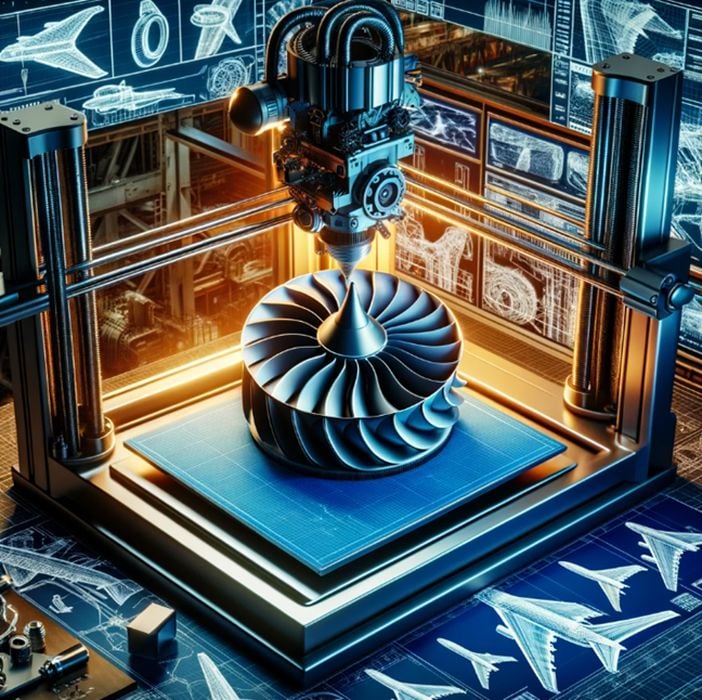
Charles R. Goulding and Warren Buzzell Jr. examine how 3D printing can be leveraged to address some of the recent challenges in aerospace component production.
The aerospace sector has been prompted to reassess its component inspection protocols in light of recent scandals involving counterfeit components, manufacturing defects, and misalignment in hole drilling operations.
While these incidents have not been directly linked to additive manufacturing or 3D printing technologies, it is imperative for the industry to closely monitor advancements in this domain and improve adherence to compliance procedures. Proactive self-regulation is often more advantageous than having external regulatory intervention. Given the current surge in demand for new passenger aircraft and Maintenance, Repair, and Overhaul (MRO) services, it is critical to mitigate any quality-related issues. The additive manufacturing sector is poised to adopt emerging technologies, such as artificial intelligence, automated drilling systems, and acoustic monitoring techniques (as seen in our recently written article, Innovative 3D Printing Solutions Addressing Counterfeit Parts Crisis in Aircraft MRO).
A recent analysis by The Wall Street Journal has raised questions regarding the necessity of increased human oversight in component inspections. This topic requires a thorough and industry-specific evaluation. The McKinsey railroad incident, a consequence of deliberate workforce reductions, is a cautionary tale about the repercussions of diminished inspection efforts. In contrast, industries such as electrical and electronics commonly implement comprehensive final product inspections, underscoring the importance of meticulous quality control. For good reason, the electronics industry often engages in 100 percent final product inspection. Similarly, the U.S. meat industry employs on-site governmental inspections to guarantee the safety and integrity of the food supply chain.
Inspecting 3D Printed Parts for Efficacy
In the rapidly evolving field of 3D printing, the implementation of rigorous inspection techniques is vital to ensure the efficacy and reliability of printed parts. These methods validate the integrity of the parts and play a critical role in advancing the technology and broadening its applications across various industries.
For instance, while elementary, visual inspection serves as the first line of defense against surface defects. It is particularly effective in identifying issues like warping or surface cracks that can compromise the structural integrity of a part. This method is easily deployable without requiring specialized equipment, making it a cost-effective and essential step in the quality control process. Dimensional accuracy measurements, often conducted using tools like calipers or coordinate measuring machines (CMM), ensure that the 3D-printed parts adhere to the precise specifications of the design. This precision is crucial in industries like aerospace and automotive, where even minute deviations can lead to significant functional failures.
Mechanical Inspection Techniques
Mechanical testing, which includes tensile, compression, and flexural tests, further contributes to understanding the material properties and behavior under various stress conditions. This information is vital for applications where the parts are expected to endure mechanical stresses, such as in manufacturing machinery or medical prosthetics.
Tensile testing is crucial for assessing a material’s strength and ductility. In this test, a 3D printed sample is subjected to a uniaxial force until it breaks. The resulting data, including tensile strength, yield strength, and elongation, are invaluable for applications where parts are under tensile loads. This test is particularly relevant for 3D printing, as the layer-by-layer construction can impact the material’s tensile properties differently in various orientations. Flexural testing determines the material’s stiffness and resistance to bending forces. This test is particularly relevant for thin, elongated parts like beams or shells, where flexural strength and modulus are critical parameters. In 3D printed objects, this test can reveal weaknesses in layer adhesion or anisotropy in mechanical properties due to the printing orientation.
Non-Destructive Inspection Techniques
Advanced techniques like non-destructive testing, including ultrasound and X-ray or CT scanning, offer deeper insights into the internal structure of printed parts. These methods are indispensable in detecting internal defects, such as voids or inclusions that are not visible on the surface but can significantly impact the part’s performance.
Surface roughness measurement, thermal analysis, and chemical analysis contribute additional layers of scrutiny, ensuring that the parts meet design criteria and adhere to material and functional standards. Together, these diverse inspection methods form a comprehensive approach to quality control in 3D printing, fostering trust and reliability in 3D printed products and encouraging their adoption across more critical and high-stakes applications.
Thermal analysis techniques, such as Differential Scanning Calorimetry (DSC), play a crucial role in understanding the thermal properties of materials used in 3D printing. DSC measures how a material’s heat capacity changes with temperature, providing essential insights into its melting point, crystallization, and phase transitions. This is particularly important for 3D printing materials like thermoplastics or metal powders, where thermal properties directly influence the printing process and the final part’s mechanical characteristics. Knowing the thermal behavior of these materials helps optimize the printing parameters, like the extrusion temperature, to ensure consistent quality. Additionally, thermal analysis can detect thermal degradation or residual stresses that may have been induced during the printing process, which could lead to premature failure of the part under operational conditions.
Microscopy provides a detailed examination of the microstructure of 3D printing materials. Scanning Electron Microscopy (SEM) offers high-resolution images of the surface and internal structure of a part, revealing details about the layer adhesion, porosity, and grain structure of the printed material. This is crucial for understanding how the printing process parameters, like layer thickness or print speed, affect the microstructural properties of the part. A well-optimized microstructure is key to achieving desired mechanical properties such as strength, ductility, and fatigue resistance. In metal 3D printing, for example, SEM can reveal the presence of microcracks or voids that can significantly impact the fatigue life of aerospace components. Microscopy analysis provides invaluable feedback for refining printing processes and developing materials with tailored properties for specific applications.
The Research & Development Tax Credit
The now permanent Research and Development (R&D) Tax Credit is available for companies developing new or improved products, processes, and/or software.
3D printing can help boost a company’s R&D Tax Credits. Wages for technical employees creating, testing, and revising 3D printed prototypes can be included as a percentage of eligible time spent for the R&D Tax Credit. Similarly, when used as a method of improving a process, time spent integrating 3D printing hardware and software counts as an eligible activity. Lastly, when used for modeling and preproduction, the costs of filaments consumed during the development process may also be recovered.
Whether it is used for creating and testing prototypes or for final production, 3D printing is a strong indicator that R&D Credit-eligible activities are taking place. Companies implementing this technology at any point should consider taking advantage of R&D Tax Credits.
Conclusion
In conclusion, the additive manufacturing sector should take cues from the recent challenges faced in aerospace component production and strive for enhanced inspection methodologies. An optimal approach combines the expertise of skilled inspectors with the utilization of advanced technological tools.