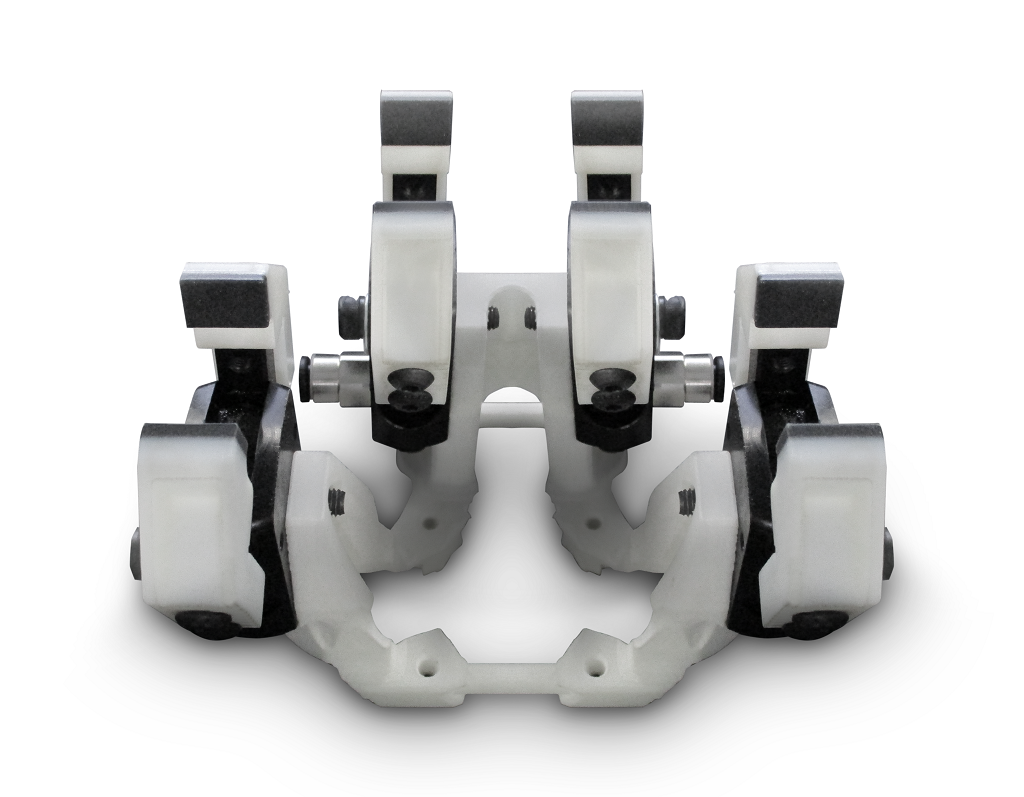
SPONSORED CONTENT
When improving a 3D printed part, sometimes a different 3D printing technology is the best route as contract manufacturer HARBEC recently found.
New York-based HARBEC has been providing contract manufacturing services for more than 40 years — and, for more than half that time, has been including additive manufacturing among its production technologies. The company has developed expertise in metal and plastic 3D printing alongside traditional processes like machining and injection molding. With AS9100 and ISO13485 certifications and as an ITAR-registered company, quality is always at the forefront of the services that HARBEC offers.
HARBEC Manufacturing Robots
Among the daily manufacturing processes at HARBEC’s facility are robots. Increasingly popular in production settings, robots allow for enhanced automation to perform repetitive tasks. To best perform those tasks, robots are outfitted with specific end-of-arm tools.
These end-of-arm tools may include multiple pneumatically powered claws or grippers that attach to a bespoke bracket.
To create those brackets, HARBEC turned to its own in-house 3D printers to ensure the right bracket could be made for each robot. An SLA 3D printed bracket proved a good first effort to make what they needed to keep the robots running: it offered decent mechanical properties and, most importantly, it let the robot work.
But it could be better.
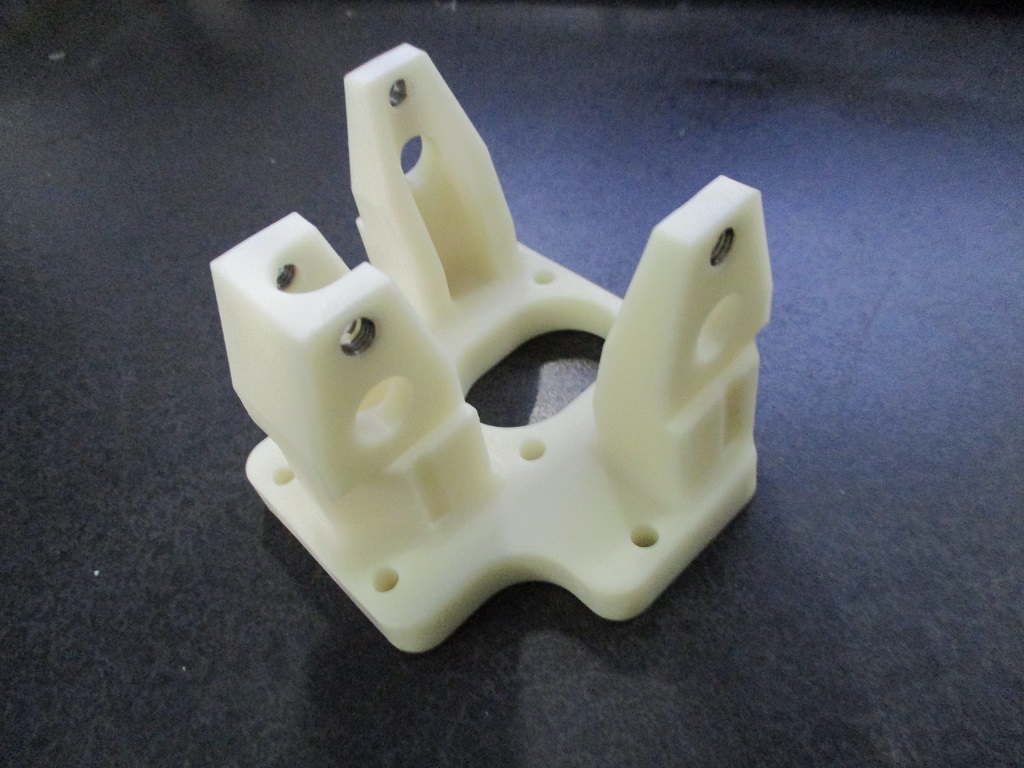
Mass: 100 g
Properties:
UTS = 38 MPa
YM = 1590-1660 MPa
Results: Heavy / Rigid / High Yield Strength
[Source: XYZprinting]
Optimizing Through Design
One of the key benefits of advanced manufacturing capabilities is the ability to lightweight parts. Helpful not only in high-value aerospace applications, lightweighting enables many parts to perform better; less weight can mean higher speeds when it comes to, for example, movements on robotic arms.
So the HARBEC team turned to the expertise they had built up in design for additive manufacturing (DfAM). They created a new topology optimized design for the bracket in SOLIDWORKS, reducing the weight of the robots’ gripper brackets. Not only did they make the brackets lighter, they ensured that the solid areas would respond well to the forces put on the bracket during operation.
Then they 3D printed the bracket again, using the same SLA system initially used.
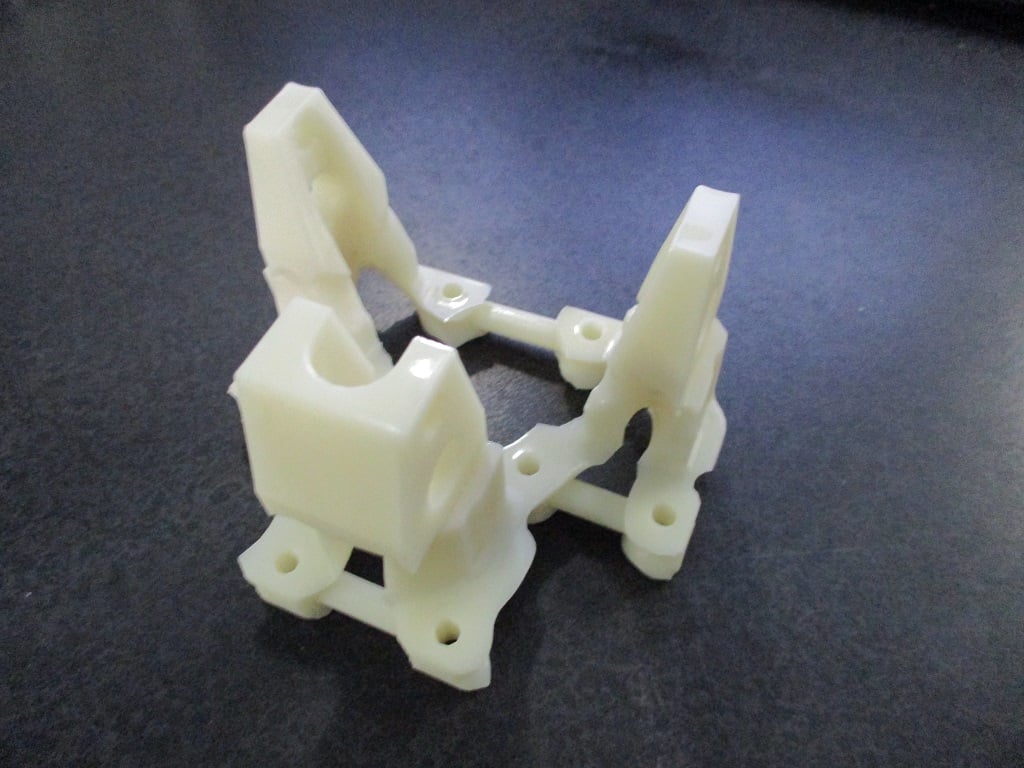
Mass: 60 g
Properties:
UTS = 38 MPa
YM = 1590-1660 MPa
Results: Lightweight / Flexible / Low Yield Strength
[Source: XYZprinting]
The Right 3D Printer For The Job
The new bracket was lightweight — but not as rigid as daily operation called for. While SLA had been workable at first, it turned out for the HARBEC team that a different 3D printing technology would suit both design and operational need better.
With more than two decades’ experience in 3D printing, HARBEC turned to its own substantial options. The company’s additive manufacturing capabilities extend to:
- FFF: Markedforged Mark Two
- DMLS: EOS270, EOS290
- SLA: 3D Systems Projet6000, Formlabs Form2
- Polyjet: Stratasys Connex500
- SLS: XYZprinting MfgPro230 xS
Among these, the MfgPro230 xS was the best choice to create a lightweight, stiff, dimensionally accurate end-of-arm bracket that could stand up to everyday use. The team selected a nylon material — sPro12W (Nylon 12 White) — to ensure the appropriate mechanical properties would be in place.
The sPro12W part proved the ideal end-of-arm bracket for HARBEC’s use, offering lighter weight and consistent performance with the original, non-optimized design.
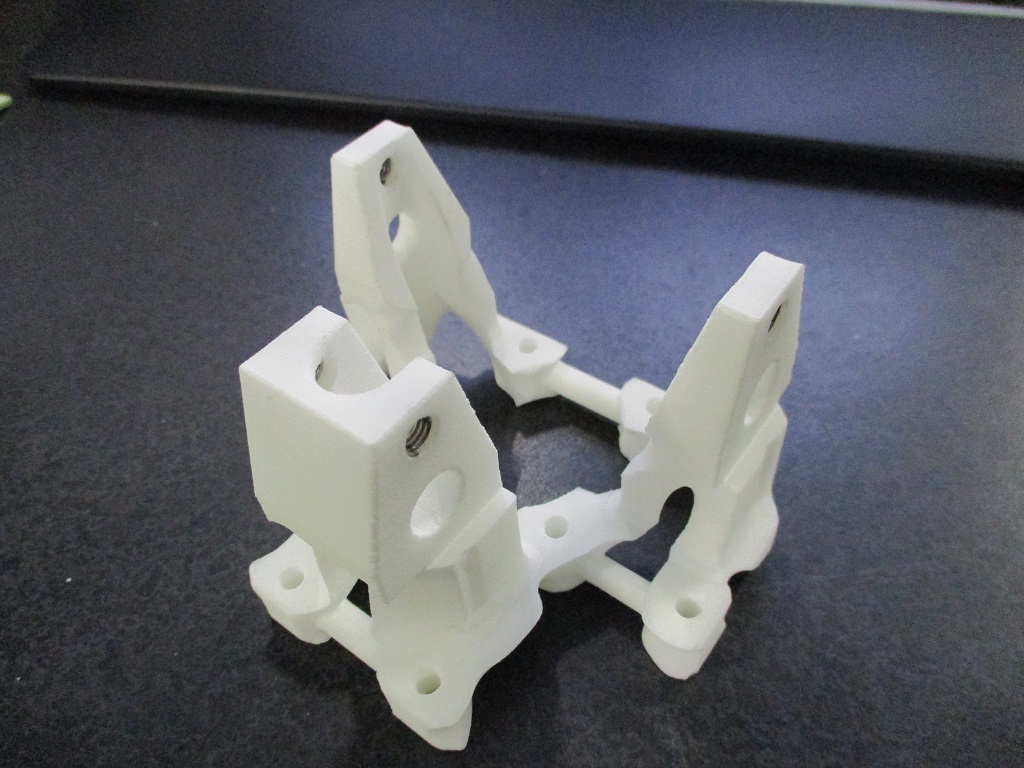
Mass: 50 g
Properties:
UTS = 48 MPa
YM = 1700-1800 MPa
Results: Lightweight / Rigid / Moderate Yield Strength
[Source: XYZprinting]
“The XYZprinting’s MfgPro230 xS has the capabilities to create any of the plastic end of arm tools to operate the robots at HARBEC,” said Bob Bechtold, President of HARBEC.
Today, the HARBEC team is examining additional applications for manufacturing improvements they can achieve in-house with their XYZprinting MfgPro230 xS.
Other companies, like TrySight and Azoth, have also seen great success in meeting their manufacturing needs with the MfgPro230 xS as the SLS system can offer a fast return on investment and new capabilities for digital inventory.
Via XYZprinting