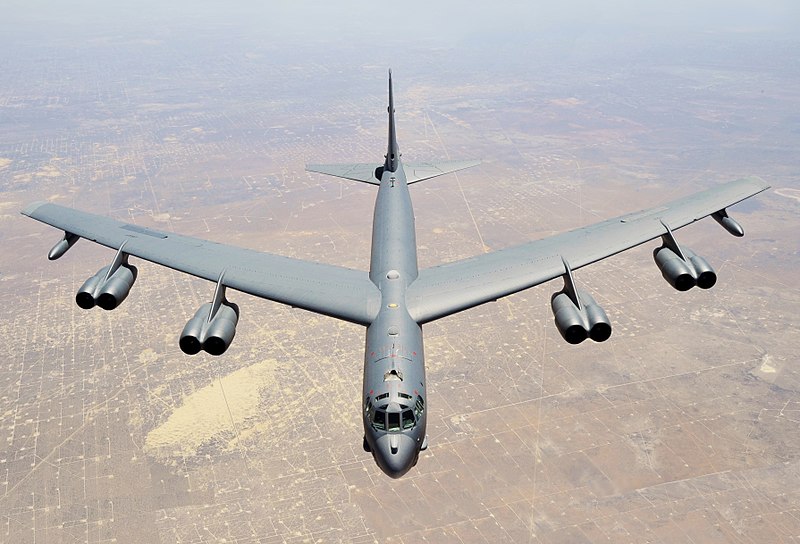
The U.S. Air Force 3D printed a metal engine part to keep the B-52 Bomber in service until new engines are fitted in the late 2020s.
The B-52’s New Component
The Air Force intends to use additive manufacturing technology to incorporate cost-efficient, easily-manufacturable parts to its building process.
As the supply change for the part is running out, U.S. Air Force engineers at the Tinker Air Force Base used 3D printing technology to print an anti-icing gasket for the Pratt & Whitney TF33-P103 turbofan engine of the B-52.
Popular Mechanics noted that the TF33 is the original engine, of which eight were installed on each of the B-52H bomber planes when they were initially produced in the early 1960s. The complex supply chain that produces the parts necessary for these high–maintenance aircrafts ages with planes like the B-52. With passing time, some of these parts will stop being manufactured and some manufacturers will go out of business.
Additive manufacturing has the ability to wave goodbye to such problems of obsolescence. The Air Force in particular has been very invested in turning to this technology, 3D printing everything from latrine covers to repairs for engine turbines.
To build the new ice-gaskets for the TF-33s, engineers reverse-engineered an OEM gasket before printing new ones. The Air Force has 3D printed 30 parts thus far, but will likely need more, as its fleet of B-52s have a combined 608 engines.
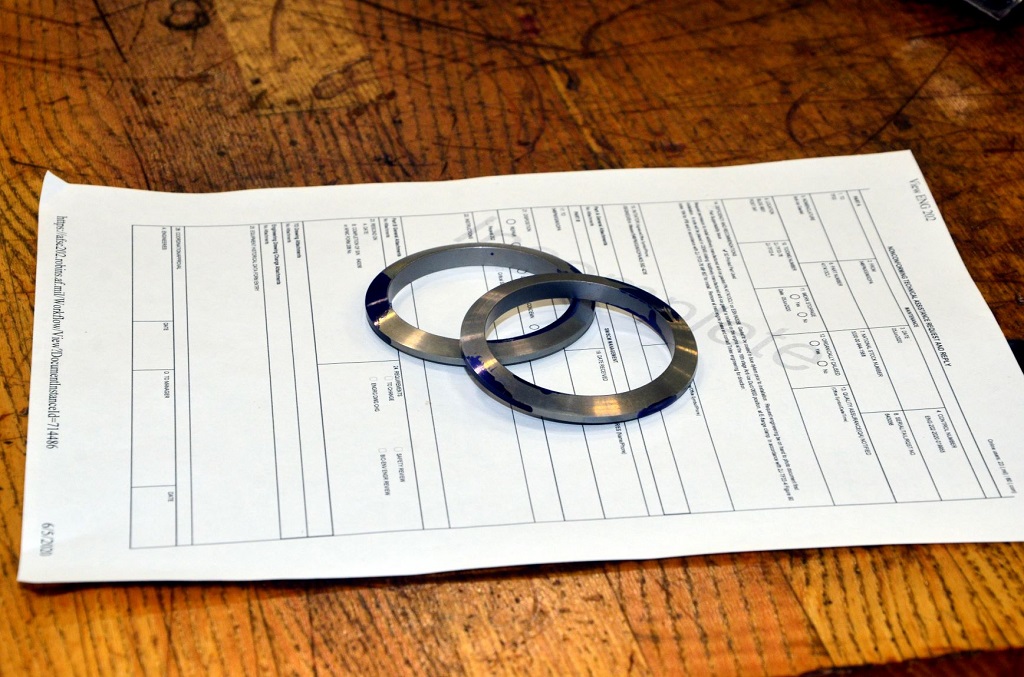
“This accomplishment is truly a historical first. This is a digitally designed and digitally engineered component that represents a substantial milestone in Air Force sustainment. Although it is a basic component, the technology our OC-ALC [Oklahoma City Air Force Life Cycle Management Center] team has developed will help resolve supply chain issues and help bring further capacities to support the warfighter,” said Johnny Tsiao, propulsion structural competency lead for the Air Force Life Cycle Management Center.
“We’ve implemented a crawl, walk and run approach when it comes to additive manufacturing. We haven’t had a 3D-printed metal component in Air Force engines before, but in the next 12-24 months, this technology will open the door to more complex and critical components that help to improve our sustainment efforts moving forward.”
The Verdict
Additive manufacturing is an excellent way to produce outdated and new parts alike faster and for a cheaper cost. Personally, I think that it would be interesting for the Air Force to continue manufacturing parts with additive manufacturing to see how much more efficient the parts on the plane are.
The Air Force also explains that timeliness is greatly improved with 3D printed replacement parts:
“Compared to the original component sourcing method, the new anti-ice gasket manufacturing process reduces administrative lead time —the amount of time between an initial contract and actual component manufacture— from 120-136 days to 14-21 days.”
Even though technologies are constantly evolving, the B-52 has stayed more or less the same since the early 60s. I think it’s safe to say that this fleet most likely won’t be going anywhere soon.
Even if the B-52s are abandoned in favor of a newer technology, it’s likely that 3D printing will be able to play a part in alleviating some of the costs and improving efficiency.
Via U.S. Air Force