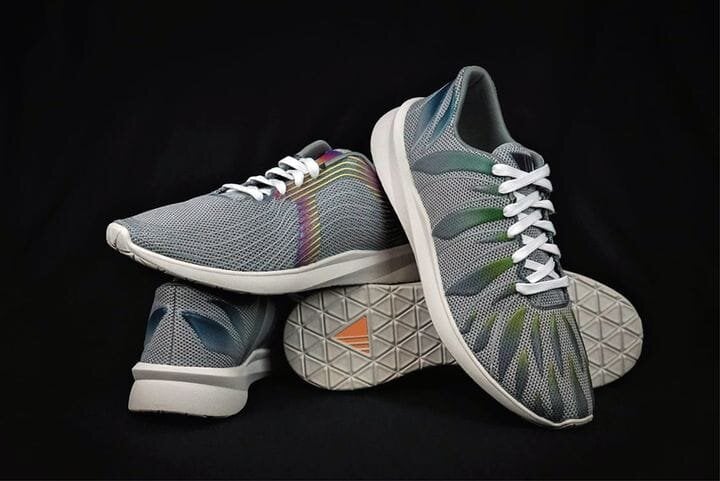
In 2015, a startup called Voxel8 wowed attendees at CES in Las Vegas with a desktop 3D printer capable of 3D printing electronic circuits into thermoplastic parts.
The firm demoed its Developer’s Kit system by fabricating a quadcopter live at CES and flying it directly off of the print bed.
Though Voxel8 continued to make announcements, mostly related to the sales of its Developer’s Kit 3D printer, for some time after that, it soon went radio silent. We did catch a brief discussion by the company at AMUG in 2017, but it wasn’t until just this past October that it made its first big announcement in years: Voxel8 has created a system for 3D printing shoe uppers.
To help the company along in its development of a machine capable of 3D printing 350,000 pairs of shoe uppers per year, DSM Venturing, along with the venture arm of HP Inc., have invested in Voxel8. To learn more, we spoke to Voxel8 CEO and co-founder Travis Busbee.
3D Printing Shoes
3D printing footwear components or even complete shoes has been an active area for some time, with New Balance working to additively manufacture midsoles years ago. Now, nearly every major athletic shoe brand is working to 3D print midsoles, including Adidas with Carbon, New Balance with Formlabs and 3D Systems, Under Armour, and Nike. Insoles, too, have become an area of active interest, with both startups like Wiivv and giants like HP participating.
What has been more difficult, however, is 3D printing the actual uppers of shoes, where all of the aesthetic appeal is and the bit that actually makes the shoe wearable. A startup called Feetz once tried to tackle this terrain using fused deposition modeling-style 3D printing, but it seems to have gone defunct in late 2018.
Busbee thinks his company can succeed where others have been unable to.
“These footwear brands are really looking for an automated digital supply chain to allow them to get their products to market much more quickly and to do so without extravagant tooling costs,” he said. “That way, they can introduce small batches of products to market, analyze the demand and then respond to it in real time. Ultimately, in order to get there, they have to have a solution for both the top and the bottom of the shoe. Currently, they only have a digital solution for the bottom, but no one has come up with a solution for the top until we came around and created this solution specifically tailored to address the top portion of the shoe.”
The Active Lab Digital Fabrication System
Currently, shoe uppers are made using a labor- and material-intensive process that includes die cutting, tooling, stitching, finishing, gluing and assembling components. Voxel8 has developed a method for automating and streamlining the fabrication of uppers via 3D printing.
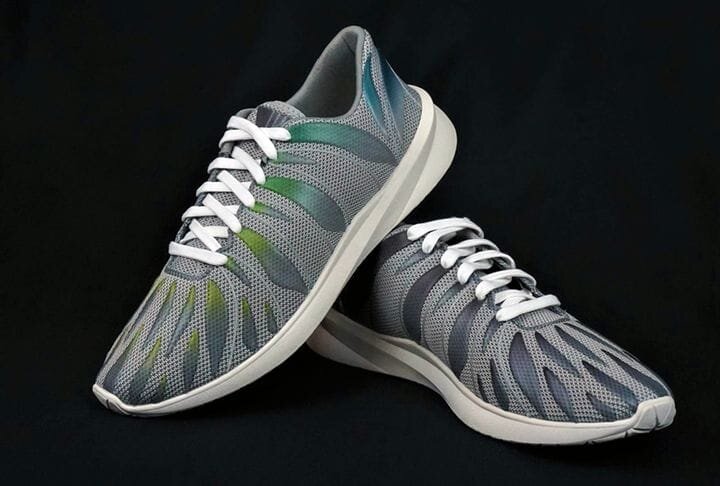
“If you just took a piece of textile and sewed it into the shape of a shoe, you wouldn’t have enough structure to really have the shoe stand up and look good and keep your foot centered on the cushioning elements of the shoe. You wouldn’t have any logos or text or branding,” Busbee said. “Ultimately, the things that go on top of that textile create the structure that give the shoe its functional performance and also create the design language and style or at least play a huge role in it.All of those components that go on top of the shoe are the parts that are the most difficult to make.”
Using a multi-input active mixing printhead, Voxel8’s Active Lab Digital Fabrication Systemis capable of either spraying or extruding liquid polyurethane elastomers onto a textile that then solidify as the elastomer reacts. This gives structure to the otherwise two-dimensional and flimsy fabric, allowing it to become a three-dimensional cloth.
Read more at ENGINEERING.com