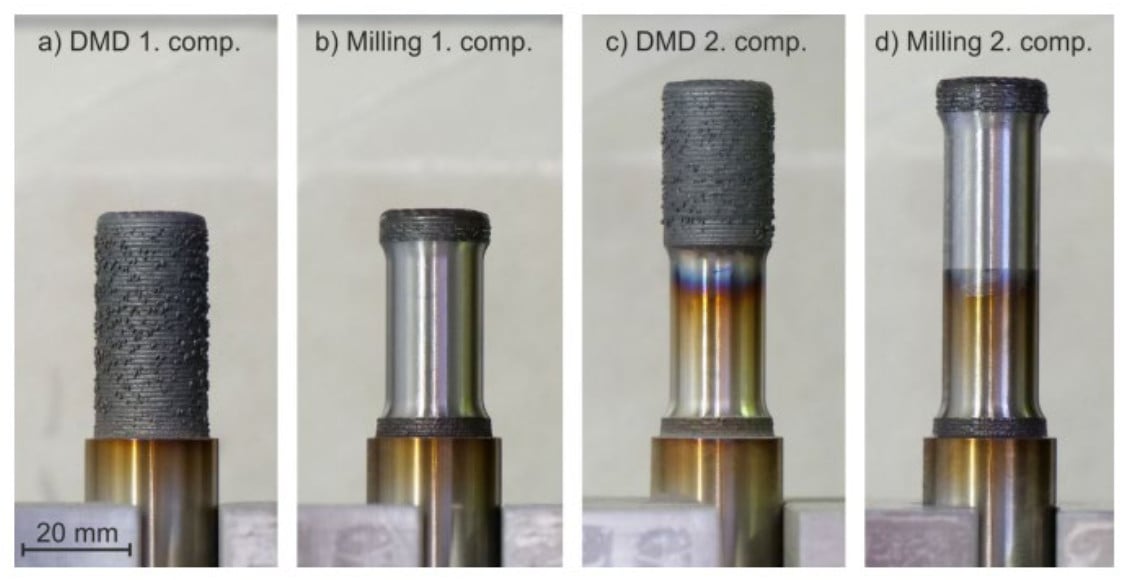
Oak Ridge National Laboratory report highlights additive manufacturing applications for hydroelectric power industry.
In modern debates about power generation—whether in Congress or the coffee shop—the dichotomy is almost always between wind and solar on the one hand and coal and gas on the other. Nuclear might come up as a third option if both sides are feeling tired of rehashing the same old arguments, but hydropower never seems to get the same level of attention.
Perhaps it’s because hydroelectric power is so dependent on location, even more than wind or solar. It’s easy to forget that almost a third of all renewable energy generated in the U.S. comes from hydropower if you don’t work in the industry or live near a major dam. But hydroelectric power has been lighting up our homes and business for a long time. It’s an industry built on traditional manufacturing methods and materials.
Unfortunately, that may be it’s biggest weakness.
Between international supply-chain issues, ongoing maintenance needs and environmental-impact mitigations, the U.S. hydropower industry is very much in need of an update. According to a recent report from Oak Ridge National Laboratory (ORNL), the time is right for advanced manufacturing and materials to bring the hydropower industry up to speed.
Challenges Facing U.S. Hydroelectric Power
The report, entitled Advanced Manufacturing and Materials for Hydropower: Challenges and Opportunities, is a joint effort of ORNL, GE Research, the Department of Energy’s Water Power Technologies Office and Kearns & West. It was informed by literature reviews, stakeholder interviews and an in-person workshop at the Oak Ridge National Laboratory Manufacturing Demonstration Facility.
One of the most pressing challenges for this industry is maintenance, brought on by the aging of the existing hydropower fleet. Repairs are happening more frequently and often involve legacy parts that are no longer being manufactured. As anyone who’s worked in manufacturing well knows, unplanned downtime is expensive, especially when the necessary replacement components aren’t easy to procure.
The report goes so far as stating that “Procurement and/or manufacturing of large metal components, which are essential to the hydropower industry, are currently impossible in the United States, and reliance on international suppliers places the fleet at risk.”
That’s a tough pill to swallow, made all the more bitter by the proportion of renewable energy accounted for by hydroelectric power. Fortunately, advanced manufacturing technologies, such as additive manufacturing, can help modernize the hydropower industry and overcome its pressing difficulties.
3D-Printed Parts and Tooling
The obvious solution to unavailable replacement parts is to manufacture them yourself. However, using traditional methods means having a dedicated facility housing numerous machine tools and other production equipment. 3D printing offers a way to consolidate multiple fabrication and machining operations into a single step. The ORNL report identifies a number of potential use cases for 3D printing replacement parts for hydropower from metal—including magnetic materials—as well as polymer composites.
In one such case, a corroded log-boom anchor for the Nimbus Dam near Folsom, California was redesigned so it could be additively manufactured on a Concept Laser machine. Engineers reduced the number of aluminum parts from three to one and reduced the total mass by 50%. What’s more, the cost of the part dropped by almost 150%, from $1,800 for one to $1,570 for six.
Aside from direct fabrication of parts, metal additive manufacturing can also be used for tooling, including stamping dies for sheet metal, die-casting molds, injection molds and compression molds. In another case study, ORNL 3D printed and finished machined patterns of hydrofoils and spokes for use in a sand-casting process. The result of this pilot study was an estimated 78% cost savings compared to previous builds that used subtractive manufacturing alone.
Hybrid Manufacturing
The combination of additive and subtractive manufacturing—also known as hybrid manufacturing—brings both additive and subtractive processes together in a single machine. Since additively manufactured parts can require additional finishing to improve surface quality or obtain more accurate geometric tolerances, hybrid manufacturing can save considerable time by eliminating the need to transfer and reorient parts between stations.
The ORNL report also notes that alternating between additive and subtractive processes over the course of a build allows for the machining of areas of a part that are inaccessible once the printing process is complete. One promising application of this technology to hydroelectric power is manufacturing turbine runners, which normally require welding as well as long-reach machining tools.
The figure above shows how alternating between additive and subtractive processes in each step of the build streamlines production of a test part made from 1.4404 stainless steel using a combination of direct energy deposition and conventional milling. The first milling operation at step (b) eliminates the need for the cutting tool to reach all the way to the bottom of the part in step (d) after the second additive operation at step (c).
Read the rest of this story at ENGINEERING.com