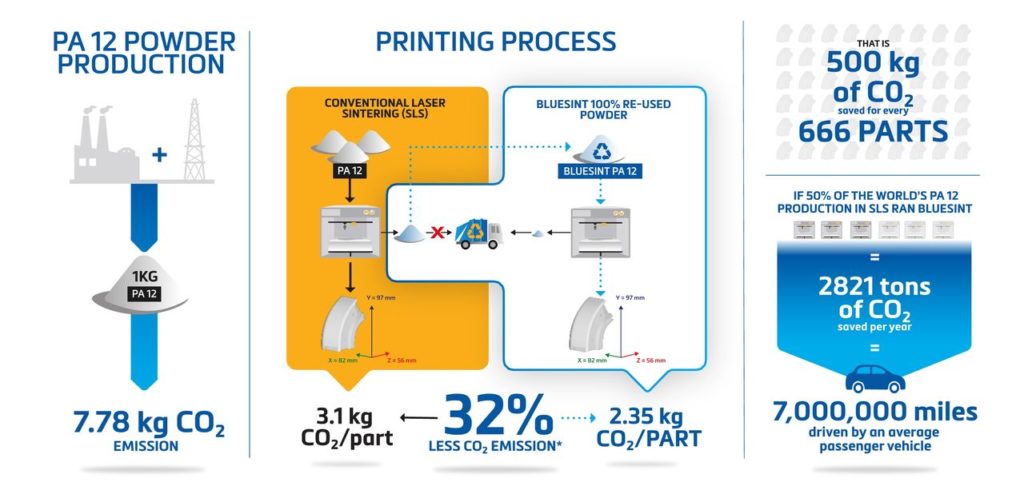
Materialise announced the broad availability of their 100% reusable powder 3D printing service, Bluesint PA12.
The company announced Bluesint PA 12 last fall, but up until now it’s been used only on friendly beta testers. Now the company is making the service available to all clients.
What is the big deal here? It’s all about reusability.
Normally SLS 3D printing has a big problem when reusing powder. In a typical SLS 3D print job most of the powder is unused: it’s not struck by the laser and, in theory, should be reusable in future jobs.
But it turns out that’s not really feasible due to something called the “orange peel effect”. Essentially what happens is the reused powder tends to shrink after the first job. This results in poor surface quality.
The normal approach to overcome this effect is to mix in some ratio of fresh powder with the reused powder. Typically the ratio is 50-50, or in some cases as high as 80% reused and only 20% fresh. This ratio depends on the equipment and materials being used.
While that makes the 3D printing work, it’s absolutely terrible for sustainability. Even though you do reuse some powder, quite a bit cannot be reused due to the ratios required. This means SLS 3D print operations typically have a giant pile of waste powder that must be disposed of properly.
Even worse, that waste powder consumed energy and generated CO2. According to Materialise, the production of each kilogram of powder creates seven kilograms of CO2 that’s emitted into our atmosphere. In other words, when you see a mountain of waste SLS powder, multiply it by seven and — you get the idea.
Materialise’s Bluesint PA12 service solves this dilemma with an ingenious solution. They have the SLS 3D printer’s laser solidifying powder as usual, but also use a secondary laser to slightly heat the surrounding powder above the shrinking threshold, thus eliminating the problem.
Materialise said the resulting 3D prints are just as good as normal 3D prints made with fresh powder, and while the surface quality may have a slightly rougher finish, but they are fully functional.
Bluesint PA12 isn’t a powder you can order and use in your SLS 3D printer; instead Materialise offers it as a service. That’s because it’s more than just the powder: successful Bluesint PA12 printing involves the hardware and slicing software in a coordinated manner.
Materialise clients can now order parts using this new service, and they can know they are definitely saving energy and CO2 when doing so.
Materialise provided an example project where a 122g part project was analyzed. Using standard PA 12 powder, the SLS job product 3.1kg of CO2. Meanwhile, the equivalent part made using the Bluesint PA12 process produced only 2.35kg.
Materialise said if 50% of the world’s SLS activity was done using Bluesint PA12, 2821 tonnes of CO2 would not be generated each year.
3D printing can be an energy-intensive activity, yet we live in a world where sustainability is becoming increasingly critical. It’s thus vitally important for 3D print companies to take steps to mitigate energy use and CO2 generation.
Materialise has made a big step here, and I’m looking for other 3D printing companies to provide similar benefits.
Via Materialise