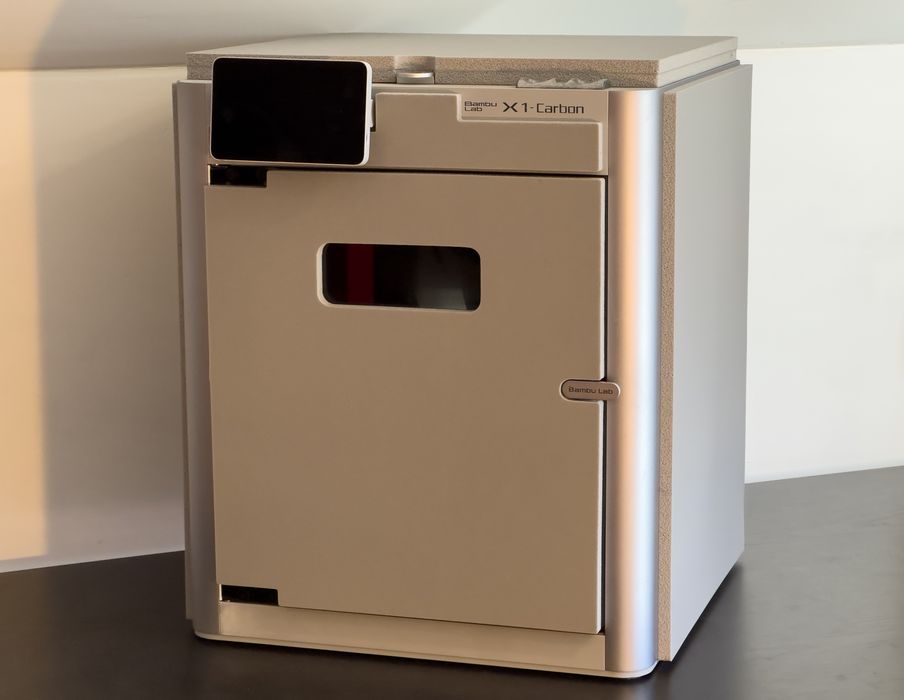
This month’s community support selection is the HPPS Project for Bambu Lab X1C/E machines.
Fabbaloo selects worthy non-profit projects or activities contributing to 3D printing and provides not only a published story on the project, but also free advertising on our well-read pages. If your project would like to take part in the program, please fill out our application form here.
The “High Performance Panel System” (HPPS) project attempts to provide a unique method of improving the print quality and energy consumption of the popular Bambu Lab X1C/E 3D printers. We spoke with the person behind the project, Peyton Oakes-Bryden.
Fabbaloo: How did you become involved in 3D printing?
Peyton Oakes-Bryden: My journey into 3D printing began in 2015 during my high school years, starting with the purchase of a Markforged Mark 2.
Since then I’ve had the pleasure to own or work with nearly every 3D printing technology type. At this moment my personal farm consists of a wall of X1C’s, a few P1S’s & a Form 3. For me additive is just exciting from a design creativity perspective, (particularly with FDM) it forces you to get creative with application specific solutions and generally makes you a better engineer across all fabrication regimes; the speed of producing multiple parts of a multi-part assembly, simultaneously is sweet too.
Fabbaloo: When did you first use Bambu Lab printers, and what were your initial thoughts?
Peyton Oakes-Bryden: I acquired my first 2 Bambu Lab X1C printers in December 2022 and was impressed by their reliability and speed in printing prototypes and end-use parts. This was particularly notable after I switched to textured PEI & G10 build plates, which enhanced adhesion and allowed for more consistent results, enabling the development of a whole host of process improvements.
Fabbaloo: What led to the creation of the HPPS project?
Peyton Oakes-Bryden: The project was initiated after noticing the excessive heat generated by the X1C printers during extended use. A comprehensive thermal analysis revealed significant heat loss through the printer’s glass and aluminum parts, leading to the development of the HPPS.
In the real world, HPPS reduces the power consumption by 15-30% for higher-temperature materials in standard conditions, and up to 40% in colder environments. It improves chamber temperatures without risking overheating (through some clever thermal design), facilitates printing with higher-temperature materials in cooler environments, speeds up the warming process of the printer, and enhances fire safety in the event of an electrical fire.
Unlike nearly any other foam, HPPS does not produce toxic fumes in the event of an electrical fire as it is made of a specific, in-house formulated foamed silicone.
Fabbaloo: How is the HPPS system installed and used?
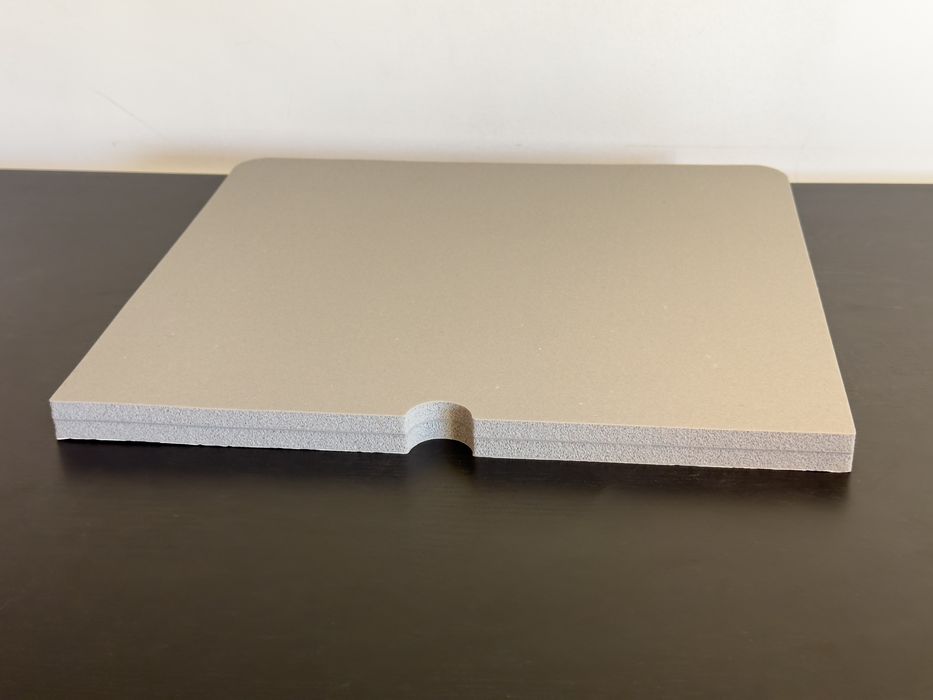
Peyton Oakes-Bryden: Installation involves attaching foamed silicone panels with pre-applied, High-Temp 3M adhesive to specific areas of the printer, requiring no additional tools or modifications.
The HPPS design ensures it does not negatively impact printer operations, even when printing materials like PLA at higher bed temperatures, by using a 3D printed top cover riser to adjust thermal effects.
The 3M adhesive on HPPS generally allows for 2-3 quick remove-and-replace operations at initial application, allowing for easy re-alignment (if required).
Fabbaloo: What is the cost of the HPPS, and how can it be ordered?
Peyton Oakes-Bryden: Priced at $150, HPPS is available for reservation through a Google form. It represents a community-driven, non-profit initiative to provide a high-quality thermal management solution at an accessible price point. With higher order quantities the cost of producing HPPS will decrease and so the price will go down.
Fabbaloo: What has been the user experience with HPPS, and how many are currently installed?
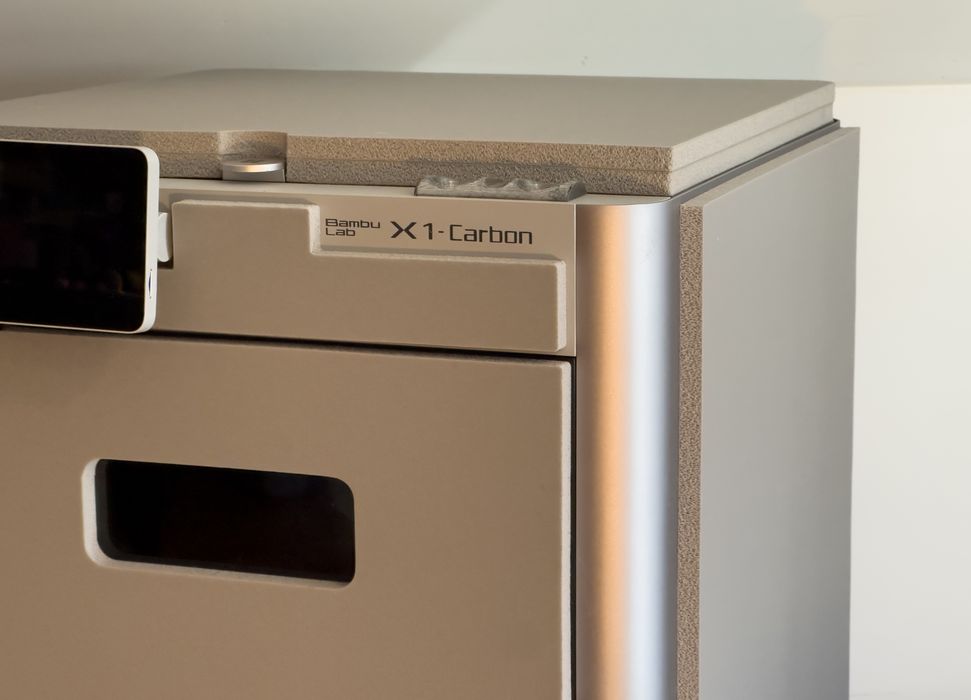
Peyton Oakes-Bryden: Users have reported significant benefits, including reduced heat-up times, higher chamber temperatures, and improved thermal stability. Currently, 9 units are installed externally in commercial, consumer, and industrial environments.
Every beta user of the HPPS has paid 150$ for their unit(s) and has subsequently reserved an additional 1-7 units. Feedback highlights the system’s ability to enable printing in colder environments and improve overall printer performance without the need for expensive upgrades.
A customer has also remarked on the protection HPPS offers for the top panel, having had a 1/2” Dewalt impact wrench drop onto the top of the unit (from a wall mount roughly 3 feet above) without damaging the printer.
Fabbaloo: Will there be further developments to the HPPS design?
Peyton Oakes-Bryden: While the current version, Gen 3 HPPS, is set to be distributed to those who reserved it, we are open to making further improvements based on feedback from a larger user base. Community remixes will be supported.
Fabbaloo: Are you working on any other printer modifications?
Peyton Oakes-Bryden: Yes, we are developing a magazine-fed, automatic build plate changer for the X1/P1 series.
Via LinkedIn and Google Forms