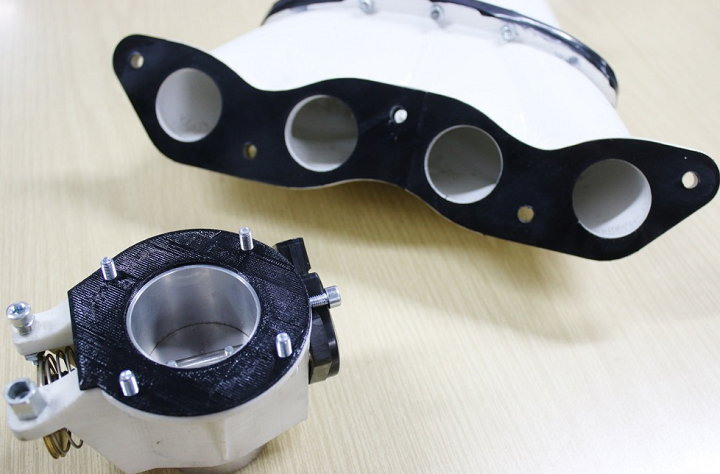
Charles R. Goulding and Preeti Sulibhavi discuss gaskets, 3D printing, and functionality.
Gaskets Play a Significant Role in Our Everyday Lives
If you require a gadget to prevent water, air or gas from escaping when two mating surfaces are joined under compression, gaskets are your answer. The varied configurations, functions, and applications of gaskets means that choosing the right gasket for the selected purpose is critical. If you’ve ever used a pressure cooker to make dinner, and your pressure cooker did not explode, you have your gasket to thank for your dinner as well as your safety.
Gaskets actually fill irregularities for “less-than-perfect” mating surfaces on machine parts. Common varieties of gaskets include:
-
Rubber Gaskets
-
Non-Asbestos Gaskets
-
Cork Gaskets
-
Spiral Wound Gaskets
-
Teflon Gaskets
Gaskets can be used in piping and vehicles, and more: gaskets with certain material properties can be used for particular functions (e.g., rubber or cork can be used for pressure, temperature, or chemical resistance). Essentially, a gasket is a flexible substance that sits between two other surfaces. Typically made from soft materials (e.g., rubber), one of the more common uses is sealing (preventing liquids from leaking from pipes).
Spiral wound gaskets, made by winding a metal strip such as stainless steel and softer filler, like graphite or PTFE, offer lower clamping forces, but are a more expensive method of sealing. Transformer gaskets are used to seal the oil and water tanks to prevent leakage, or used as weather seals to increase the ingress protection (IP) rating of the compartments. They are also used to ensure that the transformer enclosures remain accessible.
Inner bolt circle (IBC) gaskets are also referred to as ring type or raised face gaskets. A continuous ring of material, IBC gaskets sit within the circle of bolts and secure the joint. To meet the detailed specifications and requirements of these critical gadgets, 3D printing is the perfect option for creating gasket prototypes and end products.
In the process of improving and innovating gasket technology, companies can benefit from R&D tax credit incentives because the development of new products often require a process of experimentation and the consideration of alternatives. An example of this credit eligible activity would be material selection during the development of a custom gasket, wherein several materials are evaluated and tested before the optimal material for the given application is selected. Materials consumed during this process can be reclaimed in the final credit amount.
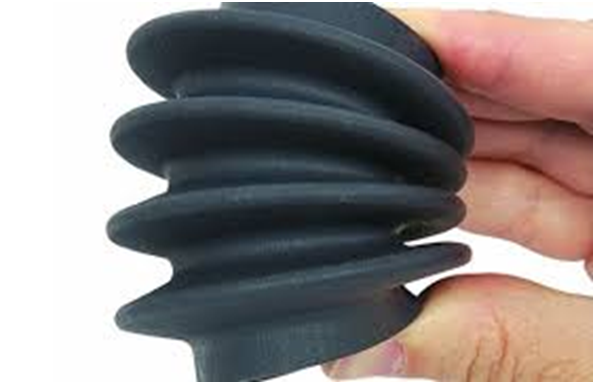
Gaskets and 3D Printing: Joining Two Different Items for the Perfect Function
Gaskets play a discreet yet vital role in many aspects of our daily, modern lives. Although the uses of gaskets can vary, the use of the appropriate gasket for a particular application cannot. By utilizing 3D printing, manufacturers can create an array of different gasket dimensions to achieve a product that is intricate and durable. Whether it is 3D printing a prototype of a new gasket for a garbage disposal, or designing a custom 3D printed gasket using silicone, 3D printing is a viable and economical option for creating gaskets. Companies that are using 3D printing to iterate and test products or components such as gaskets can benefit from R&D tax credits, which are available to support further innovation in the industry.
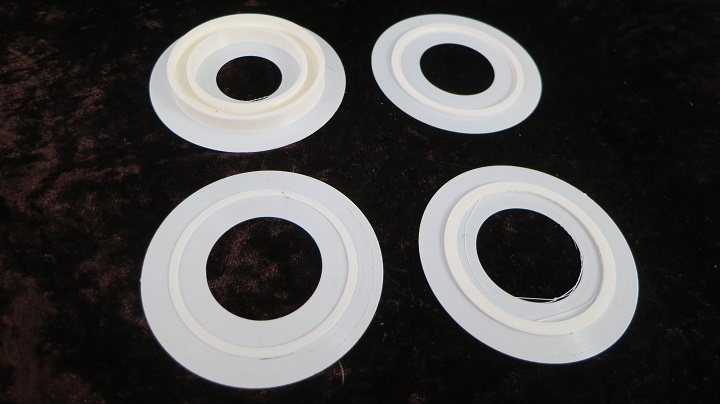
The Research & Development Tax Credit
Enacted in 1981, the now permanent Federal Research and Development (R&D) Tax Credit allows a credit that typically ranges from 4%-7% of eligible spending for new and improved products and processes. Qualified research must meet the following four criteria:
-
Must be technological in nature
-
Must be a component of the taxpayer’s business
-
Must represent R&D in the experimental sense and generally includes all such costs related to the development or improvement of a product or process
-
Must eliminate uncertainty through a process of experimentation that considers one or more alternatives
Eligible costs include US employee wages, cost of supplies consumed in the R&D process, cost of pre-production testing, US contract research expenses, and certain costs associated with developing a patent.
On December 18, 2015, President Obama signed the PATH Act, making the R&D Tax Credit permanent. Beginning in 2016, the R&D credit can be used to offset Alternative Minimum tax for companies with revenue below $50MM and, startup businesses can obtain up to $250,000 per year in payroll tax cash rebates.