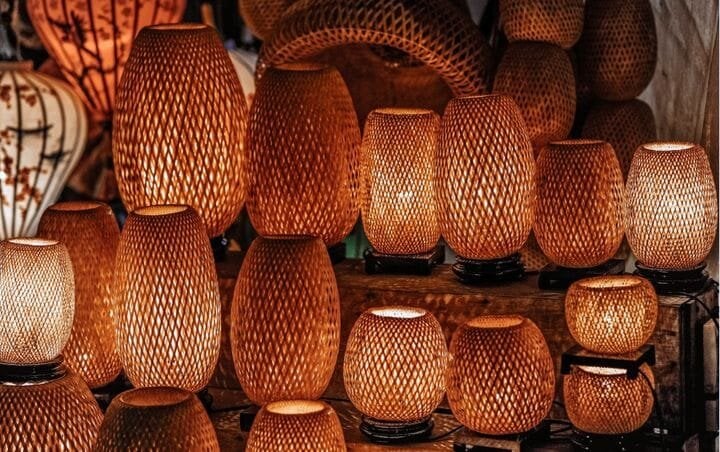
Charles Goulding & Greer Veon of R&D Tax Savers look at the use of natural fibers in 3D print materials.
Global awareness of environmental issues is at an all-time high, and the green movement is leading advancements in every industry. As these industries experience changes, manufacturers and product designers are keener than ever to integrate biodegradable and cost-efficient materials that will be beneficial choices for our planet. Some companies are turning to the 3D printing industry as an eco-conscious answer with the ability to use recycled and natural materials, specifically natural fibers including such unusual natural materials as:
-
Algae
-
Bamboo Wood
-
Jute
-
Coconut
-
Cork
-
Hemp
-
And more
Many of these fibers can be used to enhance the durability and strength of filaments used for the Fused Filament Fabrication (FFF) 3D printing process, and specifically with polylactic acid (PLA) material. Product designers who invest in using PLA filament and 3D printing for models, prototypes, or products should qualify for the R&D tax credit.
The Research & Development Tax Credit
Enacted in 1981, the now permanent Federal Research and Development (R&D) Tax Credit allows a credit that typically ranges from 4%-7% of eligible spending for new and improved products and processes. Qualified research must meet the following four criteria:
-
Must be technological in nature
-
Must be a component of the taxpayers business
-
Must represent R&D in the experimental sense and generally includes all such costs related to the development or improvement of a product or process
-
Must eliminate uncertainty through a process of experimentation that considers one or more alternatives
Eligible costs include U.S. employee wages, cost of supplies consumed in the R&D process, cost of pre-production testing, U.S. contract research expenses, and certain costs associated with developing a patent.
On December 18, 2015, President Obama signed the PATH Act, making the R&D Tax Credit permanent. Beginning in 2016, the R&D credit can be used to offset Alternative Minimum tax for companies with revenue below $50MM and for the first time, pre-profitable and pre-revenue startup businesses can obtain up to $250,000 per year in payroll taxes and cash rebates.
PLA Filament Benefits
![3D printed PLA thimbles [Source: Flickr]](https://fabbaloo.com/wp-content/uploads/2020/05/image-asset_img_5eb08cd5a92dd.jpg)
PLA differs from most thermoplastic polymers because it derives from renewable sources like sugar cane or jute fibers. All thermoplastic materials turn liquid at their melting point of about 150-160C but can be reheated after cooling & solidification to resume their liquid form. The ability to reheat PLA again without significant degradation allows them to be easily injected into a mold and subsequently recycled. Since the material comes from biomass, PLA bioplastics are biodegradable and relativity cost-efficient to produce.
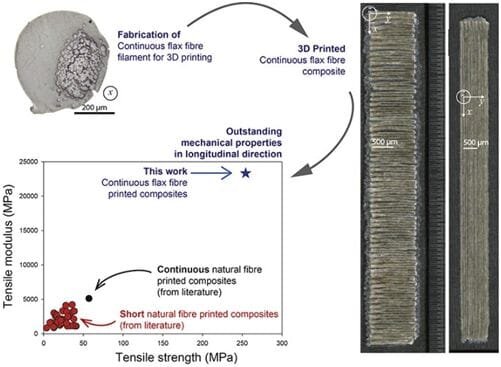
PLA filament is a smart choice in that the material is easy to print due to its relatively low softening temperature and its ability to resist warping during 3D printing. Today there are a wide variety of PLA options available on the market, as it is deliverable in several formats and a myriad of colors. PLA filament is primarily used for 3D printing rapid prototypes, and objects that won’t require exposure to high temperatures, strong mechanical properties or need extreme durability.
Flax Fibers Reinforce Biocomposites
As a way to enhance biocomposite materials in structural applications, researchers at the University of Bretagne in France sought to enhance PLA filament used in FFF-based 3D printing by reinforcing the filler with natural fiber. Though numerous studies have used jute fibers, researchers chose to use flax fibers to create a cFF/PLA filament. Flax fibers hold excellent tensile properties and are easily available with high quality and a range of density.
Researchers found through that by using cFF/PLA filament in a FFF printer, the longitudinal mechanical properties were greater than found with pure PLA filament or other natural fiber-reinforced PLA filament because flax fibers have higher mechanical properties than wood or hemp fibers.
Compared to 3D printed structural composites made with glass fibers, cFF/PLA biocomposite material showed similar fiber volume fraction, filament production, and stiffness level.
Recreating Wood Through 3D Printing
Scientists from Sweden’s Chalmers University previously discovered a way to create a 3D printing medium from wood fiber. Now researchers found a new printing method that produces a stronger material with close to the exact qualities of wood. Instead of using the previous nanocellulose gel obtained from wood pulp, researchers added hemicellulose, a natural component of plant cells.
The addition boosted the gel strength to hold together the cellulose fibers within the natural wood print. This development allowed product developers to have precise control of the nanofibers’ alignment. This development could lead to increased 3D printing of items with greater strength and sustainability.
The Way Forward
As the demand for more sustainable material options in the global marketplace grows, natural fiber reinforced filaments could advance the 3D printing industry as a smart, eco-conscious investment.