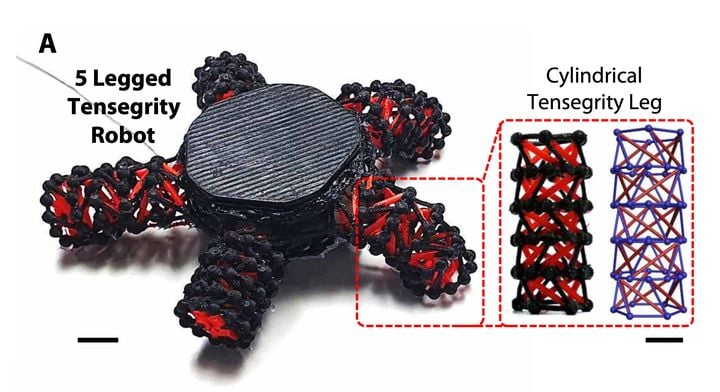
Researchers have found a way to use 3D printers to produce tensegrity structures.
Hold on, you ask, what the heck is a tensegrity structure?
A tensegrity is a type of structure that is made from a complex set of loose rigid parts and tensioned wires. If you saw the parts to a tensegrity you couldnāt imagine how they could be formed into a solid structure, yet this is entirely possible due to the tensional forces acting against the few rigid parts.
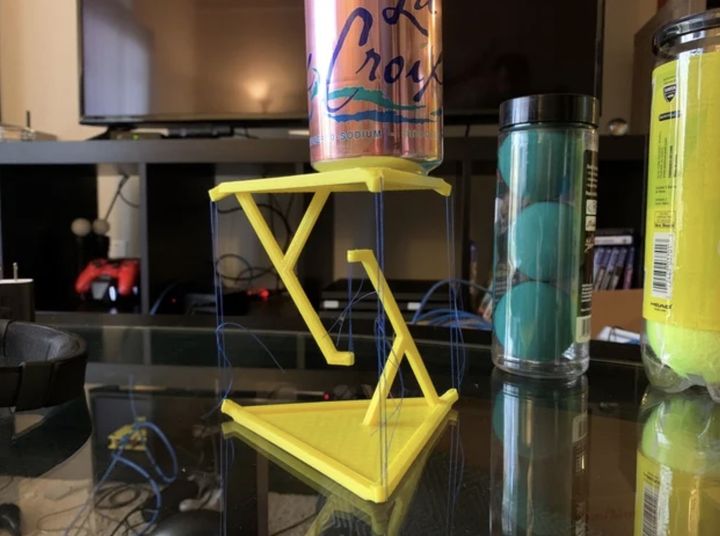
The tensegrity concept has been in our pages previous: earlier this year we selected a simple tensegrity structure as our Design of the Week. Itās something anyone could produce, and it results in a kind of āimpossible objectā.
Tensegrity structures can be functional as well, because some geometries allow for flexibility. Of course, this depends greatly on the tensegrity design, which can be extremely complex. In a sense, a tensegrity structure could be considered a type of meta-material that exhibits new properties.
Tensegrity designs can be made by implementing āprismā shapes made from the tensional components in specific arrangements.
These structures are also difficult to assemble, and most of the tensegrities youāll see are rather simple, like the Design of the Week example. However, if they could be made in more complex forms there is the possibility they could be used in more applications.
Now, researchers from South Korea’s Ulsan National Institute of Science and Technology have found a fascinating approach using 3D printing to achieve quick production of potentially highly complex tensegrity structures.
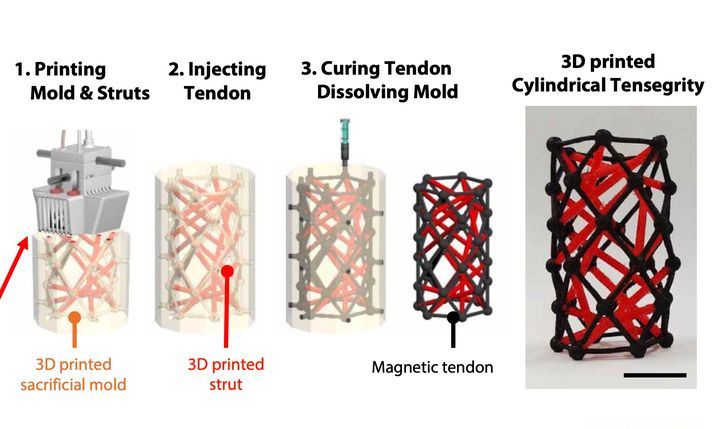
Rather than 3D printing the individual tensegrity components and then assembling them, they have found a way to āalmostā 3D print the entire structure in one job. I say āalmostā because there are two separate steps involved in their process. Letās take a look at how it works:
- A 3D model of the entire tensegrity structure is created, including both rigid and tensional components
- The rigid and tensional components are separated into two different portions of the 3D model
- A third element is added: a single solid block that surrounds all of the other elements
- The tensional components are subtracted from the solid block, leaving voids where the tensional structures should be
- This composite 3D model is then 3D printed on a dual extrusion 3D printer
- The solid block is 3D printed in PVA material, while the rigid elements are 3D printed in standard PLA material
- This results in a solid block of PVA with channels where tensional structures will be, and some loose rigid parts
- A liquid material is poured into the channels, which hardens into an elastic material to become the tensional structures
- The entire block is placed in water, where the PVA dissolves
- This leaves the tensional structures holding the rigid parts in place as designed ā and we have the tensegrity
This is incredibly simple: Design, 3D Print, Cast and Dissolve. Thatās it!
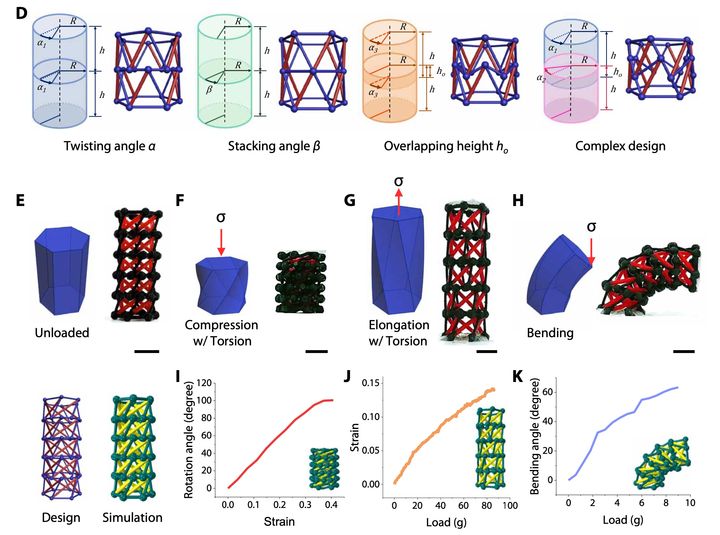
The researchers believe this technique could be used to more easily produce highly complex tensegrity structures that could taken on various functional roles. What those functions might be is a subject for further research, but the door has just been opened: this is such an easy process many should be able to use it.
Aside from the tensegrity production, this technique could be used in other ways in 3D printing as a method to incorporate third materials into a 3D print. One can imagine small blocks of āmoldsā being 3D printed on a model and then filled with casting material after the print completes.
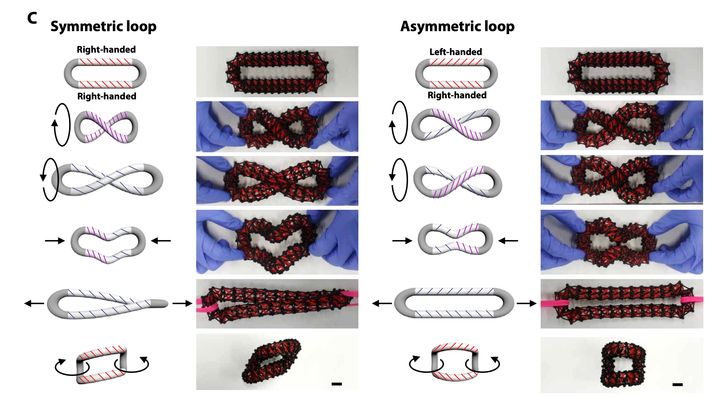
This approach could add flexible materials, for example, that might not be easily 3D printed. Or thermoset materials could be incorporated into a thermoplastic model. The possibilities here are endless.
3D printing and casting: an interesting pair of processes that may become more intertwined in the future.
Via ScienceMag