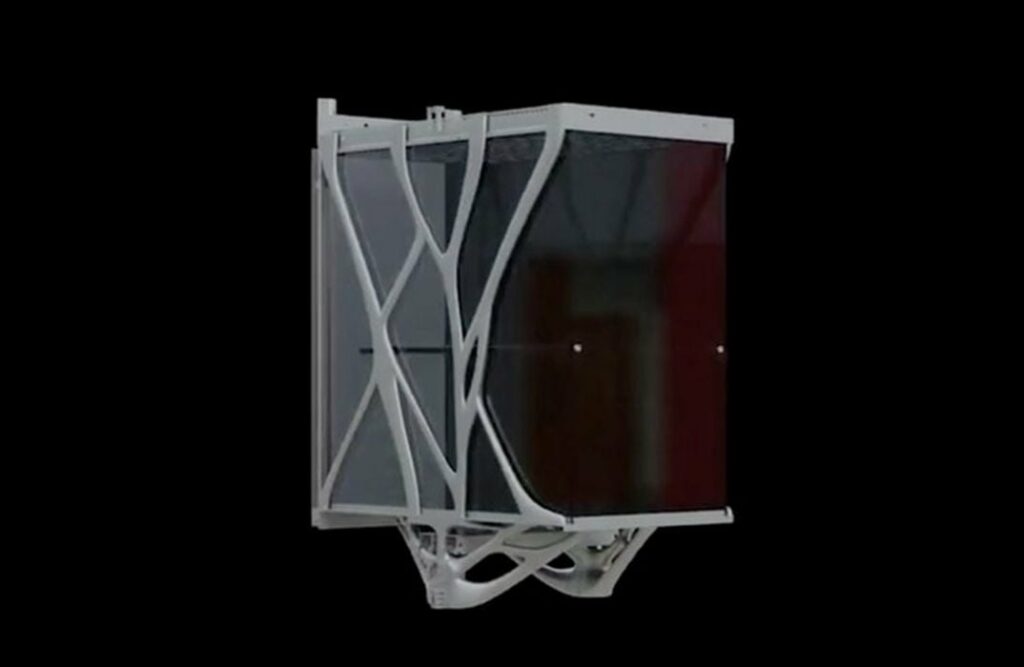
Charles R. Goulding and Ryan Donley look at how several major elevator providers use 3D printing technology.
The elevator industry is a rapidly evolving and growing market. The expansion of modern cities and safety initiatives has accelerated the growth rate of the major players (known as the Big 5) including Otis, Schindler, ThyssenKrupp (TK Elevator), Kone, and Fujitec. The emergence of numerous smaller companies in the industry has also contributed to the market growth as the need for modernization, repair, service, and manufacturing increases for elevators worldwide.
The elevator industry presents tremendous opportunities for 3D printing components including, replacement and spare parts, brackets, shims, installation attachments, and now even cab designs. The key elevator companies are all experimenting with 3D printing to some degree to continually innovate and compete in the market.
Schindler
Swiss elevator company Schindler is one of the world’s leading manufacturers of elevators, their products transport 1.5 billion people every day. Recently, Schindler partnered with MX3D to experiment with metal 3D printing in elevator cabs. MX3D is a 3D printing manufacturing solutions provider from the Netherlands known for its ability to 3D print large objects using metal.
MX3D in conjunction with ArcelorMittal, ABB, Air Liquide & Oerlikon, and Plymovent constructed a unique fully functional 3D printed metal bridge to cross the oldest canals in the center of Amsterdam by leveraging collaborative digital production tools like Autodesk to showcase the full potential of multi-axis robotic metal 3D printing technology. Leveraging additive manufacturing is helping Schindler realize the potential in the technology as the materials are lighter, easier to work with, and inexpensive compared to traditional manufacturing methods.
Otis
Otis is an American company that develops and manufactures elevators, escalators, moving walkways, and similar equipment headquartered in Farmington, Connecticut. Otis is one of the oldest standing companies competing in the market. The company has invested significantly in 3D printing technology and employs 3D printing that is leveraged for product development and rapid prototyping.
Otis utilizes 3D printing together with digital manufacturing to maintain its robust IoT strategies. Otis has expended numerous resources towards industry 4.0 and is innovating upon big data analytics integration to further modernize its operations. Above is a table for Otis’ R&D expenditures per capita.
TK Elevator
TK Elevator, which now operates independently after a sale by former parent Thyssenkrupp AG in 2020, is one of the world’s leading elevator companies headquartered in Germany. The new North American company headquarters in Atlanta, Georgia opened in 2022 and is a complex of three buildings including a state-of-the-art Innovation and Qualification Center that now houses North America’s tallest elevator test tower (420 feet). In addition to the new state-of-the-art facilities, TK Elevator has been leveraging its high-tech 3D printing center to produce plastic and metal components for its products.
KONE Corporation
KONE is one of the world’s top-ranked elevator and escalator manufacturers headquartered in Finland. KONE has been one of the earliest adopters of additive manufacturing presenting a case study for 3D mechanical design in the industry. The company’s shift to more digital innovation has kept them ahead of the curve as utilizing just-in-time 3D printing processes has allowed KONE to produce spare parts quickly without the woes of supply chain issues and prohibitive manufacturing costs.
The Research & Development Tax Credit
The now permanent Research and Development (R&D) Tax Credit is available for companies developing new or improved products, processes and/or software.
3D printing can help boost a company’s R&D Tax Credits. Wages for technical employees creating, testing, and revising 3D printed prototypes can be included as a percentage of eligible time spent for the R&D Tax Credit. Similarly, when used as a method of improving a process, time spent integrating 3D printing hardware and software counts as an eligible activity. Lastly, when used for modeling and preproduction, the costs of filaments consumed during the development process may also be recovered.
Whether it is used for creating and testing prototypes or for final production, 3D printing is a great indicator that R&D Credit eligible activities are taking place. Companies implementing this technology at any point should consider taking advantage of R&D Tax Credits.
Conclusion
The elevator industry is one of the largest expanding markets worldwide. The rapid growth of the sector has enabled the industry to innovate its products, processes, and services through additive