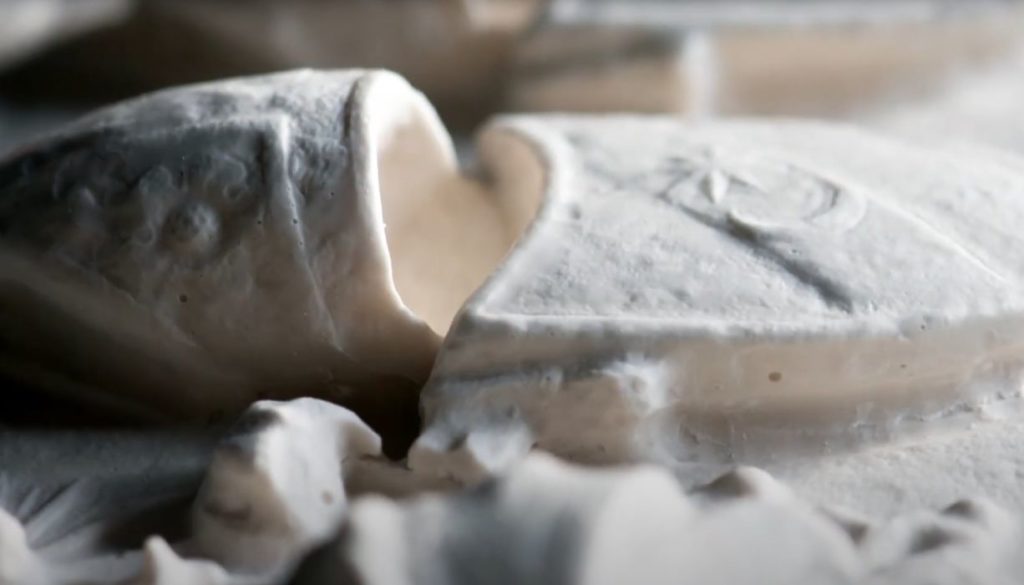
Researchers have developed a process for 3D printing tactile replicas of UNESCO World Heritage Sites and associated objects.
The goal here is to produce artifacts in a way that can engage visually impaired individuals through a tactile approach. Normally the items are far too large to touch as they are usually visually observed. Also, some artifacts are too fragile to permit touching, lest the objects be gradually damaged.
The solution is to reproduce them at a scale that allows touching. This must be sufficiently small to allow the “toucher” to gain a good understanding of the object’s entire geometry.
The project was undertaken by researchers from the Centre for Fine Print Research at UWE in Bristol, and funded by the EU Commission.
They explain the goals of the project:
“The models replicate the texture, design and structure of the historical sites and their artefacts which users can engage with through touch and feel. The models also contain a number of built in electronic near field connectivity (NFC) sensors which are triggered by a small ring-like device worn by users as they run their hands over various parts of the model. Once triggered, the ring device vibrates and activates an audio guide connected to an app on the users’ smart phone or tablet, creating a multi-sensory experience.”
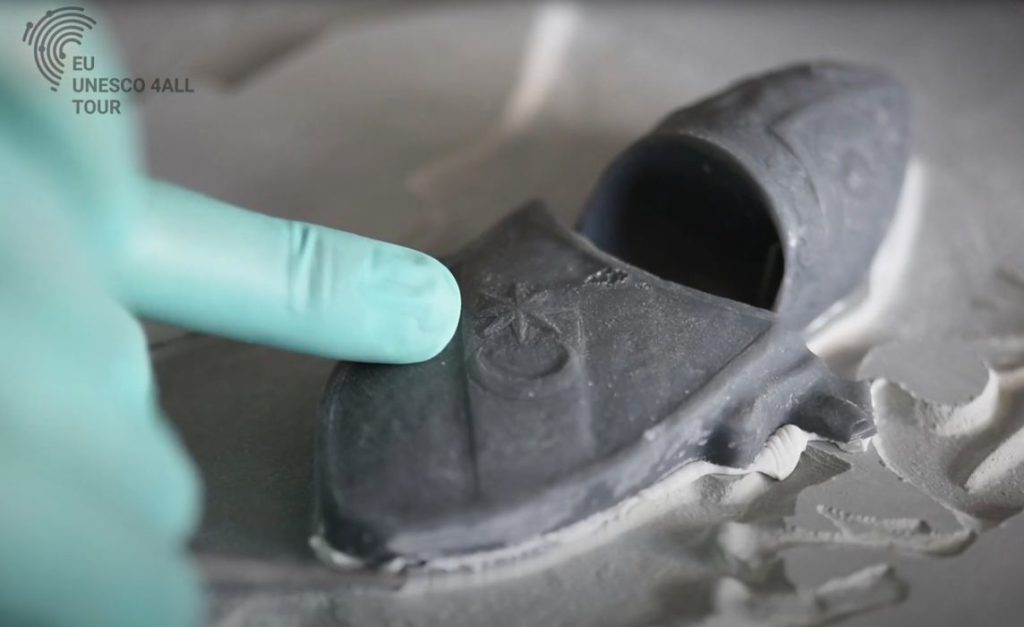
To build the tactile models, 3D scans were used to produce printable 3D models. These were produced using a resin 3D printer, and then mounted on a custom CNC-cut board with outlined mounts for each item. That board then served as a mold for casting a negative silicone mold, which in turn was used for casting in a plaster-like material.
You can see the entire production process in this short video:
There were four sites reproduced in this way, including Basiscica Aquileia in Italy, Alhambra Palace in Spain, Sibenik Cathedral in Croatia and Rila Monastery in Bulgaria.
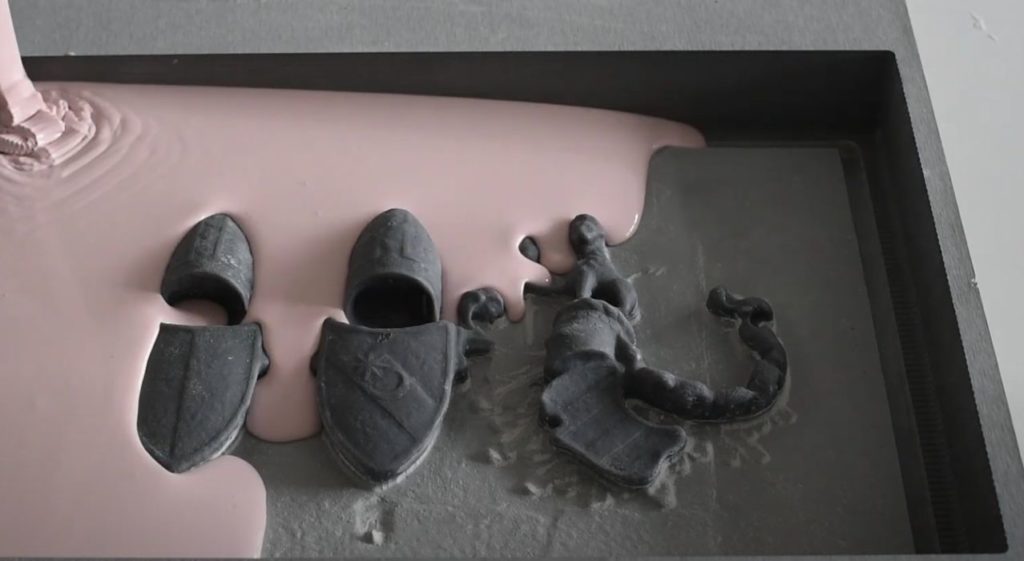
This might seem to be a straightforward project, but it was not. They explain:
“Each model took hundreds of hours to create with several stages of production carried out by researchers at the CFPR. This included translating real objects into digital models through photogrammetry, digital 3D modelling and digital sculpting. Digital models were then built using a variety of materials and techniques including Computer Numerically Controlled (CNC) routing, laser cutting and engraving, and resin 3D printing. One of the main challenges for researchers was to create a precise replica of an artefact, of considerable size and at reasonable expense, while ensuring the material was easy to maintain and pleasant to touch.”
Now that this project has been completed, it paves the way for future projects to be created for other heritage sites around the world, making our world more accessible to the visually impaired.