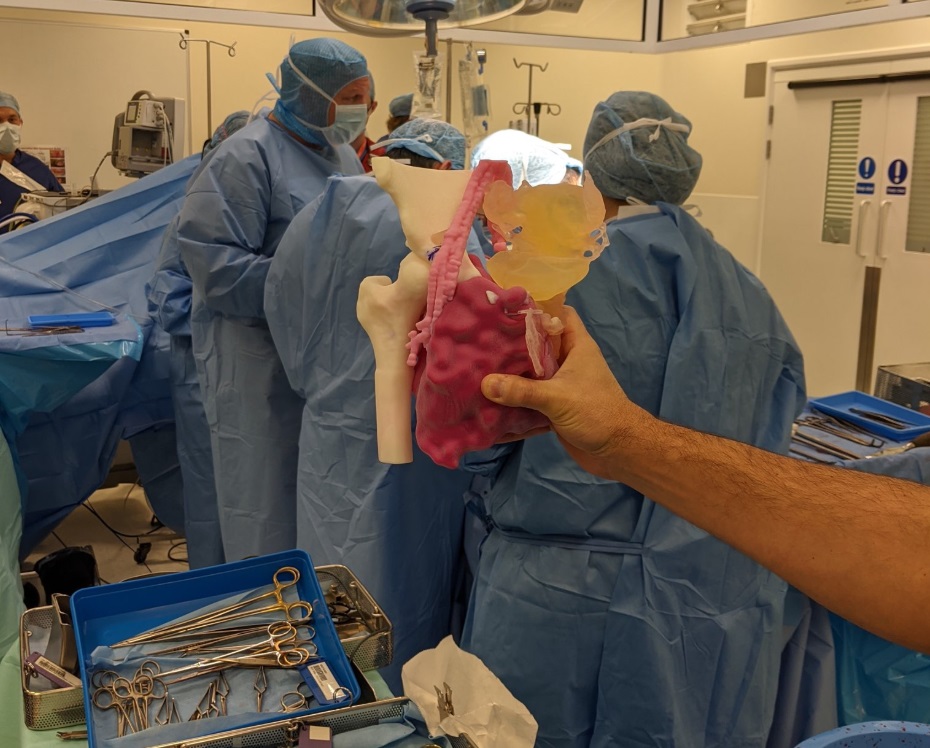
This week, UK-based 3D LifePrints announced a new certification that further validates its patient-specific medical 3D printing focus.
The certification, ISO 13485:2016, relates to the company’s Quality Management System (QMS). Such recognitions are critical to the expansion of 3D printing in the medical field, which obviously requires significant attention to quality and adherence to standards.
“An internationally recognised standard of excellence, ISO 13485:2016 is a stringent set of guidelines for the medical device industry. The standard ensures that an organisation maintains its quality and compliance levels specific to the design, manufacture and distribution of medical devices,” the 3D LifePrints announcement explains of this certification.
3D LifePrints has been making excellent headway in the medical 3D printing field. Their models, built from patient imaging data, allow for both medical professionals and patients to clearly understand specific anatomical situations. The company also has operations focusing on surgical guides, implants, and bioprinting — all specific to individual patients. Advanced procedures, including those employing robotic simulation, are enabled through their high-tech medical approach.
With the new certification, 3D LifePrints explains, the team can now expand its point-of-care model. This is set to include new sterilizable surgical guides and anatomical models, all of course patient-specific.
“It has long been our goal to standardise our processes by adherence to this internationally recognised standard. The formal certification of our QMS opens up considerable market opportunities for the business and is a clear signal to our customers of the importance we attach to Quality Assurance and Patient Care,” 3D LifePrints CEO Henry Pinchbeck says.
These market opportunities aren’t just marketing; ISO certifications and their like are vital to the ongoing expansion of real-world usage for 3D printing.
Ensuring that new technologies meet or exceed existing standards is key to actual adoption of 3D printing in point-of-care situations. Recognition in the US with FDA approval and in Europe with CE marking, or with ISO standards, back up claims with evidence. That is: not only do companies say they can safely 3D print guides and devices that can be used in medical environments, they can prove it. These 3D printed medical devices are held to the same standards as traditionally manufactured devices.
The new certification at 3D LifePrints is built upon the company’s Digital Platform Embedmed, and “includes the design and manufacture of sterilisable devices within a Controlled Environment in one of 3D LifePrints’ embedded Hubs.”
The “hub” operating model sees 3D LifePrint technology housed in host institutions. These can then in turn offer point-of-care service incorporating biomedical engineers along with the 3D printing hardware and software necessary to create the patient-specific services. An in-house structuring also reduces wait time; rather than wait weeks for an ordered device to come in, medical practitioners can have their patient-specific guides in hand in days.
To date, 3D LifePrints has installed hubs in Alder Hey Children’s Hospital in Liverpool, Nuffield Orthopaedic Centre in Oxford, Wrightington Hospital in Greater Manchester, and Leeds General Infirmary.
“3D printing offers some really unique and exciting opportunities to change the way that we teach, plan and undertake surgical interventions in orthopaedics. 3D LifePrints are leading the way. The models can be designed to a specific criteria. No two children, or conditions are the same, so a 3D model of a patients problem can only benefits the training, and ultimately the care they receive,” said Consultant Orthopaedic Surgeon Daniel Perry of Alder Hey Children’s NHS, Liverpool, UK.
These hubs may be set to expand with the new confidence boost of an important ISO certification.
Via 3D LifePrints