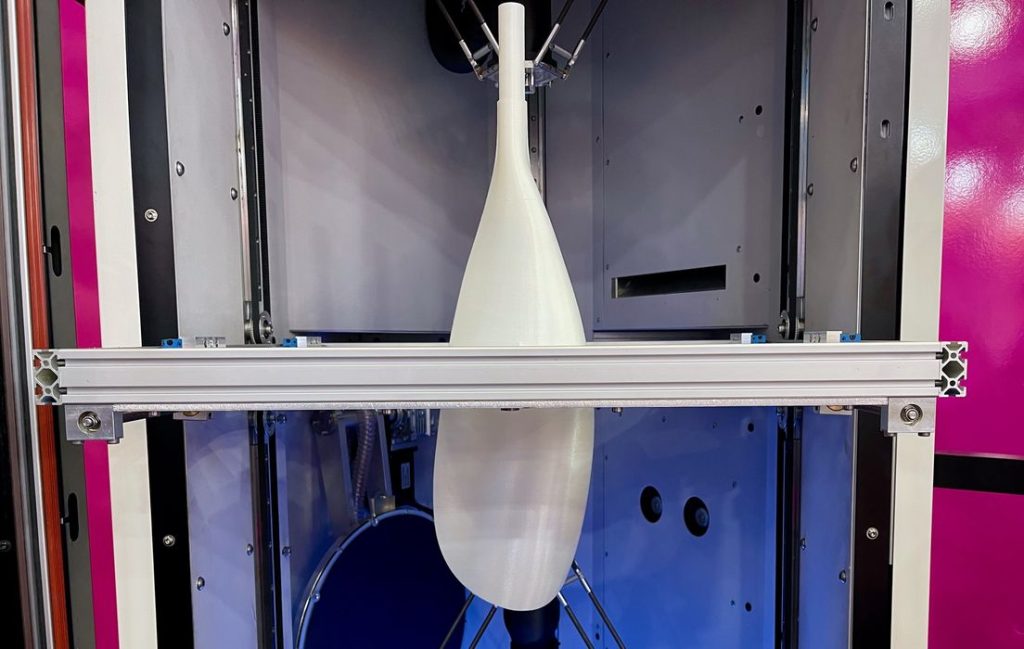
Upside down 3D printing has been done previously. I first saw this effect in 2014 when Mass Portal had one of their Pharaoh delta machines running sideways. Later, we saw some folks wall-mounting their Creality 3DPrintMills, also printing sideways.
Upside down is also possible, as gravity doesn’t have much effect when support structures are used. Polymers still adhere to the print surface.
Here Duplex 3D has mounted the delta motion system opposite to each other, so that they can operate in parallel. One system prints the top of the model, while the other works on the bottom.
There are a couple of benefits to this approach. First, your print is done in half the time because “two printers” are working on it. These two devices cannot interfere with each other, so they proceed unchecked without the possibility of collisions as happens in some other dual extrusion configurations.
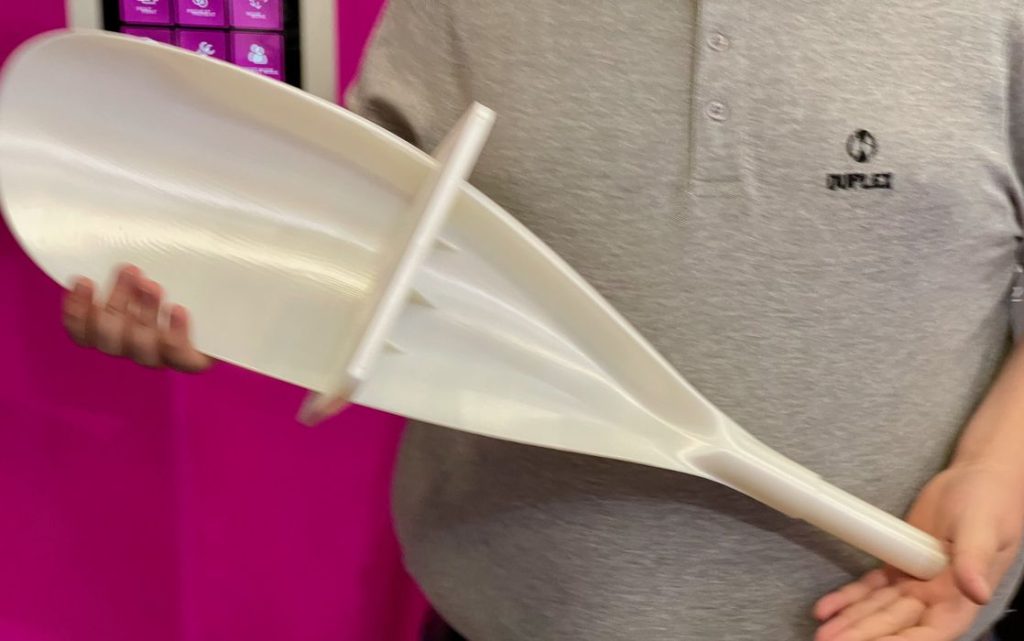
The second benefit is size: the prints can be literally twice the height of each print system. The F2 can produce objects 1m in length, with a diameter of 400mm.
Another benefit is with support structures. It’s possible to reduce the support required by optimally oriented the print: overhangs in one direction might not be in another. I’m not certain if Duplex 3D’s software automatically identifies this, but it probably should, as that could simplify post processing.
But wait: you’re probably wondering how this print sequence could begin? Isn’t there just air between the two print zones?
Yes, that’s true, and Duplex 3D uses a unique approach to get things started.
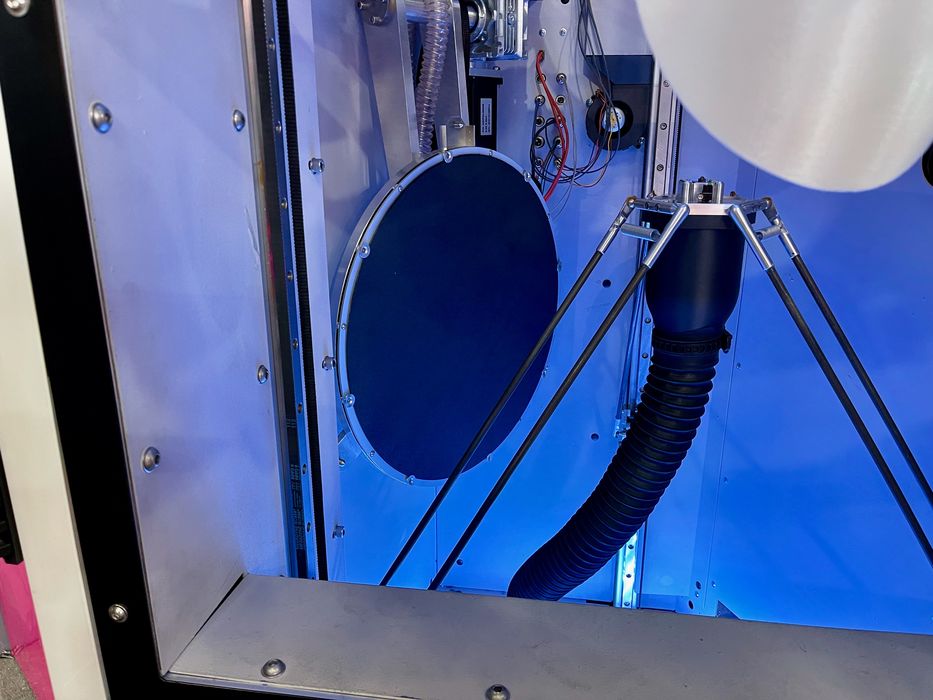
Inside the F2 there is a movable print plate. To begin a print, the plate swings into place, and the top printer produces a “frame” like the one seen here:
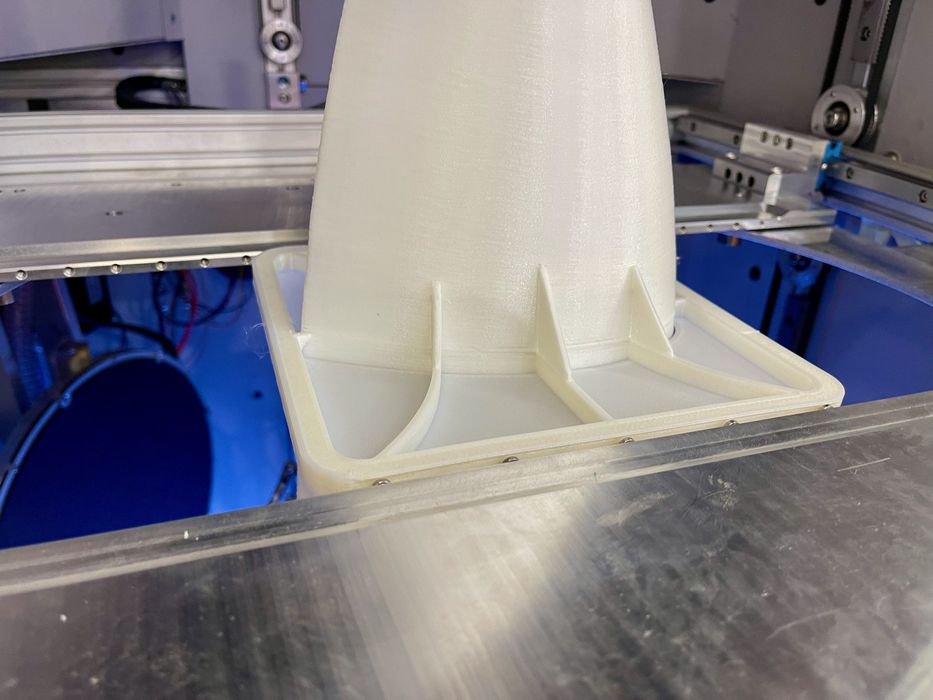
This frame becomes the build surface for both halves of the print. The lower printer works downward from the bottom of the frame, and top vice versa.
After the print completes you’ll have to remove the excess frame material, but that’s no different than removing support material.
The result is a rather large print, obtained in record time. Here we see a paddle printed in 1m length.
The F2 sports a heated plate that can hit 180C, and an actively heated chamber that can hit 80C. The hot end can reach 500C, and putting all this together means the F2 can make use of virtually any engineering 3D print material.
While the F2 has swappable nozzles, the default is a 0.8mm nozzle, quite a bit larger than the default 0.4mm nozzles found on most FFF 3D printers. This produces more coarse extrusions, but that’s ok for the large-sized prints coming out of this machine.
As you might imagine, the F2 comes with specialized software to generate the complex GCODE for operating this dual extrusion machine, along with the “AutoPlane” system that moves the temporary plate.
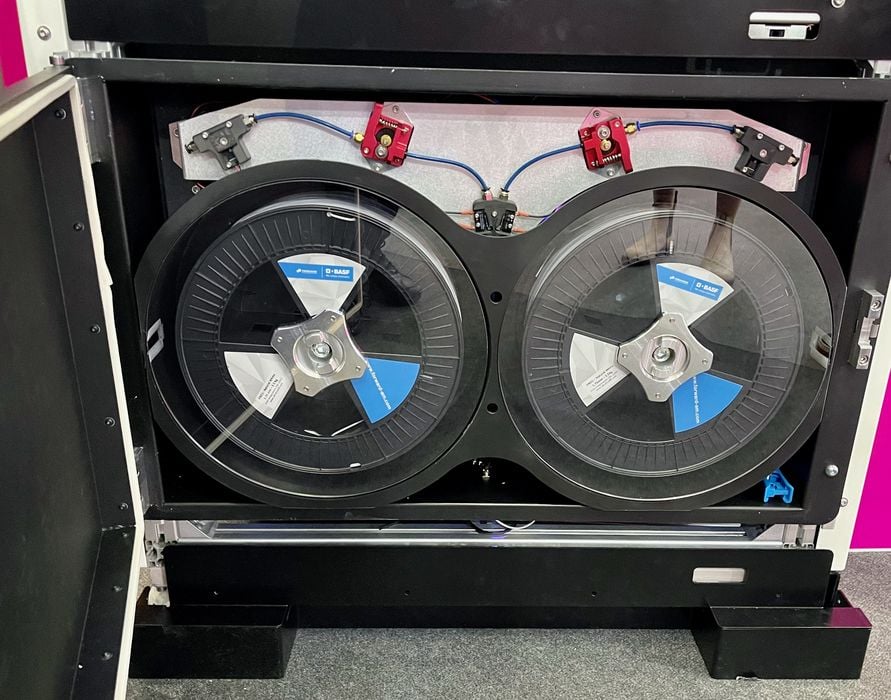
Many different materials are possible with the F2, but the 4.5kg spools reside in a special dry box in the bottom of the machine to maintain quality. The company is working with BASF to provide a wide variety of materials for the F2.
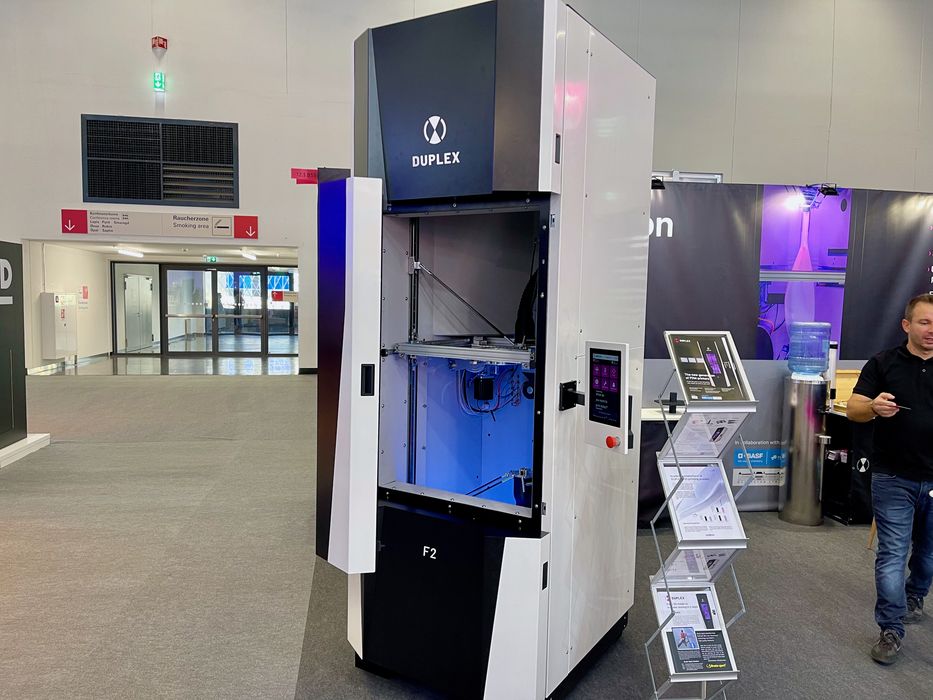
The machine is nearly ready for release, and the price is said to be near €85,000 (US$89,000). For that you’ll get one year of support as well.
Via Duplex 3D