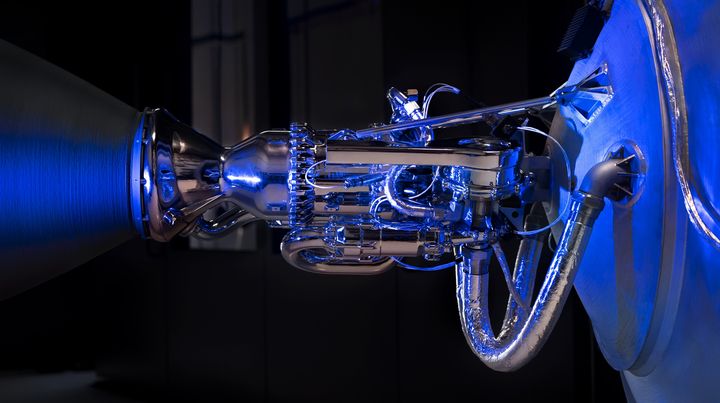
Relativity Space has landed a major client, Lockheed.
The California startup has been developing a means to — literally — 3D print an entire rocket. This is vastly different from the conventional approach, which involves traditional tools and a whole lot of individual parts that are often sourced from different suppliers.
Instead, Relativity Space intends on 3D printing all of the parts required. To do so, they have created a massive robot arm-powered 3D printer they call “StarGate”. It doesn’t send you to space itself, but it builds parts to do so.

Recently the company announced plans to massively expand their 3D printing farm to the tune of US$59M. It now seems that expansion will be well-used in the near future, with existing clients like Iridium and a new client.
Lockheed has selected Relativity Space to assist them with a new project they’re undertaking for NASA. The project is part of NASA’s “Tipping Point” solicitation. It’s a series of technology demonstrations that NASA believes are necessary to successfully enable later projects to the moon and beyond.
One of the projects in the “Cryogenic Fluid Management Technology Demonstration” category was awarded to Lockheed, with a fee of US$90M along with the obligation to complete the mission. The mission is described by NASA as follows:
“In-space demonstration mission using liquid hydrogen – the most challenging of the cryogenic propellants – to test more than a dozen cryogenic fluid management technologies, positioning them for infusion into future space systems. Lockheed Martin will collaborate with Marshall and Glenn.”
The problem they’re solving here is to ensure they know how to properly manage liquid hydrogen fuels over the long term. While liquid hydrogen rocket engines were successfully used on the now-retired Space Shuttle, they were only running briefly to take the ship to Earth orbit. That’s quite a bit different from having the liquid hydrogen sit for months while en route to, say, Mars, and expect it to be fired up when you get there.
The mission will experiment with a number of techniques to ensure liquid hydrogen can be retained in operational state for longer periods.
Tim Ellis, Relativity Space’s CEO, told TechCrunch:
“We’re building a custom payload fairing that has specific payload loading interfaces they need, custom fittings and adapters. It still needs to be smooth, of course — to a lay person it will look like a normal rocket.”
Flexible Rocket Design
One of the most important advantages provided by Relativity Space’s approach is flexibility. In a typical rocket manufacturing environment, contracts are specified with a large number of suppliers who then funnel parts to the assembler. It’s a long, drawn-out process that is rather inflexible as changes would require coordinating multiple parties with in-flight work.
Ellis explained the 3D printing advantage:
“With our 3D-printed approach we can print the entire fairing in under 30 days. It’s also software defined, so we can just change the file to change the dimensions and shape. For this particular object we have some custom features that we’re able to do more quickly and adapt. Even though the mission is three years out, there will always be last-minute changes as you get closer to launch, and we can accommodate that. Otherwise you’d have to lock in the design now.”
In these days of rapid change this capability becomes particularly important. Should Lockheed wish to change the design along the way, they can. That could be quite important as they seem to be testing a number of currently not-developed technologies that might require adjustment.
To me, this is a highly advanced way of leveraging 3D printing technology, and it’s one that few other industries have yet realized. While the aerospace industry is a bit peculiar in that they have relatively few parts at high cost, there certainly should be ways to use the 3D printing flexibility advantage in other industries.
Via Relativity Space, TechCrunch and NASA