
Researchers have developed a method of 3D printing extremely small structures using copper.
Copper is an incredibly useful material, as it not only conducts heat very well, it also is an outstanding electrical conductor. That’s why you see it used in PCBs and heat exchangers.
As we’ve written previously, copper is an up and coming material in the 3D print space. The reason for this is certainly the utility of copper objects made with revolutionary complex designs.
Heat exchangers, for example, must deal with surface area exposed and at the same time air or liquid flow. The ability to create highly complex designs for heat exchangers using 3D printing means there will be more efficient components available for industry.
The same can be said for electronic components made with copper. For example, compact antennae can be created in a similar manner using complex copper structures.
The problem is that copper is a very difficult material to 3D print. It doesn’t really work well with standard LPBF processes because the copper reflects the laser energy all around the build chamber, messing up the print and potentially damaging components. Also, copper conducts heat quite efficiently, making the laser dot meltpool stretch much more than usual.
Options for 3D printing copper have been quite restricted. Here’s the few I know of:
- Digital Metal uses a cold binder jet 3D printing process and is able to print small detailed copper objects
- Desktop Metal also has a cold process and can 3D print objects in copper
- SPEE3D uses a supersonic process to kinetically bind particles, and can print copper objects with coarse resolution
- Markforged’s cold process can also 3D print small copper objects on their Metal X machine
- Xact Metal has found a way to adapt their small volume LPBF machine to attempt 3D printed copper objects
The finest resolution possible with these few copper metal options is from Digital Metal (now part of Markforged). Here you can see a 1cm cube made from copper, which provides a hint as to the maximum possible resolution for copper printing these days.
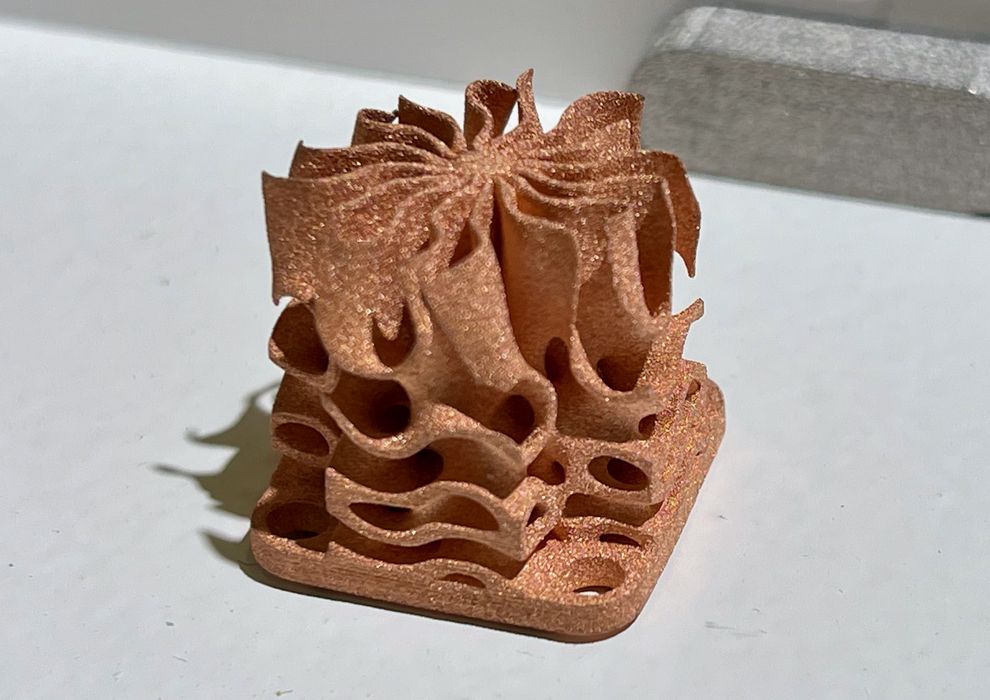
At present there is no way to 3D print tiny objects in copper, blocking quite an array of possible applications.
Now this could change as researchers published a new paper in the International Journal of Extreme Manufacturing (a journal that sounds quite interesting) entitled “Localized electrodeposition micro additive manufacturing of pure copper microstructures”.
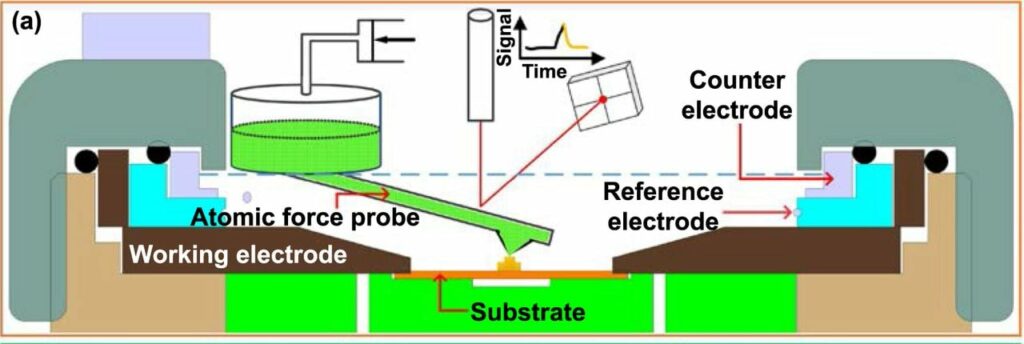
The researchers a new process they call “localized electrochemical deposition micro additive manufacturing”, or “LECD-μAM”. The process involves a combination of electrochemical deposition and atomic force servos.
The team was able to successfully 3D print a tiny spring in copper, with a wire length of only 0.320mm in about six minutes, shown at top.
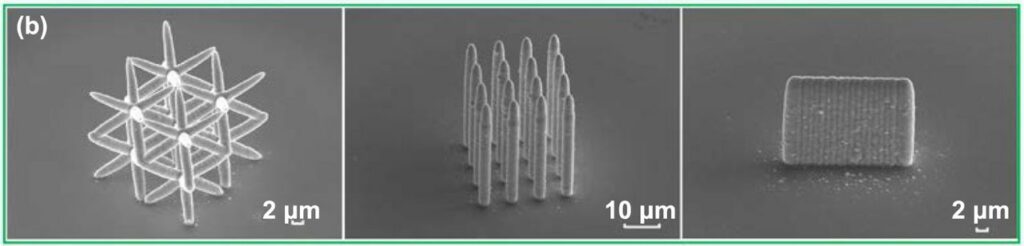
Normally, electrochemical deposition requires a mask, but in the new process no mask is required.
There are also several interesting positive aspects of LECD-μAM, including that it is more chemically friendly as it uses copper sulfate rather than more toxic liquids, and does not require an expensive environmentally controlled environment as LPBF does.
Finally, they say:
“These results delineate a new way of fabricating terahertz transmitter components and micro-helical antennas with LECD-μAM technology.”
Indeed. If this technology is commercialized, we could see, for example, highly compact and efficient 5G antennae in our new smartphones.
Via IOP Science