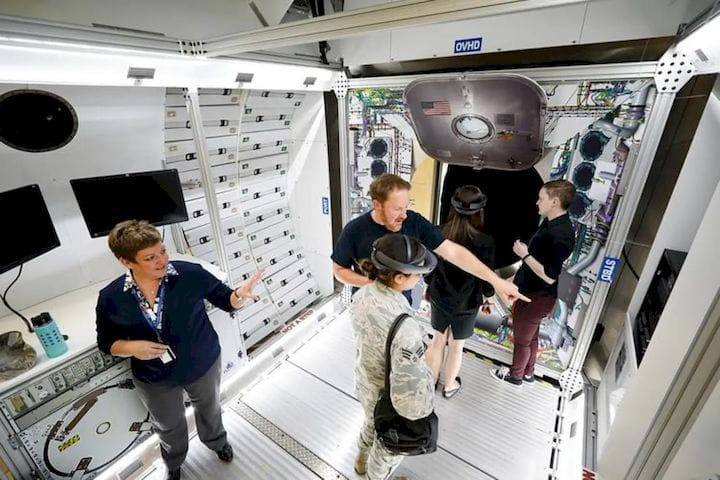
Lockheed Martin is famous for engineering innovation, dating back to the legendary Skunkworks.
Today, the defense contractor is making use of innovative augmented reality technology in their manufacturing process and across entire product lifecycles. Lockheed Martin’s AR project began in the Space Systems division, for example in assembly and quality processes for NASA’s Orion Spacecraft, but has been so successful that the company has deployed the Microsoft Hololens hardware and Scope AR software in other divisions, namely Aeronautics, Missiles and Fire Control, and Rotary and Mission Systems. The company may even send Hololens to space on crewed missions to support training and maintenance tasks.
To find out more about what Lockheed Martin is doing with AR, engineering.com spoke to Shelley Peterson, Principal Investigator for Augmented and Mixed Reality for Lockheed Martin Space Systems, and Scott Montgomerie, co-founder and CEO of Scope AR, the AR software Lockheed Martin is using. Check out our conversation below.
Why did Lockheed Martin start using augmented reality?
SP: The way that our spacecraft are built involves drawings, models, and lots of data that has to be interpreted. For space, we’re often building a small number of spacecrafts. We have programs that have higher volumes, but in many cases, we’re interpreting data in almost every build. And that interpretation takes time. When you can place data spatially, there’s just a significant advantage. It removes so much of the interpretation. We’ve seen in the past that it takes about 50% of the time to go through all of that data and to make sure, and work with peers to make sure the action that’s about to be taken is the correct one.
Of course, when building spacecraft, we need to be very cautious during the actions that we’re taking in the manufacturing process. With 50% of the time being spent just on interpreting the data, our leadership gave it a name—information overhead—and we set a goal to optimize it.
What sort of data are we talking about here? Assembly instructions?
SP: It spans across assembly, the manufacturing process and to assembly launch and test operations, as well as use cases in maintenance and sustainment. We felt that manufacturing was a great place to start because it’s kind of an easy place to measure. We can calculate how much time is being saved, and the other benefits of the technology.
What type of personnel wears and uses the AR in their jobs?
SP: It’s the technician on the shop floor along with the quality engineers who support them. And then these technicians and engineers work with us to build the AR content. They provide us information and feedback on what content needs to be built, and in some cases they also build the content.
For example, for position alignment. When we have any objects that have to be placed with 0.5” tolerance, such as fasteners, strain gauges, transducers, heaters or misters, accelerometers, for example, or hook-and-loop fasteners (There’s a lot of Velcro and tape on spacecraft!) Just for fasteners, we’re seeing about a $38 savings in touch labor per fastener. Lockheed purchases over 2 million fasteners per year, to put that in context. I think that capability applies to all of those other components that I just mentioned.
We’ve also seen drilling and torque applications. We’re working on activity right now which is the start-to-finish work instruction for the Orion crew seat module, to build up the crew seat from start to finish just with AR. So, we started off with shop aids that supplement pre-existing resources, and we’re still doing that, but we’re also adding in a work instruction that is really a start-to-finish assembly process.
There’s an old saying, “There’s no repair shop in space”. Quality is obviously important in this industry. What can you tell me about how AR is used in quality and inspection?
SP: When the quality department is looking to verify component placement in assembly, AR is a very quick and easy way to do that and also when they verify the work instruction in advance, it’s much quicker to do that through AR than to try to verify from traditional methods. Many of the support organizations for the manufacturing process are benefiting as well.
I imagine that it doesn’t require much, if any, training for the operators to interpret the content. Is that right?
SP: That’s correct, yes. Because it’s spatially referenced in the environment, they’re often seeing exactly what they expect. It’s just in a much more easily accessible format.
Read more at ENGINEERING.com