![[Image: Stratasys]](https://fabbaloo.com/wp-content/uploads/2020/05/Boom3_img_5eb0a527904ce.jpg)
Stratasys looks toward a future in production, building upon its unique history with 3D printing.
When I caught up with the company’s Vice President of Manufacturing last month, Scott Sevcik shared a look at Stratasys’ strategies surrounding carbon fiber. At IMTS a few weeks ago, that carbon fiber capability was on display alongside myriad other solutions for prototyping and, increasingly, production applications. This week, I spoke with Sevcik again to gain perspective on the bigger picture for Stratasys, as this is increasingly summed up with one key word for strategy: manufacturing.
Before looking forward, though, we took a step back to discuss how we — how 3D printing — got here.
“Stratasys has been around for 30 years, and prototyping has been the focus of that core history for much of 3D printing. With FDM and the ability to print a range of thermoplastic materials, we had interest in tooling earlier than other technologies did. This began in aerospace first, then automotive and more general manufacturing, all dating back probably on the order of 10 years or more at this point,” Sevcik said.
“In the 2000s, companies were realizing they could do more with these materials with Stratasys’ FDM capabilities. Customers had mostly been going it alone. Stratasys recognized this, and a focus for us is on close relationships with customers. As we became more aware of this push, and how customers are using this technology, we started to evolve.”
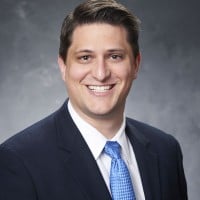
It was through this evolution that Sevcik himself came to join the team at Stratasys, as the push for the company expanded to bringing in people who were part of these industries. This, he explained, was “so we could have better conversations with these customers and better understand their language.”
The Stratasys Direct Digital Manufacturing (DDM) Group was an important part of this shift, helping to pave the way in developing products to better suit customers’ actual needs.
“We had customers going very deep with FDM technology for tooling a number of years ago, and that extended as we expanded to higher-value materials. Most of this was done very quietly; some has been shared, some we haven’t been able to share, with how often this technology has been used,” he continued.
Most of the production-focused work was focused around ULTEM 9085, a popular engineering-grade material. Airbus in particular, around 2013-2014, began exploring this material and FDM 3D printing more deeply, qualifying these for what they called missing part production. That company saw that these capabilities could provide significant advantages in developing solutions for a number of different needs, Sevcik noted, including production of replacement parts that were no longer available, and affecting design through lighter-weight parts and customization for cabin components.
Airbus, he said, was one of the first major public examples Stratasys could share about their production focus.
Aerospace engineers have seen tooling in particular rise into significance as a 3D printing application. The use of ULTEM on Stratasys’ machines gave rise to an important question for these engineers: “This is a production material; is this a production technology?” This, Sevcik said, led to a “very collaborative effort to make sure they understood the technology and got what they needed out of it to qualify for flight use.”
And admirable as the application may be — and it is, no question about that — it represents a close relationship with a single customer.
Sevcik acknowledges that most of these major production use cases has been representative of a one-off type of application-specific development with a specific customer. Working closely with such customers as Airbus and Team Penske, among others, has led to Stratasys “enhancing production processes around these materials,” ensuring the traceability that aerospace needs and using a certification-grade material to meet these needs. Developing a deep relationship with individual users enables a deep understanding of their real-world manufacturing environment and targeted needs and usage. This understanding can then be taken out and broadened to lead to a more optimized development process for production solutions.
“We dug in and made the most repeatable technology in FDM,” Sevcik said. “We’ve reached levels of repeatability in an additive manufacturing technology that exceeded some in traditional technology. We listened to our customers, listened to those needs, and drove toward production.”
Today’s progress, in reaching qualified material status and seeing industry specs documenting certification, “all came about through early adopters and pushing through to industry,” he added.
Such high-profile — and high-flying — use cases for Stratasys’ thermoplastic production offerings in 3D printing present an interesting picture for areas where additive fits into the manufacturing workflow. In part two of our interview, we touch on additional usage as production 3D printing continues to rise, and how focus shouldn’t be wholly on metals when discussing such topics.
Via Stratasys
A blog post reveals much of what happens behind the scenes at 3D print service Shapeways.