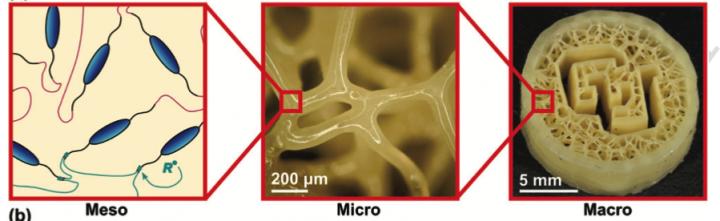
Scientists have developed a new 3D printing material that closely mimics biological tissues.
The Problem
Biological tissues are really specialized, meaning that they’re great at what they do. Unfortunately, it also means that they’re really hard to replace. Over time, they have evolved to be perfect at their specific functions. For example, cartilage is a compliant and elastic tissue that cushions joints but remains strong enough to resist compression and bear substantial loads.
Creating an artificial replacement that can fill the shoes of such tissues would naturally be a challenging feat.
The New Discovery
Over at the University of Colorado Denver, Chris Yakacki, PhD, along with the team of scientists that he led, became the first to 3D print a complex, porous lattice structure made up of liquid crystal elastomers (LCEs) to create a device that can mimic cartilage among other biological tissues.
The team, joined by professor Kai Yu, PhD, postdoctoral fellow Devesh Mistry, PhD, doctoral student Nicholas Traugutt, and scientists from the Southern University of Science and Technology (China) reported their findings in the Advanced Materials journal.
LCEs
Yakacki, who works at the CU Denver’s Smart Materials and Biomechanics (SMAB) Lab, started his journey with LCEs — soft and multifunctional materials that are known primarily for their elasticity and extraordinary ability to dissipate high energy — in 2012. By 2018, the scientist had been given an NSF CAREER award to rethink the manufacturing process of LCEs. He also got several rounds of funding to apply the technology to football helmets to improve their shock absorbing properties. Yakacki wasn’t ready to step down from LCEs just yet, however.
He says:
“Everyone’s heard of liquid crystals because you stare at them in your phone display.”
He explains further:
“And you’ve likely heard of liquid crystal polymers because that’s exactly what Kevlar is. Our challenge was to get them into soft polymers, like elastomers, to use them as shock absorbers. That’s when you go down the layers of complexity.”
The Process
LCEs were originally used to create large objects with little detail or microscopic structures with immense detail, solely because of how tricky LCEs are to work with. Over recent years, they have been used to create larger devices with higher resolutions — for example the phones in our pockets.
Yackaki and his team came up with a 3D printing process that simplified the entire manufacturing process of such devices. The team focused on the DLP process and designed an LC resin that resembled honey. When coming into contact with UV light, the resin cures and forms new bonds in thin photopolymer layers, forming a soft, strong and compliant elastomer. These qualities make this material ideal for printing cartilage and other such tissues. Their new method multiplied the rate-dependence by 12 and the strain-energy by 27 in comparison to objects printed using a commercially available photocurable elastomer resin.
After this discovery, the team used their resin to build many objects such as a tiny (but detailed) lotus flower and a prototype for a spinal fusion cage — as a result creating the largest and most detailed LCE device.
Further Applications
Yakacki was reminded of his old project and recognizes the application of this material in shock-absorbing football helmet foam or even mini biomedical implements for toes. He looks forward to learning more about the applications of the process for the spine.
“The spine is full of challenges and it’s a hard problem to solve,” he says.
“People have tried making synthetic spinal tissue discs and they haven’t done a good job of it. With 3D printing, and the high resolution we’ve gotten from it, you can match a person’s anatomy exactly. One day, we may be able to grow cells to fix the spine, but for now, we can take a step forward with the next generation of materials. That’s where we’d like to go.”
The Impacts Of The Discovery
As I’ve said time and time again, 3D bioprinting is definitely an area that sparks my interest. What is special to this particular project? Of all of the materials they could use to bioprint tissues, it would have never occurred to me to use a material that is used to manufacture a phone. The most ingenious part of this project for me is the connection that was made between the material and this particular application.
Obviously, with a discovery this huge, there will be work done to further analyze the applications of their new resin and process. As an athlete myself, I recognize the importance of protective equipment that does its job well. Sports like football and hockey are considered more “high-risk” than most others because of the amount of contact and room for injury. I hope to hear more about this team when their versatile technology is applied not only in the medical industry, but as unusual as it initially sounds, in the sports one as well.
Via EurekAlert!