![Impossible Objects Founder and Chairman Bob Swartz [Image: Fabbaloo]](https://fabbaloo.com/wp-content/uploads/2020/05/ImpossibleObjects1a_img_5eb096206949c.jpg)
Impossible Objects has been busy with growing interest in its composite based additive manufacturing (CBAM) process.
When I caught up with company Founder and Chairman Bob Swartz the last day of this year’s RAPID + TCT, he was ready to begin recovery from a very busy May. Describing the event as “a good show — very busy,” he took the time to introduce me to Impossible Objects’ new 3D printing system.
CBAM-2
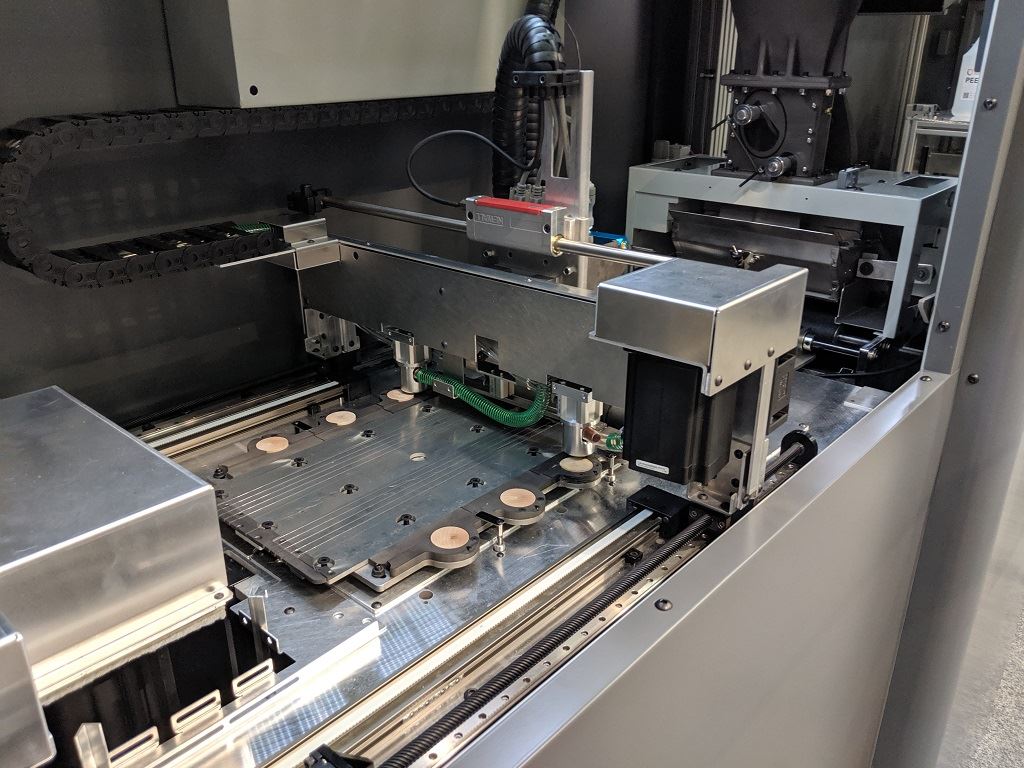
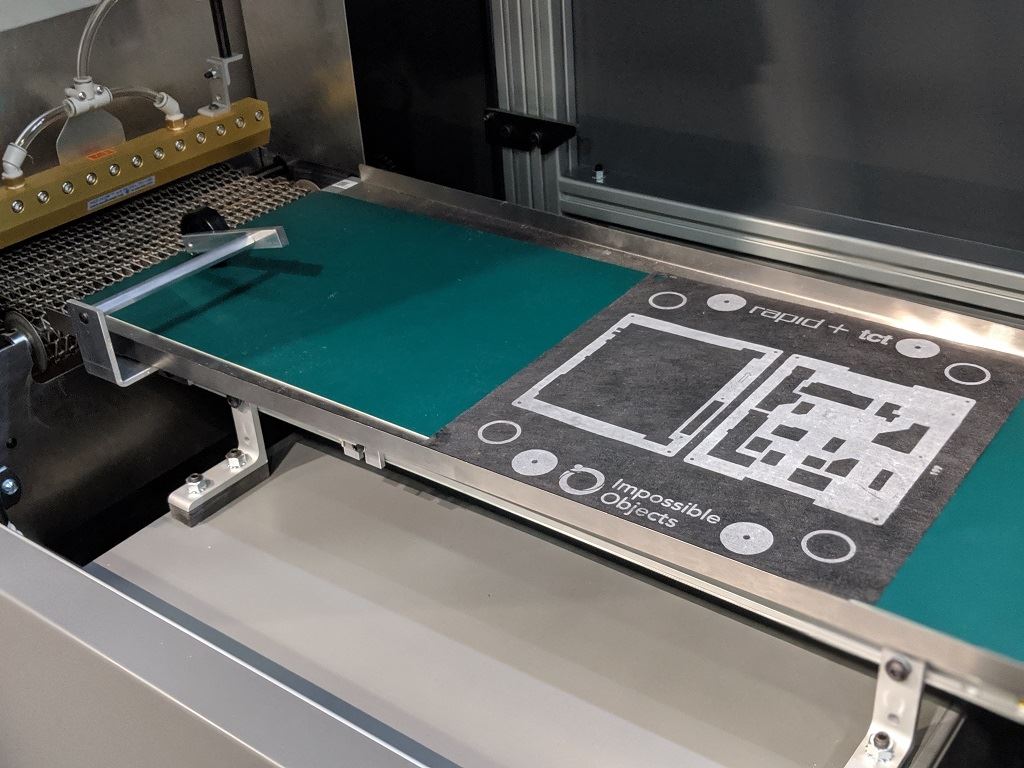
Looking inside the CBAM-2 [Images: Fabbaloo]
The CBAM-2 offers, Swartz noted, a larger build area as well as improvements in reliability, the camera system, and the industrial design from its predecessor, the Model One, introduced two years previously.
The Model One has attracted a good amount of attention, a point that should help the next-generation system. Impossible Objects notes users of its CBAM technology including Ford, Jabil, the US Air Force, and National Institute for Aviation Research (NIAR).
The new system was designed for production — and the necessary speed. Impossible Objects says the CBAM-2 “can produce high volumes of production parts quickly — up to 10x faster than conventional 3D printing.” Those parts are also able to be quite strong, made from composite materials that combine, for example, carbon fiber and fiberglass with PEEK and Nylon.
The larger build volume that Swartz indicated is pretty large indeed, with the sheet system working with sheets up to 12” x 12”. Three added cameras take stock of each print job, with in-process quality control monitoring the sheets and inkjet nozzles.
Longer-duration operation is also a consideration, as the CBAM-2 features automatic powder filling, which “reduces fill-time to days,” as well as bulk ink cartridges to cut down on ink refills.
“It will be shipping in Q3,” Swartz said.
BASF Partnership
![Impossible Objects’ material range is set to expand [Image: Fabbaloo]](https://fabbaloo.com/wp-content/uploads/2020/05/ImpossibleObjects3a_img_5eb09621cae13.jpg)
Impossible Objects has announced a partnership with BASF for Ultrasint PA6, “a much better polymer than PA12,” as Swartz told me.
The collaboration allows users of both the Model One and the CBAM-2 to use Ultrasint PA6.
“PA6 is substantially cheaper [than PA12], and is more used in automotive applications. It has better heat and mechanical properties,” Swartz said.
The ability to 3D print carbon fiber-PA6 composite parts is certainly intriguing. The company further compares the material with other familiar offerings, noting that carbon fiber-PA6 composites “are up to four times stronger than conventional Fused Deposition Modeling (FDM) parts and twice as strong as Multi Jet Fusion (MJF) parts made with PA12.”
The new material offering will, along with the CBAM-2, be available in Q3.
$4.1 Million
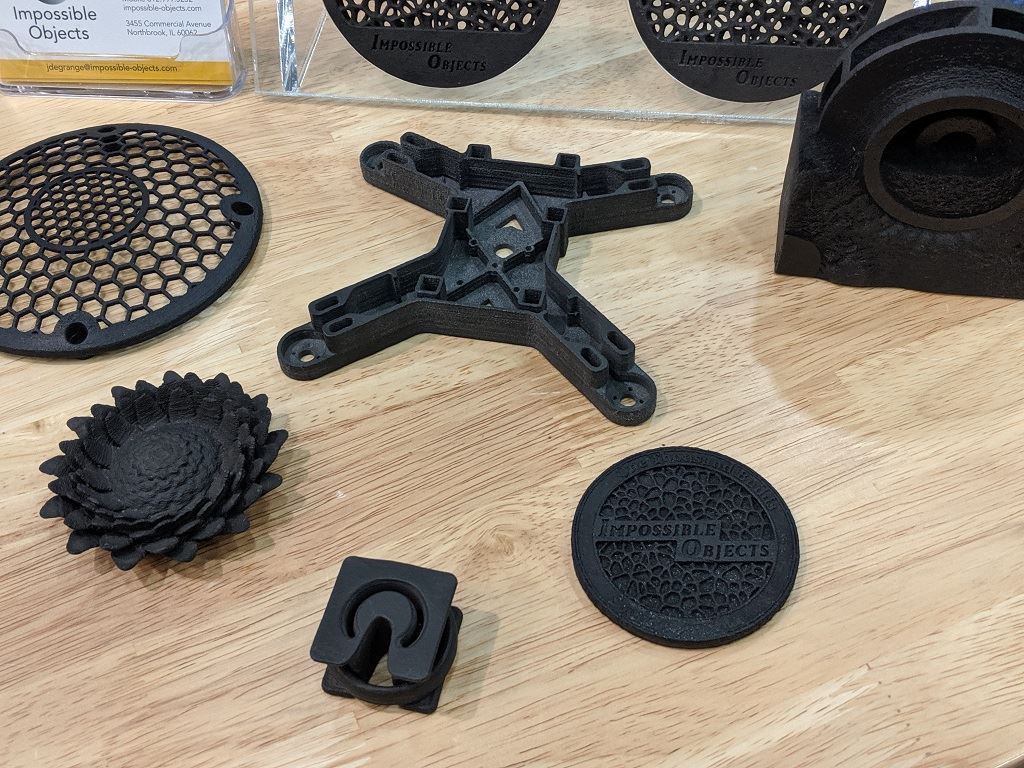
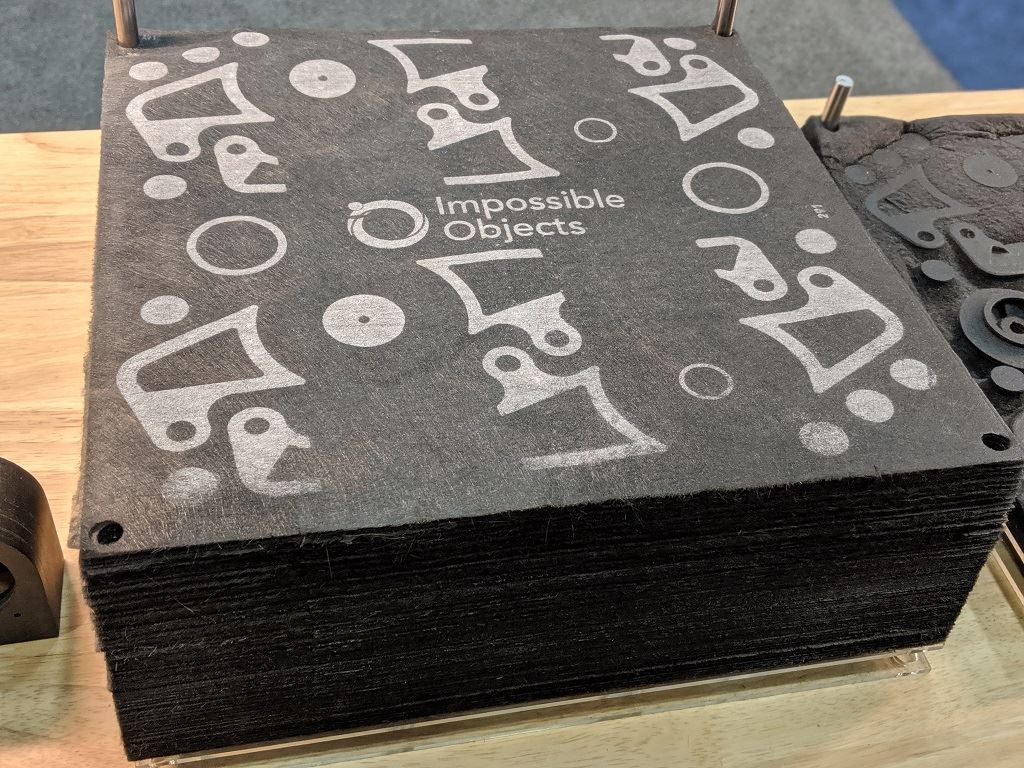
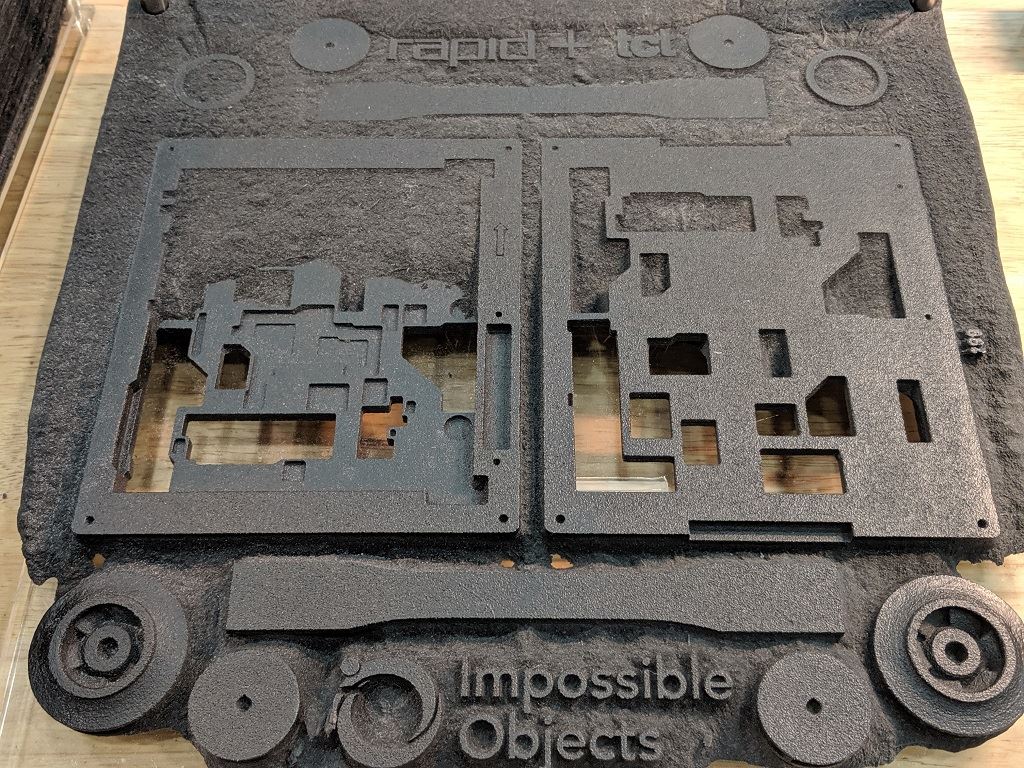
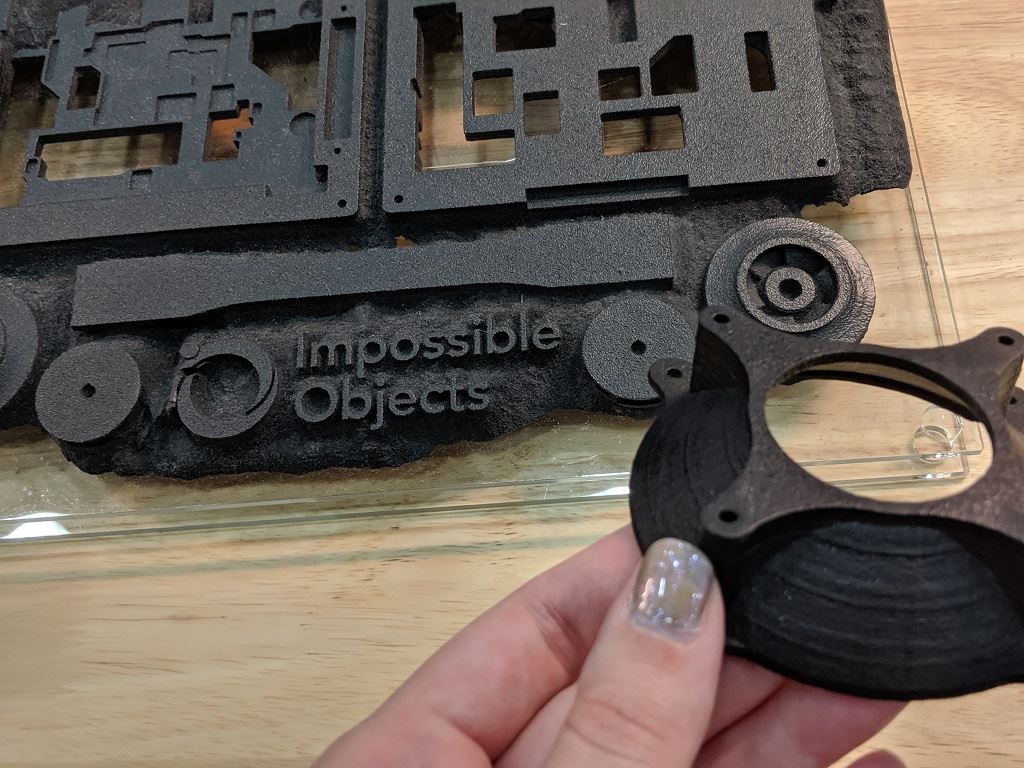
Impossible Objects prints [Images: Fabbaloo]
It’s not the first multi-million funding announcement from Impossible Objects, following a $2.8M round in 2014 and $6.4M Series A in 2017. And it probably won’t be the last.
This time, Impossible Objects announced a $4.1 million funding round led by OCA Ventures, which is a returning investor. For those keeping count at home, that brings funding above the $13 million mark.
With a new machine, materials partner, and funding, as well as increasing interest in parts and machines, things are in fact looking more possible than ever for Impossible Objects.
A manufacturing-as-a-service company has developed a way to 3D print continuous carbon fiber in a production setting.