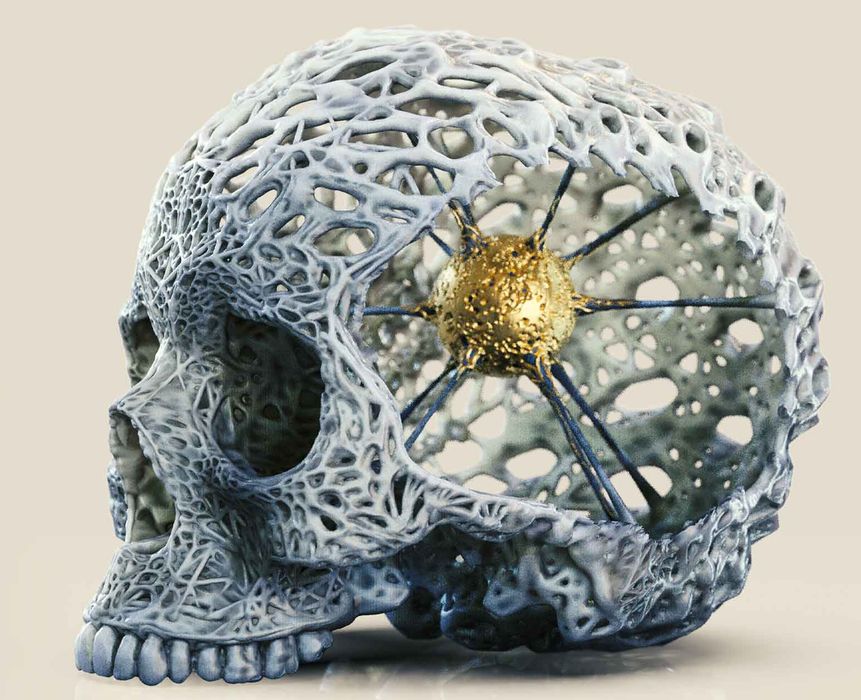
Formlabs just published a very interesting piece on how one of their clients leveraged 3D printing to produce movie props that would otherwise be impossible.
The props were produced by South Africa-based Dreamsmith, who make the most astonishing pieces, both props, animatronics and prosthetic makeup for film productions. The company was founded in 2013 by Jaco Synman after receiving awards for working on Mad Max: Fury Road, and now has produced pieces for over 60 productions, including District 9.
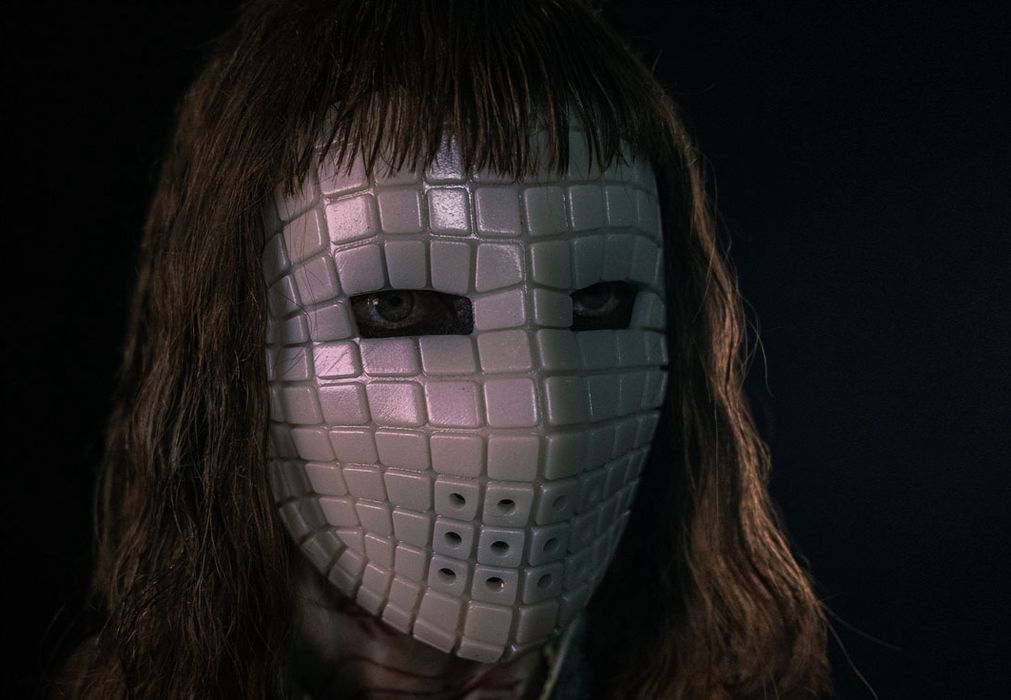
The company’s workflow involves use of CAD and sculpting tools, as well as 3D scanning and 3D printing. For 3D printing, they use a mix of FFF and SLA technology from Formlabs.
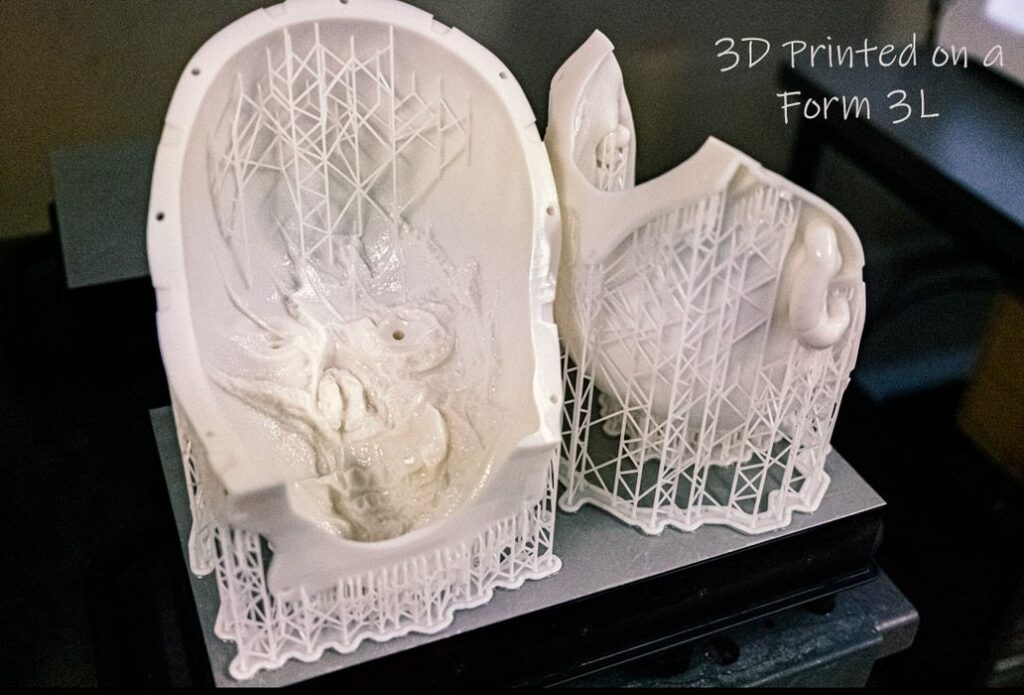
One of their more recent projects is to provide some of the special props and make-up effects for HBO’s Raised By Wolves series. While one of my favorite shows, it was unfortunately cancelled by the HBO Gods earlier this year. Nevertheless, if you’ve seen the show, you know that many of the effects used were startling and quite incredible to imagine producing.
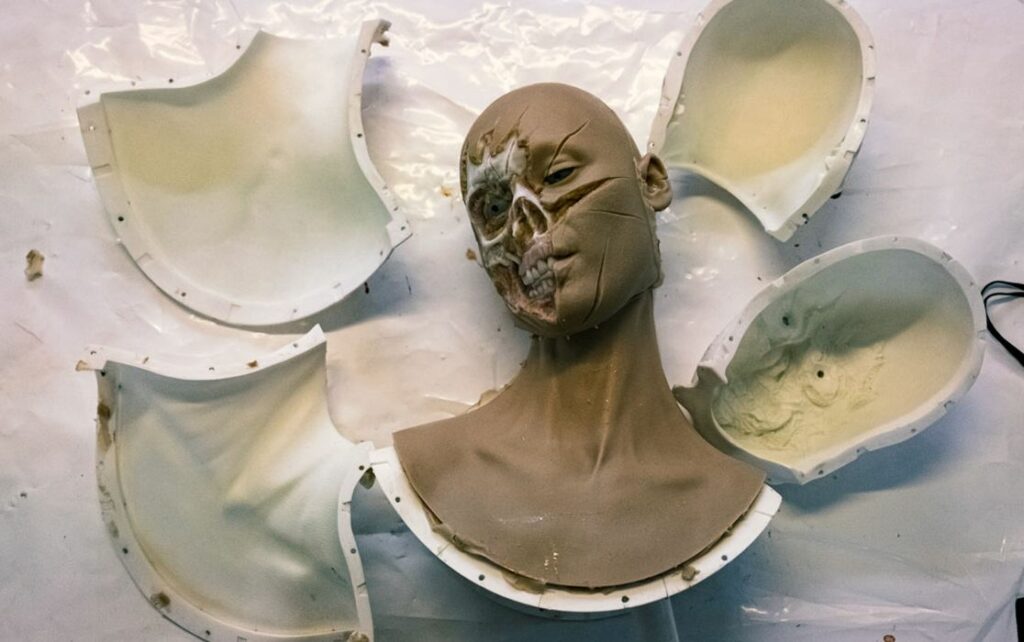
Dreamsmith chose to use a small fleet of Formlabs Form 3L 3D printers for this job, as they have a more than sufficient large build volume. Dreamsmith explains:
“The Form 3L ticked all the boxes. It has a massive 33.5 x 20.0 x 30 cm build volume with a resolution of 25 microns, all enabled by PreForm software that makes the package extremely reliable and easy to use. All this coupled with the impressive variety of resins makes the Form 3L an incredibly powerful tool, one tool that has completely revolutionized our workflow in two short years.”
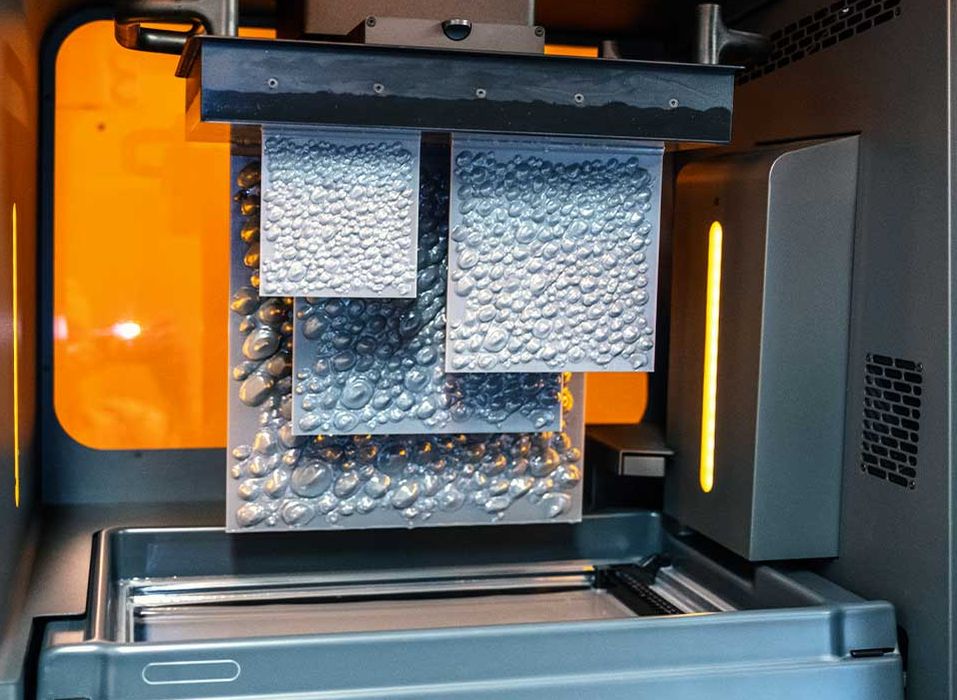
The news piece walks through five different applications by Dreamsmith on Raised By Wolves, including challenging projects like making a hyperrealistic silicone replica of an actor’s mangled face, producing a highly complex silicone custom-fit mask, and rapidly making a life-size realistic body double 3D print of an actor for a scene that would be impossible to film with the live actor.
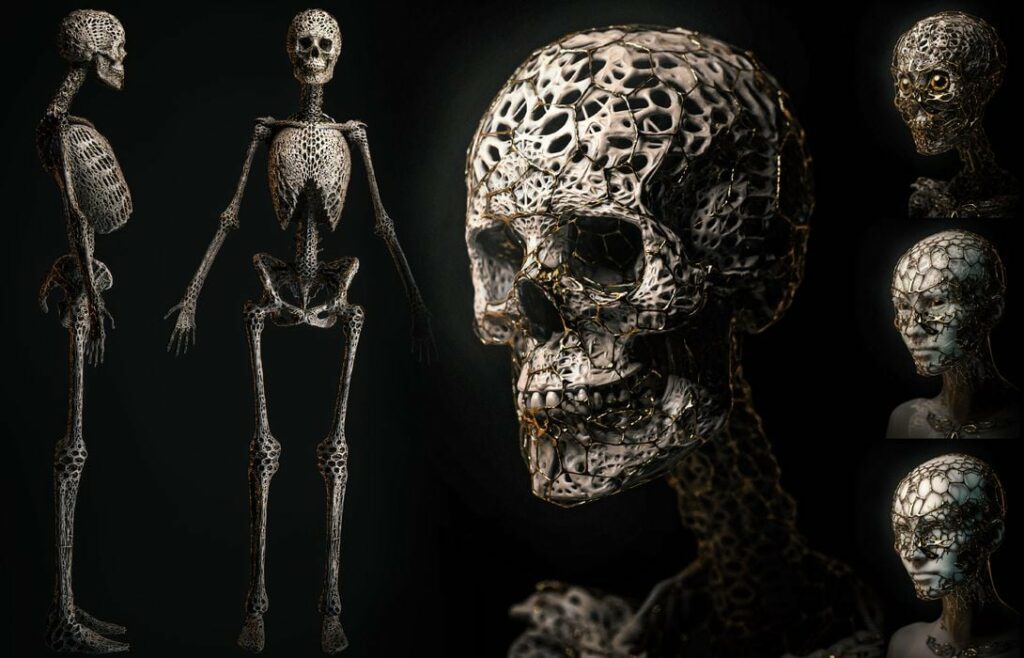
In addition, they undertook a project to produce “impossible” props. These were large sculptures that could literally not be produced in any way other than 3D printing due to their geometric complexity.
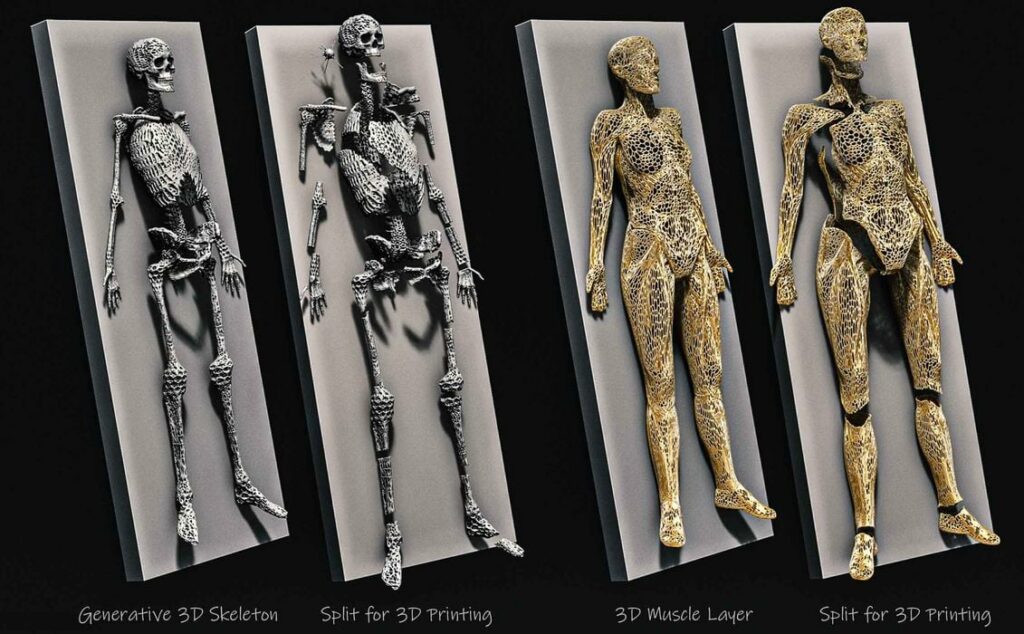
Specifically, this model was of an organically shaped full size biomechanical skeleton. Dreamsmith explains:
“The design above is of a life-size biomechanical skeleton. An intricately detailed prop with a geometric flow that would have been agonizingly difficult to sculpt out of clay and basically impossible to mold with traditional techniques.
The Grandmother Skeleton is a perfect example of a design created purely because we were able to 3D print it. Impossible shapes and interlocking gears have been printed for a while now, but what we needed was the ability to be precise at a useful scale. We needed a life-sized skeleton! The build volume of the Form 3L allowed us to print this entire prop in practical chunks at high resolution.”
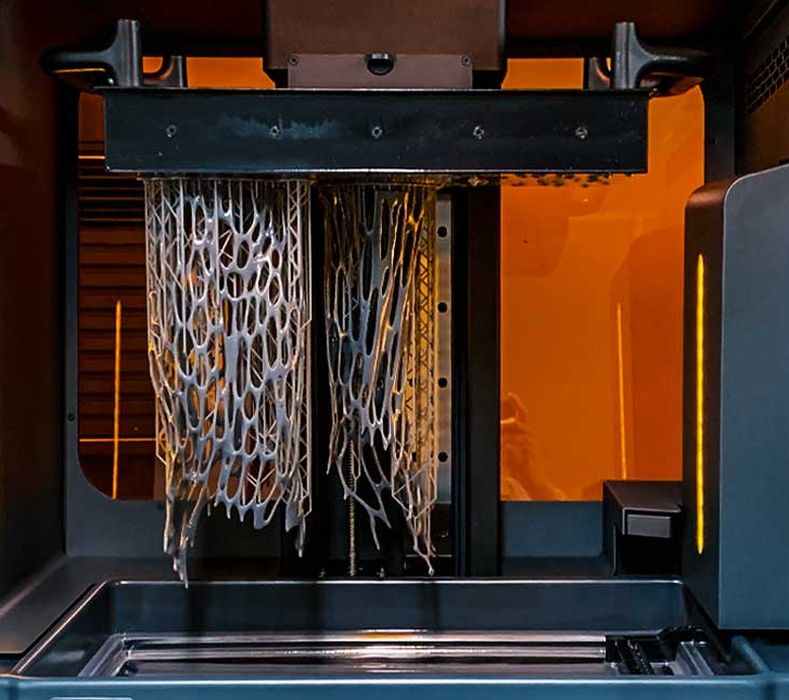
I resonate with this application because it is reminiscent of similar highly complex geometries used in manufacturing: they also cannot be produced in traditional ways, yet provide immense new value. Here the value is visual, rather than measured in weight savings.
It’s also a very good demonstration that the build volume of a 3D printer doesn’t necessarily dictate the size of objects that can be produced. Parts can almost always be broken down into smaller pieces and then assembled later.
What’s even more impressive is that for Dreamsmith, this was the first project they undertook that had a majority of 3D printing activity. This new workflow was then put to the test by movie deadlines, and Dreamsmith was able to get to the finish line successfully.
Formlabs has published many details of the workflow and process Dreamsmith used to produce these incredible props, and one can learn quite a bit by reading through them. [Note: Some of the images of the props are a bit gruesome, so please read accordingly.]
Via Formlabs and Dreamsmith