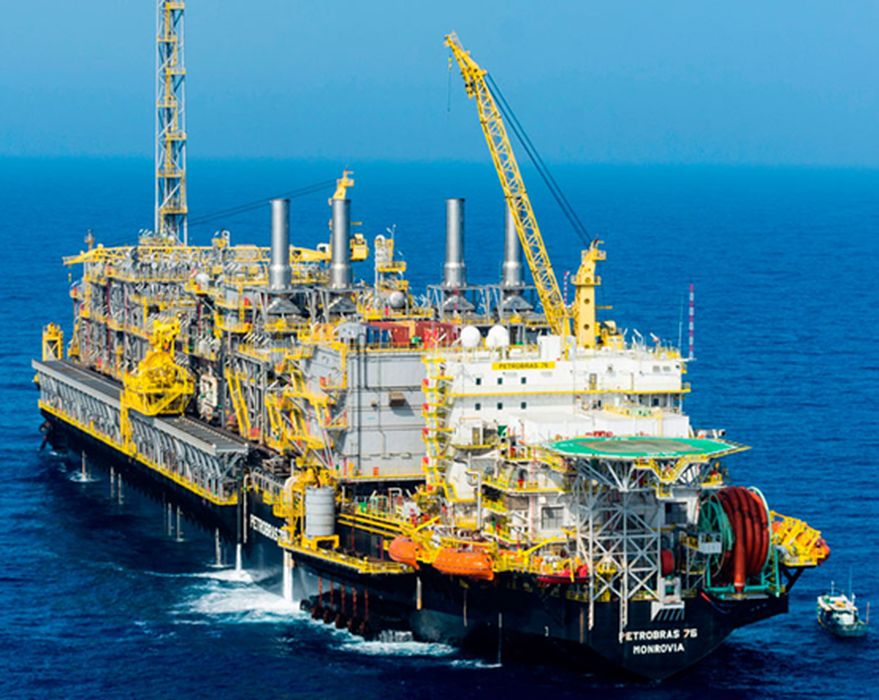
Charles Goulding and Andressa Bonafe examine 3D printing technology at Petrobras in Brazil.
2021 has been an important year for 3D printing at Petróleo Brasileiro SA (Petrobras), a state-owned multinational with over 41 thousand employees and $53 billion in revenue. Founded in 1953, the Brazilian company controls significant oil and energy assets in 16 countries. It engages in oil and gas exploration, production, and distribution activities, which span six business areas, namely:
- Exploration and Production, which involves crude oil, natural gas liquids, and natural gas exploration, development, and production;
- Refining, Transportation, and Marketing, which includes refining, logistics, transportation, trading operations, oil products, crude oil exports and imports, and petrochemical investments;
- Gas and Power, particularly transportation and trading of natural and liquefied natural gas, generation and trading of electric power, and the fertilizer business;
- Distribution of oil products, ethanol, biodiesel, and natural gas to wholesalers and through the Petrobras Distribuidora S.A. retail network in Brazil;
- Biofuels, which include the production of biodiesel and its co-products and ethanol-related activities, such as equity investments, production and trading of ethanol, sugar, and the excess electricity generated from sugarcane bagasse; and
- International exploration and production of oil and gas, refining, transportation and marketing, distribution and gas, and power operations outside of Brazil.
Despite recent political turmoil concerning the successive increases in fuel prices and risk of government interference, Petrobras continues to thrive and invest in innovative ways to increase the efficiency of operations. Working in partnership with the German manufacturer of optical systems Carl Zeiss and the Brazilian non-profit research and technology organization, SENAI, Petrobras is advancing the use of additive manufacturing for the production of critical oil and gas components. Ongoing research focuses on metal 3D printing methodologies, particularly Laser Beam Powder Bed Fusion (PBF-LB) as well as Laser Beam Directed Energy Deposition (DED-LB).
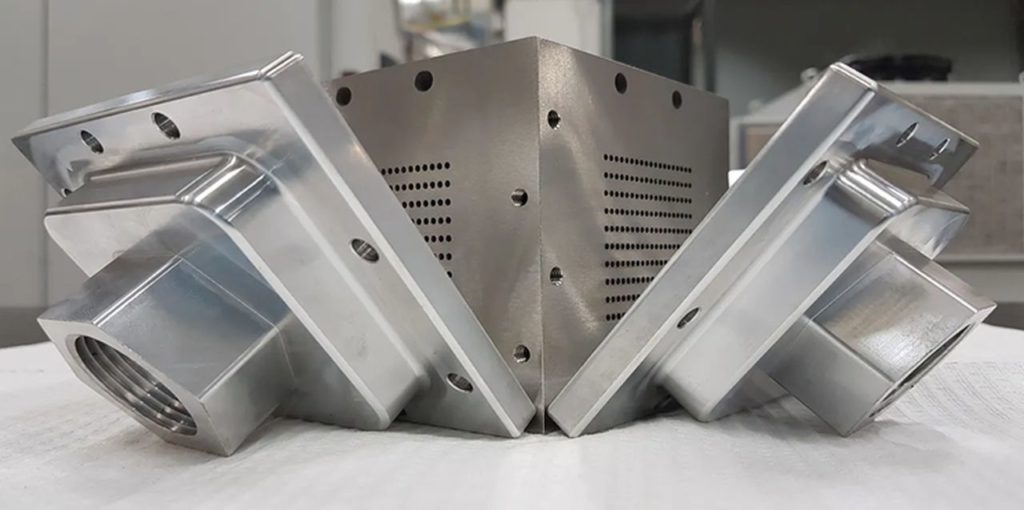
According to Zeiss, the goal of the partnership is to develop and validate approaches for the manufacturing and qualification of static and dynamic critical components for the oil and gas industry. The international consortium is particularly interested in deepening the understanding of powder aging and the influence of powder degradation on defects in the final parts. Using multiscale multitool computed tomography strategies for rapid parameter development and process stability, the two-year initiative aims to positively impact the oil and gas supply chain in the medium and long term.
Challenges and Opportunities for the Oil and Gas Industry
3D printing technologies can be greatly beneficial to the oil and gas industry. Among the most relevant opportunities are the potential to decrease time to market in tightly scheduled projects and to provide replacement parts for legacy equipment often situated in remote areas. In this context, avoiding costly downtime that usually accompanies the replacement of critical parts would represent major savings and greater competitiveness.
Costs related to tooling and transportation can also be significantly reduced due to low-volume production and localized digital manufacturing networks. Logistical advantages are particularly relevant for those doing business in emerging countries, where imports can be costly and time-consuming.
Examples of energy applications that can be prototyped and produced with 3D printing are very diverse and include gas turbine nozzles, sand control screens, turbomachinery, subsea chemical stick injection tools, sealing accessories, perforated pup joints, liner hanger spikes, drill bits, jigs and fixtures, pressure gauge pieces, control-valve components, among many others.
The ongoing expansion of 3D printing materials shows great promise for the oil and gas industry, as there is a growing number of options that combine hydrocarbon resistance, good tensile properties, and high heat deflection.
However, there are still many challenges to the more widespread adoption of 3D printing for oil and gas applications, particularly beyond polymers. Daniel Huamani, CTO at 3DCRIAR, underlines the importance of advancing the use of metal, which has the greatest potential to impact areas of higher value-added, specifically exploration. Daniel, who has substantial experience in oil and gas and was interviewed for this article, points out that the ability to quickly produce metal parts with complex geometries will be a game-changer for the performance of machinery, from pumps to heat exchangers.
Meeting very stringent regulatory standards for oil and gas applications, nonetheless, will require continued research and development efforts. In order to be cleared for use in oil platforms, parts must go through a comprehensive certification process designed to assess their safety. To this end, Petrobras’ ongoing initiatives are essential to ensuring that the oil and gas industry will soon be able to take full advantage of the great benefits of additive manufacturing.
US-based companies engaged in similar efforts can take advantage of R&D tax credits, as described below.
The Research & Development Tax Credit
The now permanent Research and Development (R&D) Tax Credit is available for companies developing new or improved products, processes and/or software.
3D printing can help boost a company’s R&D Tax Credits. Wages for technical employees creating, testing and revising 3D printed prototypes can be included as a percentage of eligible time spent for the R&D Tax Credit. Similarly, when used as a method of improving a process, time spent integrating 3D printing hardware and software counts as an eligible activity. Lastly, when used for modeling and preproduction, the costs of filaments consumed during the development process may also be recovered.
Whether it is used for creating and testing prototypes or for final production, 3D printing is a great indicator that R&D Credit eligible activities are taking place. Companies implementing this technology at any point should consider taking advantage of R&D Tax Credits.
Conclusion
There are many challenges and opportunities for 3D printing in the oil and gas industry. Petrobras’ research efforts show great promise for the advancement of metal applications, however, the path to meet safety standards may not be an easy one. No matter the obstacles ahead, it seems evident that additive manufacturing is bound to revolutionize the oil and gas market around the globe, sooner or later.