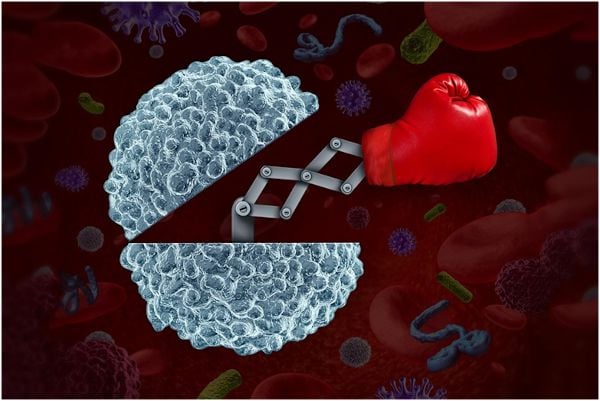
Charles R. Goulding and Preeti Sulibhavi examine how 3D printing could make an even bigger splash during the second wave of COVID-19.
Global COVID-19 infection rates are increasing, and we are now in Round 2 of the fight against the global pandemic. The first round of the COVID fight was a defining moment for the 3D printing industry.
Round 1
3D printed items for fighting COVID-19 included swabs, masks, shields, laboratory equipment, and components for ventilators and respirators. The 3D printing users included companies ordinarily engaged in the same or similar product categories including apparel companies for masks and companies contributing new products for the first time like Ford and General Motors for ventilators. Ramping up to design and produce new products with new processes isn’t easy and the collective results of all the participants have been astounding.
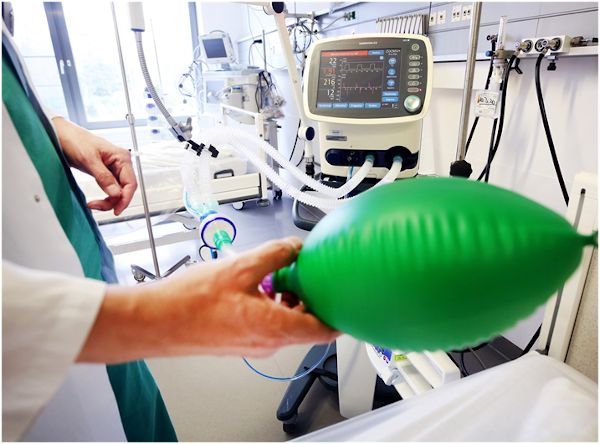
Round 2
Clearly, the recent experiences will enable companies who continue to supply PPE to become much more efficient. What was envisioned as temporary production lines can be re-engineered for optimal speed, quality and yield. This re-engineering can use additional 3D printing for design and production.
In Round 1, purchasing departments at PPE manufacturers had to disregard their standard practices and scramble to source different materials and components from any place they could find them at almost any cost. With the 8 month COVID interval they are now able to apply their normal purchasing pricing prowess and optimize material selection and vendors.
It became obvious to the U.S. government and companies that critical PPE items must be produced in the U.S. and production of these critical items has now in fact been re-shored to the U.S., which is also the world leader in 3D printing. Legacy vendors of PPE products, including ventilators, have witnessed the pinch-hitting emergency and manufacturers use 3D printed components, now fully realizing the benefits of 3D printing.
During the 8 month COVID period the overall rate of manufacturing automation implementation including robots and conveyors has greatly increased, in part due to social distancing requirements. This automation includes more 3D printing, which is an important part of the Industry 4.0 automation process.
In Round 2 we have the emergence of new virus-fighting technologies including UVC lighting, UVC lighting robots, enhanced HVAC air handling and touchless technologies, all of which can benefit from 3D printing.
Federal tax incentives, such as the Research and Development Tax Credit, are available for companies that pursue 3D printing activities.
The Research & Development Tax Credit
Whether it’s used for creating and testing prototypes or for final production, 3D printing is a great indicator that R&D Credit eligible activities are taking place. Companies implementing this technology at any point should consider taking advantage of R&D Tax Credits.
Enacted in 1981, the now permanent Federal Research and Development (R&D) Tax Credit allows a credit that typically ranges from 4%-7% of eligible spending for new and improved products and processes. Qualified research must meet the following four criteria:
- Must be technological in nature
- Must be a component of the taxpayer’s business
- Must represent R&D in the experimental sense and generally includes all such costs related to the development or improvement of a product or process
- Must eliminate uncertainty through a process of experimentation that considers one or more alternatives
Eligible costs include US employee wages, cost of supplies consumed in the R&D process, cost of pre-production testing, US contract research expenses, and certain costs associated with developing a patent.
On December 18, 2015, President Obama signed the PATH Act, making the R&D Tax Credit permanent. Beginning in 2016, the R&D credit has been used to offset Alternative Minimum Tax (AMT) for companies with revenue below $50MM and, startup businesses can obtain up to $250,000 per year in payroll tax cash rebates.
Conclusion
During Round 1 of the COVID-19 pandemic, the 3D printing industry stepped up and demonstrated what it could do. In Round 2, look for an even greater 3D printing industry contribution.