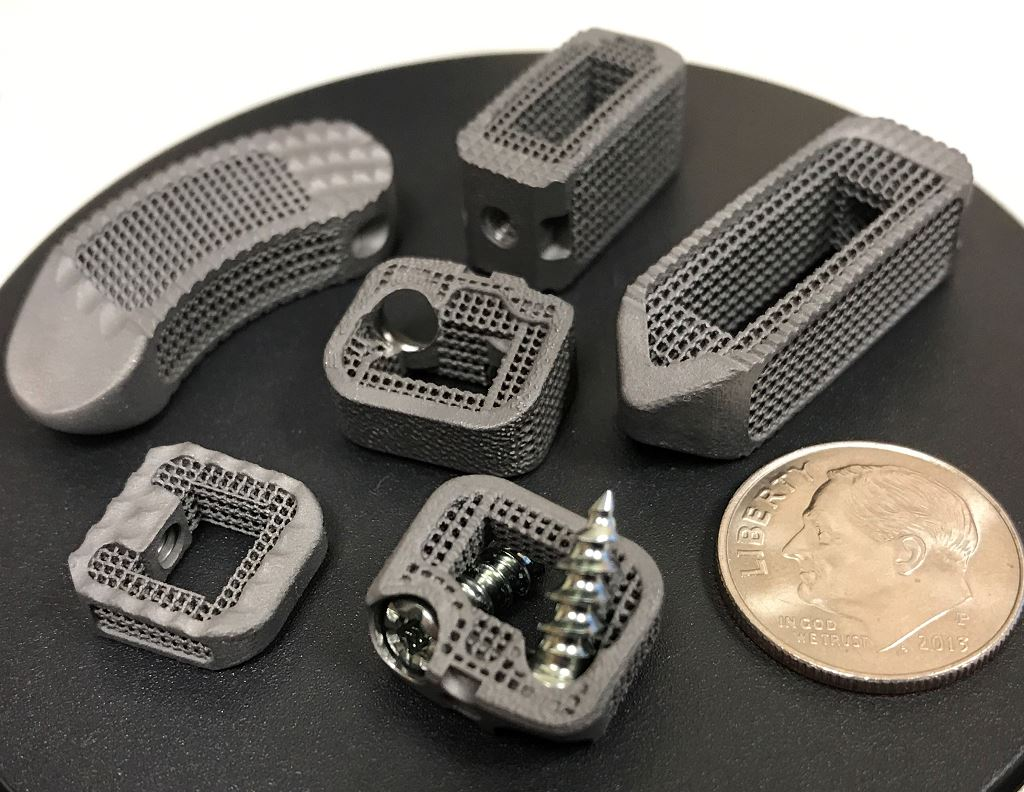
Charles R. Goulding and Peter Favata examine 3D printing being used for more advanced spinal surgical care.
In the United States, over 1 million instrumented spinal procedures are performed every year.
The spine is one of the most important skeletal structures in the human body. It gives the body support and structure allowing one to move freely while protecting the spinal cord, which is what connects the brain to the rest of the body. Patients undergo a variety of spinal surgeries, the most common being spinal fusion and artificial disc replacement. Spinal fusion involves fusing two or more of the spine’s vertebrae together, eliminating the movement in between those vertebrae. Artificial disc replacement involves removing a spinal disc that is damaged beyond repair and replacing it with an artificial one.
In addition to creating biomodels and guides, 3D printing allows surgeons to design a prosthetic that fits perfectly to the patient. Most off-the-shelf spinal implants are used to stabilize the bones and correct the problem before fusing the bones together. In situations where there is severe spinal degeneration or an issue that makes it difficult to reconstruct, a unique titanium implant can be printed and attached directly to the spine.
3D printing technology is rapidly transforming the way that medical devices such as spinal implants are created and the field of orthopedics has much to gain from this evolution. Today, a broad range of medically-certified systems now exist that enable the production of 3D printed spinal implants. With additive manufacturing, cages and interbody fusion devices can be fabricated with a high level of design freedom that enables the creation of complex shapes with improved mechanical and material properties.
Now, 3D printing is being utilized for spinal surgeries around the world.
Companies 3D Printing Spinal Implants
The global spinal implants market is predicted to exceed US$19.5 billion by 2024. All over the world, companies are investing in additive manufacturing to assist in spinal implant R&D and production. Let’s take a look at just some U.S. companies doing just that:
Stryker Corporation, a major medical technologies corporation based out of Kalamazoo, Michigan, has made significant investments in additive manufacturing technology. Stryker already has a range of 3D printed spinal implants designed for bone-in growth and biological fixation. We recently covered Stryker’s acquisition of Wright Medical and its implications on 3D printing for the company’s growing implant portfolio.
Medtronic, a global leader in medical technology, recently announced its acquisition of spinal surgery company Medicrea. Medicrea’s dedicated 3D manufacturing facility will expand Medtronic’s ability to develop custom medical products, including its line of 3D printed titanium spinal implants. Combining Medicrea’s 3D printing capabilities and spinal surgery expertise with Medtronic’s expansive portfolio of technology and data could lead to significant advancements in surgeries and patient care.
After investing in metal 3D printing to advance its spinal implant production, Indiana-based Nexxt Spine has received FDA clearance of its 3D printed NEXXT MATRIXX Stand Alone Cervical System. This year, the company has expanded its Noblesville, Indiana campus in order to house additional 3D laser beam printers. The expansion includes tripling the size of the 3D printing room, creating a dedicated test lab, and tripling the class 10,000 cleanroom – demonstrating the company’s commitment to design and produce industry disrupting products using state of the art equipment and infrastructure.
Since being founded in 2012, Dallas, Texas based medical device startup Osseus Fusion Systems has focused on the development of advanced medical products for spinal related injuries. One of Osseus’ key goals is using new, emerging technologies such as additive manufacturing, to improve the quality and capabilities of its products. The company’s Aries titanium implants are some of the most porous on the market, allowing for better fusion to other bone structures.
3D printing and similar activities used for developing innovative medical devices such as implants may be eligible for R&D Tax Credits.
The Research & Development Tax Credit
Whether it’s used for creating and testing prototypes or for final production, 3D printing is a great indicator that R&D Credit eligible activities are taking place. Companies implementing this technology at any point should consider taking advantage of R&D Tax Credits.
Enacted in 1981, the now permanent Federal Research and Development (R&D) Tax Credit allows a credit that typically ranges from 4%-7% of eligible spending for new and improved products and processes. Qualified research must meet the following four criteria:
- Must be technological in nature
- Must be a component of the taxpayer’s business
- Must represent R&D in the experimental sense and generally includes all such costs related to the development or improvement of a product or process
- Must eliminate uncertainty through a process of experimentation that considers one or more alternatives
Eligible costs include US employee wages, cost of supplies consumed in the R&D process, cost of pre-production testing, US contract research expenses, and certain costs associated with developing a patent.
On December 18, 2015, President Obama signed the PATH Act, making the R&D Tax Credit permanent. Beginning in 2016, the R&D credit can be used to offset Alternative Minimum tax for companies with revenue below $50MM and, startup businesses can obtain up to $250,000 per year in payroll tax cash rebates.
Conclusion
3D printing is quickly becoming a useful tool for surgeons who are undertaking spinal surgery. Having the ability to create an implant that will perfectly fit the patient’s spine can help accomplish a more successful surgery then compared to off-the-shelf implants. As of now, 3D printing implants are not a viable option to anyone needing an emergency surgery being that it takes longer. However, the technology is quickly progressing and eventually we could see 3D printers directly in hospitals to create these spine implants on site.