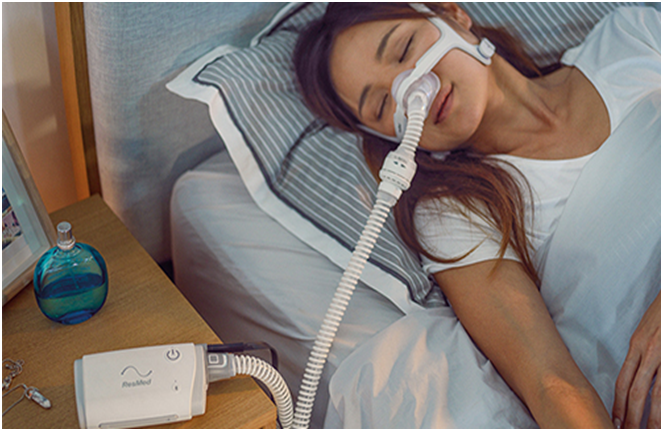
Charles Goulding and Peter Favata contemplate 3D printing opportunities that could arise in a more personalized sleep care industry.
ResMed, based in California and founded in 1989, is a $3 billion fast-growing company that designs medical equipment, specializing in the treatment of sleep apnea and other respiratory diseases. This includes devices to treat sleep-disordered breathing and respiratory conditions, masks used for delivering oxygen and other respiratory needs offering at home and hospital use, and portable oxygen concentrators. These products allow many people with respiratory diseases to live better and healthier lives. ResMed has been on an acquisition spree with an emphasis on software and data which provides critical information for a medical company.
ResMed has been dedicating more time and money to the R&D of its products while also hiring more employees. Below is a chart showing ResMed’s recent acquisitions.
3D Printing Opportunities
ResMed’s products adapt very well to 3D printing. Many people have been using 3D printers to create replacement parts or customize the products to best fit their needs. An example of this is a 3D printed filter adapter for the Airfit F20 CPAP mask that is used for sleep apnea. This is less expensive than buying the normal filter adaptor while also allowing you to cut it down to an N95 size.
3D printing has been used for repair parts, extending the life of the equipment. In one instance, the piece that flows air into the nose had broken off, making the mask unusable. Luckily with 3D printing a new piece could be 3D printed that worked properly.
ResMed could also take a page out of Metamason’s book and start 3D printing the nasal interface of their masks. What Metamason does is take a 3D scan of the person’s face and input data into a CAD program to create the design. The manufacturers then will take the CAD data and use a 3D printer to produce the product.
The Research & Development Tax Credit
Whether it’s used for creating and testing prototypes or for final production, 3D printing is a great indicator that R&D credit-eligible activities are taking place. Companies implementing this technology at any point should consider taking advantage of R&D Tax Credits.
Enacted in 1981, the now permanent Federal Research and Development (R&D) Tax Credit allows a credit that typically ranges from 4%-7% of eligible spending for new and improved products and processes. Qualified research must meet the following four criteria:
- Must be technological in nature
- Must be a component of the taxpayer’s business
- Must represent R&D in the experimental sense and generally includes all such costs related to the development or improvement of a product or process
- Must eliminate uncertainty through a process of experimentation that considers one or more alternatives
Eligible costs include US employee wages, cost of supplies consumed in the R&D process, cost of pre-production testing, US contract research expenses, and certain costs associated with developing a patent.
On December 18, 2015, President Obama signed the PATH Act, making the R&D Tax Credit permanent. Since 2016, the R&D credit can be used to offset Alternative Minimum Tax (AMT) or companies with revenue below $50MM and, startup businesses can obtain up to $250,000 per year in cash rebates that can be applied directly to payroll taxes.
Conclusion
3D printing is a very useful tool when it comes to manufacturing medical equipment. 3D scanning peoples features to make sure the equipment works as well as possible for them is a great new ability. As well as being able to make replacement parts quickly and efficiently is critical when it comes to something that may help save someone’s life.