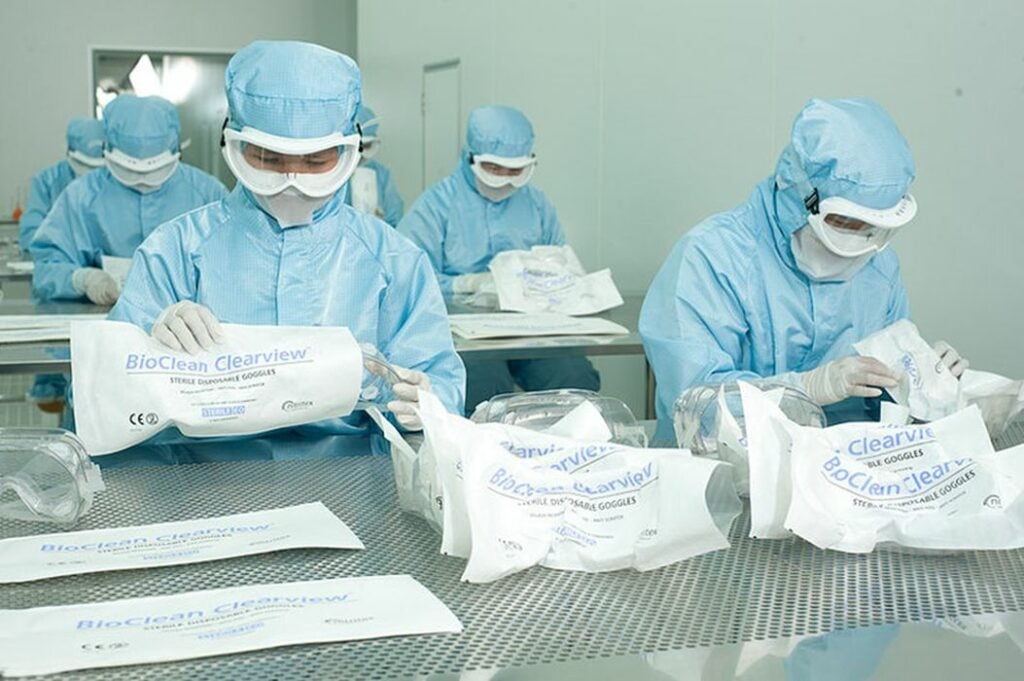
Charles R. Goulding and Julia Wallace look at the possibilities of using 3D printed parts in clean room environments.
A cleanroom is an area in which pollutants like dust and airborne microbes are filtered out of the air, keeping that area as clean as possible. It is maintained by a filter system that decontaminates air from outside the room, then forces that air into the room while forcing out contaminated air from within.
Cleanrooms are used in many fields that require pristine environments, such as biotech and pharmaceutical companies, as well as certain types of manufacturing, including aerospace and microelectronics. Any sort of contamination in these industries could lead to major defects in products and cause issues with production.
In order to keep a cleanroom as clean as possible, everyone and everything in it must also be as clean as possible. Protective clothing and specific furniture are made to prevent possible contaminants from floating around the room.
There are different classes of cleanrooms as regulated by ISO, ranging from ISO 1 (extremely clean) to ISO 9 (clean), and are measured in terms of particles/m3 of air, and each class requires a certain number of air changes per hour (volume of air filtered in an hour/volume of the room), with a higher average correlating to a cleaner room. Different industries require different classes of cleanrooms, and cleanroom manufacturers must adhere to these ISO standards.
3D Printing and Cleanrooms
In the past, many engineers and scientists have been hesitant to utilize 3D printed devices in cleanrooms for fear that these devices would generate too many particles.
However, new research has been published within the last 5 years showing evidence to the contrary. A study from 2019 showed that 3D printed objects used in semiconductor processing contained no harmful metal impurities other than those from colorants, which can be avoided using natural-colored filaments.
Another study from 2018 demonstrated that fused filament fabrication-based 3D printed materials are compatible with the solvents, acids, bases, and solutions used in the wet processing of semiconductor materials. Together, these studies show at least one proven way that 3D printing is compatible with regular production in a cleanroom.
The Research & Development Tax Credit
The now permanent Research and Development (R&D) Tax Credit is available for companies developing new or improved products, processes and/or software.
3D printing can help boost a company’s R&D Tax Credits. Wages for technical employees creating, testing and revising 3D printed prototypes can be included as a percentage of eligible time spent for the R&D Tax Credit. Similarly, when used as a method of improving a process, time spent integrating 3D printing hardware and software counts as an eligible activity. Lastly, when used for modeling and preproduction, the costs of filaments consumed during the development process may also be recovered.
Whether it is used for creating and testing prototypes or for final production, 3D printing is a great indicator that R&D Credit eligible activities are taking place. Companies implementing this technology at any point should consider taking advantage of R&D Tax Credits.
Conclusion
Now that the use of 3D printed materials in cleanrooms without risk of contamination has been backed by scientific evidence, it is expected that this practice will continue to grow. Adding to the numerous practical applications of 3D printing, industries that use cleanrooms to produce and manufacture will do so much more quickly, using additive manufacturing rather than traditional methods.