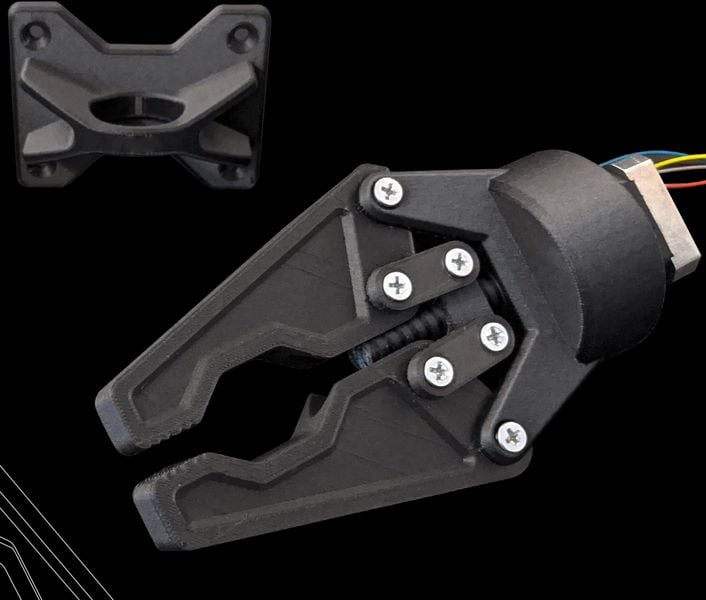
MakerBot announced the availability of a new nylon carbon fiber material for their METHOD series of 3D printers.
The company has been on a bit of a materials binge lately, with repeated announcements of new materials available for their METHOD platform. The METHOD, introduced in late 2018, and then updated the device in 2019 to the METHOD X, a platform offering high internal heating and thus the ability to use a wider variety of materials.
It seems that was their goal all along: enable the use of more powerful engineering materials. That’s something highly desirable in their new target market, professionals and engineers. It’s quite a distance from their original hobbyist and educational markets where basic materials like PLA were suitable. To attract professionals, MakerBot had to offer much stronger materials.
The METHOD X is where they can now do this, and they’ve been introducing a series of new materials. One we saw earlier this year was their original carbon fiber material, MakerBot Nylon Carbon Fiber. This strong material required the corresponding introduction of the MakerBot METHOD Carbon Fiber edition, which included a special extruder with nozzles capable of handling the highly abrasive carbon fiber material.
MakerBot Nylon 12 Carbon Fiber
This week MakerBot introduced a new variation to this material, which they call “MakerBot Nylon 12 Carbon Fiber”. There are some differences between these two materials:
Nylon Carbon Fiber
- Heat deflection: 184C
- Tensile strength: 110 MPa
- Tensile modulus: 7600 MPa
Nylon 12 Carbon Fiber
- Heat deflection: 154C
- Tensile strength: 66 MPa
- Tensile modulus: 6000 MPa
As you can see, the Nylon 12 Carbon Fiber, while quite strong, is definitely not as strong as the original CF material. Similarly, it does not offer quite as high heat resistance.
Why offer this apparently weaker material?
There’s another factor: moisture resistance. The nylon 12 material absorbs substantially less moisture from the air, which is always a problem when 3D printing nylon materials.
Typically nylons will quickly absorb so much moisture even in a day’s exposure to corrupt the quality of printed parts. The effect is caused by the moisture boiling during the brief moment the filament passes the hot end of the 3D printer. The bubbles that form become part of the printed part, resulting in lousy surface quality and more notably poor part strength: bubbles aren’t a very strong structural material.
For this reason most 3D printer operators using nylons will keep them in a heated storage cabinet, even during 3D printing operations.
Similarly, once parts are built they are still made of nylon and will absorb water if exposed to the air.
The new Nylon 12 Carbon Fiber material is said to have much lower absorption of moisture. MakerBot says:
“The MakerBot Nylon 12 Carbon Fiber utilizes a nylon 12 base polymer, and is able to absorb less moisture than nylon 6/66. As a result, it retains more of its performance in the presence of moisture. Nylon 12 carbon fiber is designed to deliver a smooth carbon fiber 3D printing experience and achieve consistent performance in any environment. For applications that require parts to hold their form with minimal flex, such as automotive brackets or inspection gauges, nylon carbon fiber offers a tensile modulus of 6000 MPa, underscoring its high stiffness. The material is ideal for functional prototyping and lightweight tooling applications in aerospace, manufacturing, and automotive industries.”
This material likely opens up more opportunities for applications in several industries where moisture could be an issue. As a result, it may be that MakerBot will be able to sell more 3D printers to more companies, so this is a good move for them.
Via MakerBot