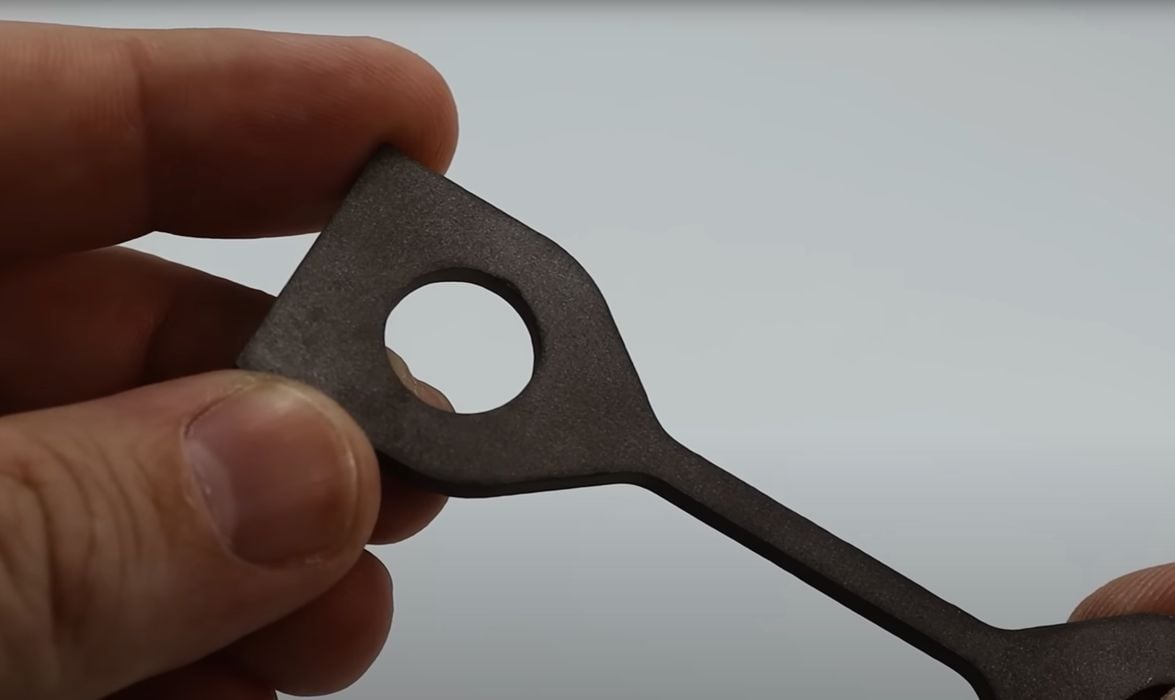
A very surprising analysis of 3D printed metal versus CNC milling has been completed.
YouTube channel electrosync performed a fairly comprehensive test of tensile strength for a wide variety of materials, in both 3D printed and CNC milled form. The results were a bit shocking.
The test set a baseline by performing pull-tests on a standard coupon using several polymer materials, starting with PLA. This test found the PLA to fracture at the 55kg level, with an elongation of 0.3%. Some variations of infill were attempted, which somewhat increased part strength, as one would expect.
From there the tests used stronger materials.
The testing used Markforged’s Onyx FR material, with continuous carbon fiber. That’s substantially stronger than mere PLA, and the results showed this is indeed true. electrosync tested a variety of Onyx FR materials, and found them to have varying, but quite strong results.
Then the focus was on 3D printed metals. These were obtained by electrosync through an unnamed service bureau that produced them using the SLM process. Aluminum, stainless steel, tool steel and even titanium were tested. As you might expect, these were significantly stronger than either the PLA or reinforced polymer materials.
Then the testing shifted to CNC milled parts, which were the same coupon, but were cut by a service bureau using CNC milling equipment.
The results for the CNC’d parts were quite strong, but surprisingly they were all somewhat less strong than their 3D printed equivalents!
How could 3D printed parts be stronger than CNC milled parts? The general assumption is that layer-by-layer production should be less strong than “solid metal” CNC parts because of the possibility of delimitation of layers.
That apparently was not the case in electrosync’s testing. Each of the CNC’d parts were less strong than the 3D printed coupons using the same test equipment and procedures.
In the video, electrosync offers no reason for this result, so we are left to speculate.
If I may speculate, I suspect the results may have something to do with the crystalline microstructure of the respective materials. It’s possible that the chunk of metal from which the CNC milling took place cooled from the outside – in, leading to potentially different microstructure throughout the metal.
On the other hand, the SLM printed metal coupons would have had very consistent microstructure because the conditions during printing are identical on each layer. In fact, metal 3D printer operators spend considerable effort to tune the parameters, including speeds, energy and temperatures to generate the best possible microstructure.
What could this mean?
One possibility is that with this knowledge it would be possible to use smaller — and lighter weight — parts in certain applications by choosing 3D printing over CNC milling.
Another possibility is that this might be the harbinger of the future: what happens in a world where 3D printed parts are ALWAYS stronger than conventionally made parts.
I think there might be a great many more 3D printers in that case.
Via YouTube