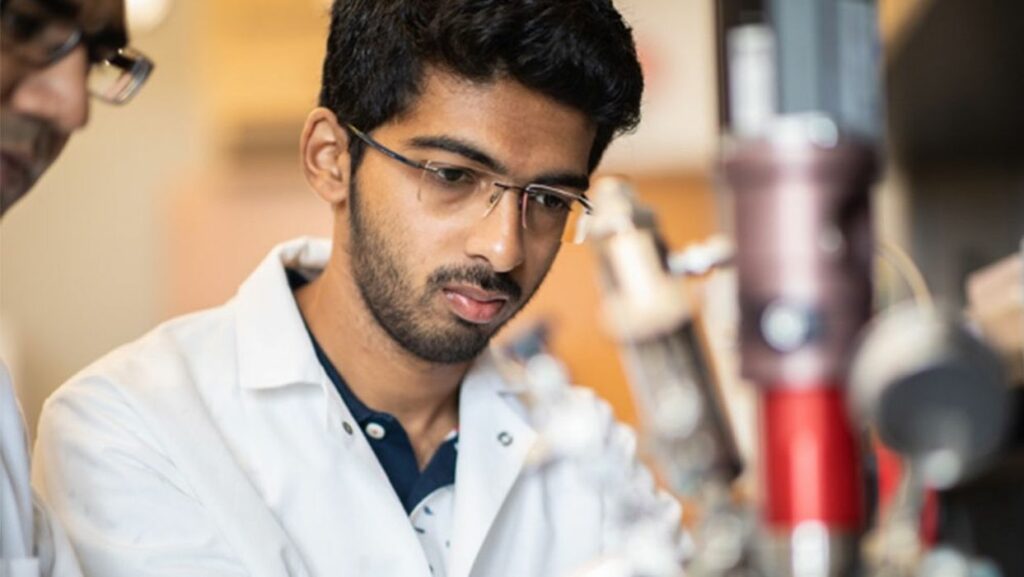
New research seems to have developed a way to 3D print bioelectronic components.
3D printed electronics are not a new thing; they’ve been around for many years. It’s a simple matter of using a conductive material and embedding that into the print. Electricity and/or signals can traverse the conductive paths for a functional purpose.
However, when you consider the idea of 3D printing an electronic system intended to be placed inside a human body, then things get a lot more complicated.
For starters, the object should be able to flex, because parts of the body can move, and an embedded bioelectronic system should be able to twist without breaking — and still function electronically.
Secondly, the object had better be biocompatible. That means the material used must be biocompatible.
That’s challenging because many of the major 3D printing processes use the principle of photo polymerization, in which energy is used to selectively fuse solid portions of a vat of resin.
What’s happening is that the energy affects photoinitiatior molecules mixed into the resin. Those molecules curl up and interlock, creating the rigidity when they absorb sufficient radiation.
The problem is that today’s photoinitiators are toxic, and thus incompatible with biological use.
The new research from Texas A&M University seems to have developed a material that overcomes these challenges and also provides notable electrical properties. The paper abstract explains:
“To address these challenges, we developed a class of shear-thinning hydrogels as biomaterial inks for 3D printing flexible bioelectronics. These hydrogels are engineered through a facile vacancy-driven gelation of MoS2 nanoassemblies with naturally derived polymer-thiolated gelatin. Due to shear-thinning properties, these nanoengineered hydrogels can be printed into complex shapes that can respond to mechanical deformation.”
They say that the shapes 3D printed with this material can deform as much as 80% and still recover their original geometry. This is apparently of a sufficient level to work within virtually the entire range of human body mechanical movement.
As for electrical properties, the new material is said to be “highly conductive”, making it ideal for electronic applications.
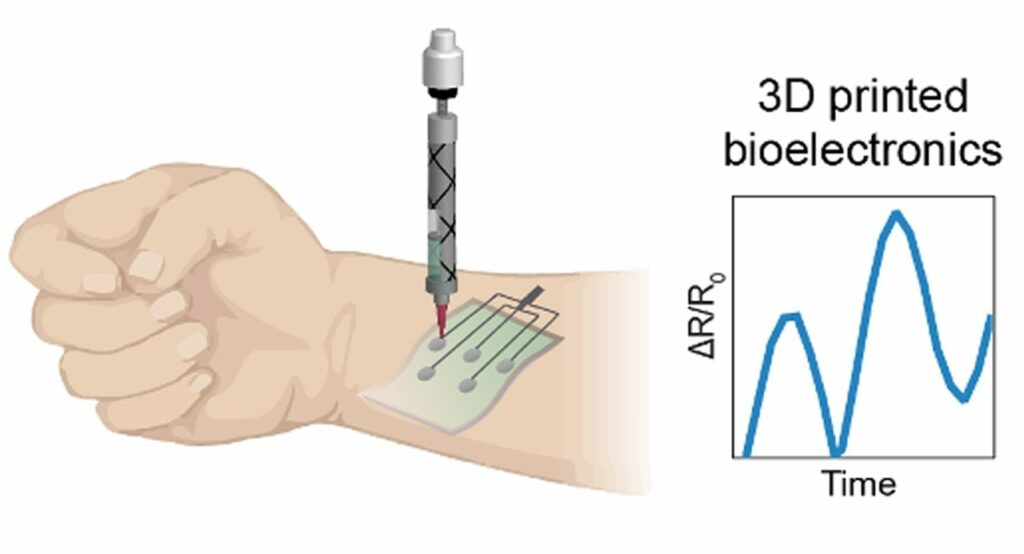
What are the implications of this development? The researchers speculate on what may come next:
“The 3D printed cross-linked structure demonstrates excellent strain sensitivity and can be used as wearable electronics to detect various motion dynamics. Overall, the results suggest that these nanoengineered hydrogels offer improved mechanical, electronic, and biological characteristics for various emerging biomedical applications including 3D printed flexible biosensors, actuators, optoelectronics, and therapeutic delivery devices.”
Where will this lead? This development opens the door for inventors to devise new kinds of embedded systems that can be quickly 3D printed and implement functions we can only imagine.