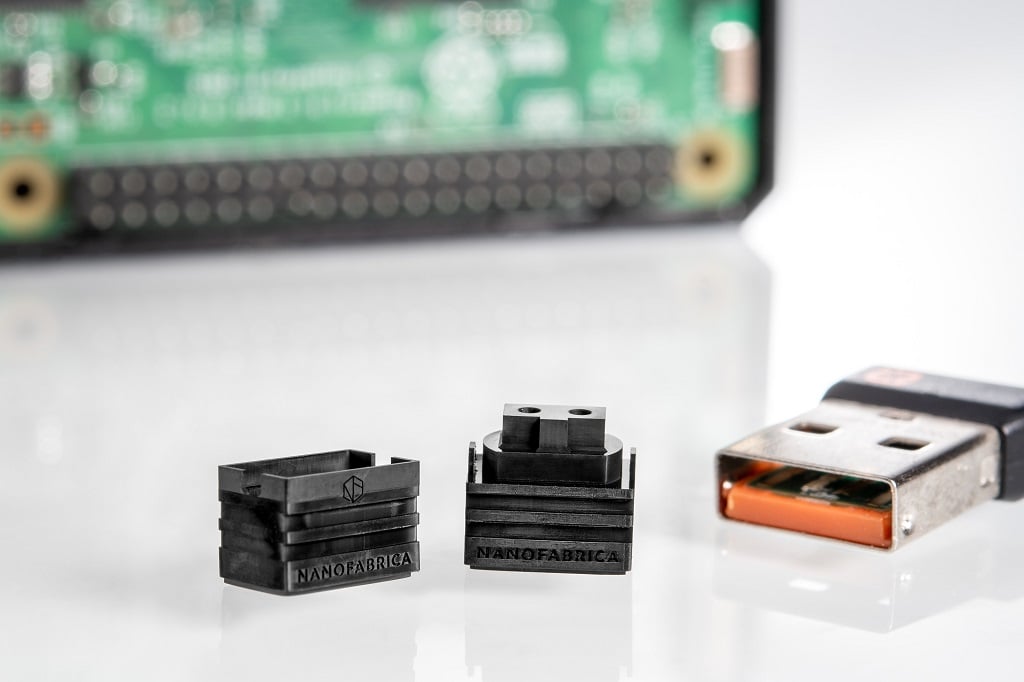
I spoke with Avi Cohen, EVP Sales at Nanofabrica, for a look into why micro-scale precision in 3D printing is a huge achievement.
Precision In 3D Printing
While thankfully we’re easing away from the phrase “3D printing” conjuring images of a Yoda head on a desktop FFF machine, still most immediate thoughts of the technology turn the mind to parts made on such a system. If not, thinking of “additive manufacturing” might lead one to consider advanced rocket engine parts, where newly possible geometric complexity consolidated an assembly of dozens of components to a single unibody part. If not that, maybe it’s 3D printed hearts or buildings. The applications are growing widely across the board, across technologies and materials, but in most cases you can really see them being built up.
Israel-based Nanofabrica is taking these big ideas and turning them to the small scale. So small, in fact, some of their capabilities are best displayed on highly detailed prints the size of a grain of rice.
Resolution is a key parameter in 3D printing. These stats are often given in millimeters to understand the fineness of detail possible. Nanofabrica, though, uses a different scale altogether, as their Tera 250 system offers some real precision engineering at “1 µm resolution over 50X50X100 mm.” It can create structures as small as 0.001mm.
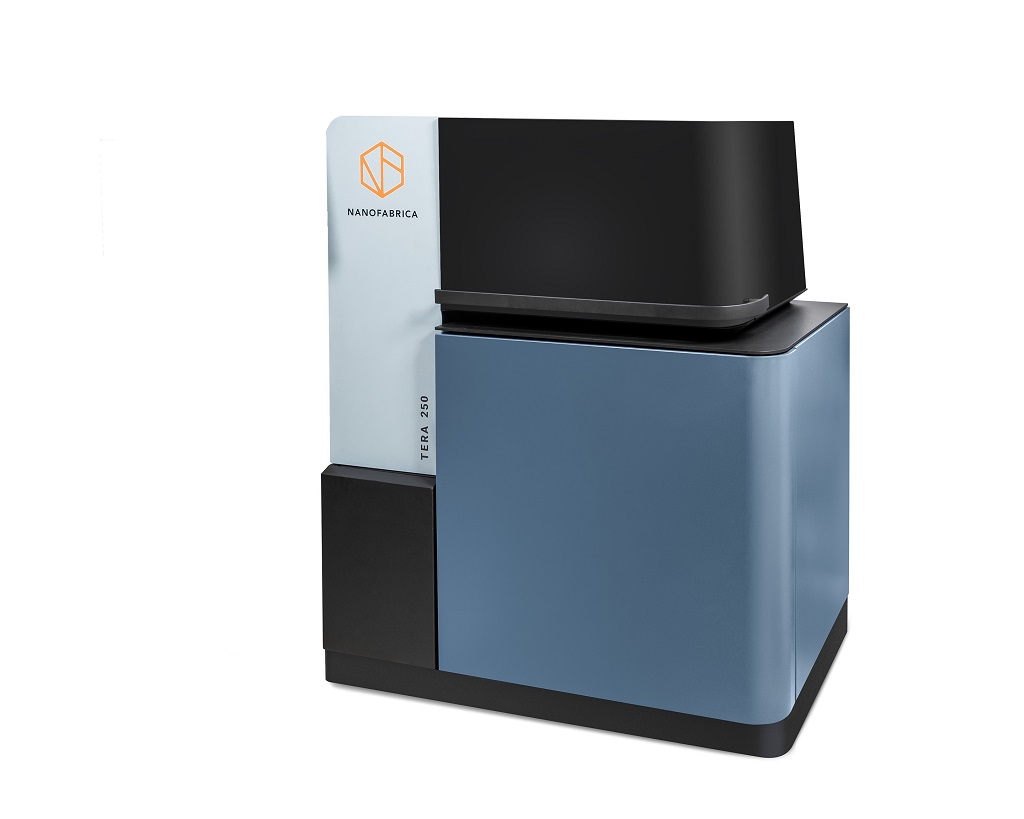
So fine is the detail possible that we’ve considered their technology’s achievements as another way of considering 3D printing resolution altogether. Indeed, as Nanofabrica CEO Jon Donner explained:
“We came up with the Tera 250 as this conveys the most unique aspect of our technology, namely the fact that we manufacture the only commercially available AM platform that can produce micro products with micron resolutions. We have 250 tera voxels in the build volume of the printer, hence the Tera 250!”
Inside Nanofabrica
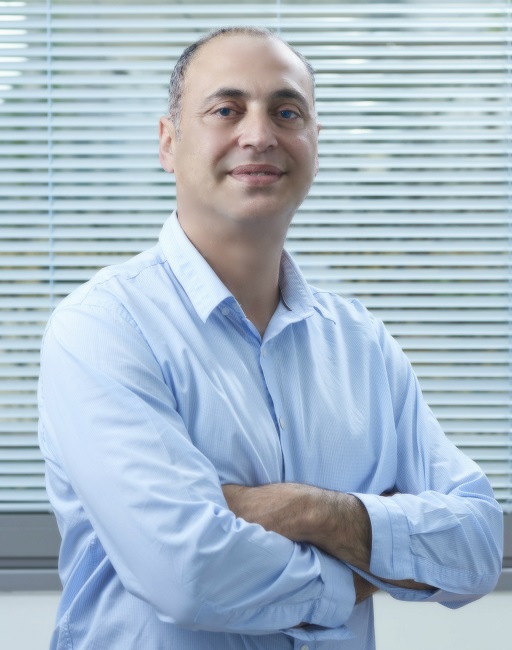
For more detail on the detail here, I turned to a conversation with Avi Cohen. Cohen has been in the 3D printing industry for over two decades now, having worked at Stratasys for 16 years and XJet for another half-decade, before joining up with Nanofabrica last summer.
“I’ve been working in the 3D printing world since late 1998,” Cohen said, reminiscing, “3D printing was very early then. People didn’t know what a ‘3D printer’ was, they’d say, ‘A printer I know, but what’s this 3D?’ In the beginning, it was very normal to print something in the palm of your hand. Every year then, people would want something bigger and bigger, they would want the bumper of a car. But no one stopped and said, ‘Okay, we grow big parts, but what about smaller and smaller?’ or, ‘How small can you get?’
The reason behind joining Nanofabrica is to learn and join a new, innovative technology as well as going into this virgin land of microparts and still being in the AM industry which I like so much.”
So, he noted, what Nanofabrica is doing now is offering “the ability to print tiny tools we haven’t shown before.”
Nanofabrica has been around since 2016, making it “relatively young,” Cohen acknowledged. The idea sprang from the CEO, Donner, who has a PhD in optics. Cohen explained:
“The idea was to develop a micro-DLP process to set up an adaptive optic system, to zoom and fix to a micron size. All this is done on a granite table, it’s very solid, in order to get the super high accuracy of 300 nano. The movement of this system is accurate to 300nm…The combination of all this gives us a new technology, an innovative technology to bring to these microparts. Nobody has a machine built where the chassis is a granite table with micro optics, that was never seen before. We call it adaptive smart optics.”
From 2016, the team has now grown to about 15 employees working to create these finely detailed tiny prints.
Nanofabrica 3D Printing Technology
One of the company’s parts to really grab significant attention is one that’s grabbed popular culture for years now: the Harry Potter-famed Hogwarts castle. While in the books, the castle was a massive structure with dozens of staircases housing hundreds of students, Nanofabrica’s version is a bit scaled down. It measures about 2.5mm across: “the size of a grain of rice.”
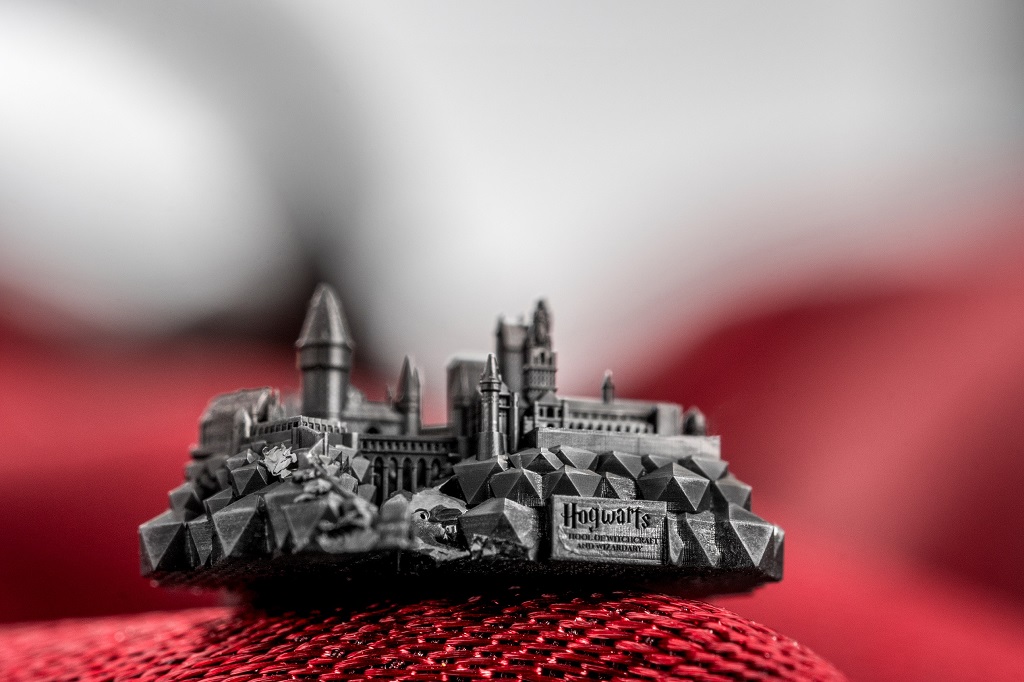
It’s a very cool model, to be sure, and absolutely demonstrates the exquisite detail possible from the Tera 250. But the “your name on a grain of rice” fad of the ‘90s was also very cool; what takes us away from nifty demonstration to the functional?
Indeed, as Cohen acknowledged, “The ability to print small parts brings the big question: who needs them and for what?”
In his experience, there are essentially two major customers for such tiny, detailed 3D printed parts. About half are looking to 3D print a small part — think electronic connectors, optics, or mechanical parts — ready for use. The other half are looking to 3D print mold inserts.
In terms of parts, an example that sprang forth to best understand the application possibilities for bitty 3D prints was a pretty-forgotten, previously high-profile product. Remember Google Glass? In looking up the timeline to write this paragraph, it honestly surprised me to realize the project isn’t dead. Wikipedia sums it up tidily:
“Google started selling a prototype of Google Glass to qualified ‘Glass Explorers’ in the US on April 15, 2013, for a limited period for $1,500, before it became available to the public on May 15, 2014. It had an integral 5 megapixel still/720p video camera. The headset received a great deal of criticism amid concerns that its use could violate existing privacy laws.
On January 15, 2015, Google announced that it would stop producing the Google Glass prototype, to be continued in 2017 tentatively. In July 2017, Google announced the Google Glass Enterprise Edition. In May 2019, Google announced the Google Glass Enterprise Edition 2.”
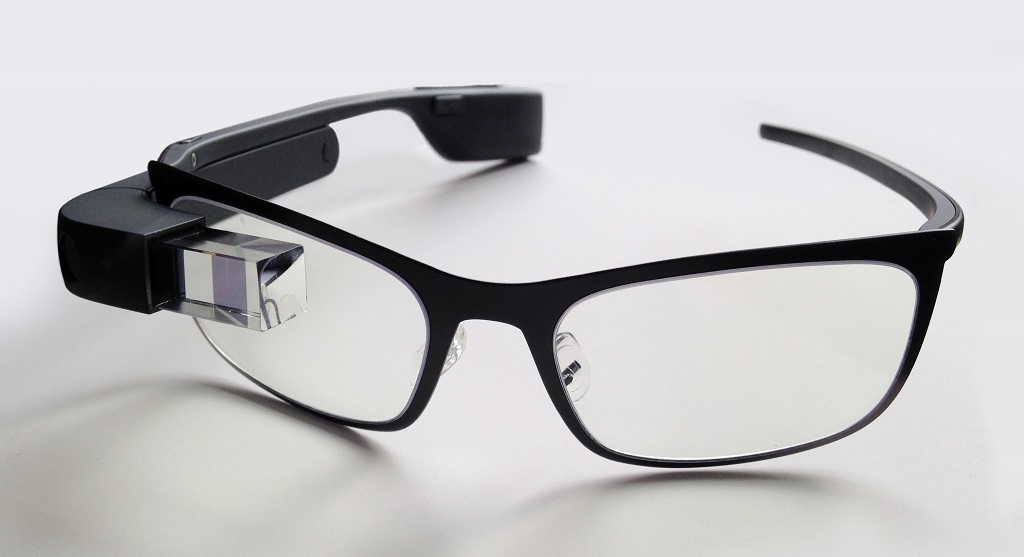
So in bonus news, Google Glass is still a thing. But: could the initially planned commercial project have achieved some better measure of success if the actual glasses weren’t so bulky and not-wearer-friendly?
“If you remember, some years ago Google came up with Google Glass; it was big and bulky here,” Cohen said, indicating the sides of the frames, “and didn’t get much success, I think. If they were looking to print the assemblies with microparts, maybe the end would be different.”
Indeed, Nanofabrica is becoming increasingly well-versed in 3D printing microassemblies. A micro insulin pump requires “very small assemblies inside it,” and the Tera 250 was able to deliver on this important functional demand. Micro impellers allow the pump to function. A micro filter for the medical market was made with 580 individual 50-micron holes in it.
“The parts we print can vary between small mechanical parts, lens holders that need accuracy, even automotive, aerospace, or medical,” Cohen added.
On the injection molding side, micro capabilities allow for a widening array of possibilities in a typically tooling-intensive discipline. We’ve had a look here into some of the possibilities with 3D printed micro molds using Nanofabrica’s technology.
And the timeline?
“We are already delivering the first machines to a few customers,” Cohen said.
The first three shipments have already taken place — or are about to, given Israel’s recent entry into another pandemic-necessitated lockdown — and the Tera 250 is officially out in the world.
Nanofabrica runs on a machine-selling model, enabling customers to install their own systems and 3D print their own projects.
This company seems like another poised to make big headlines for its impressively tiny achievements in 3D printing.
Via Nanofabrica