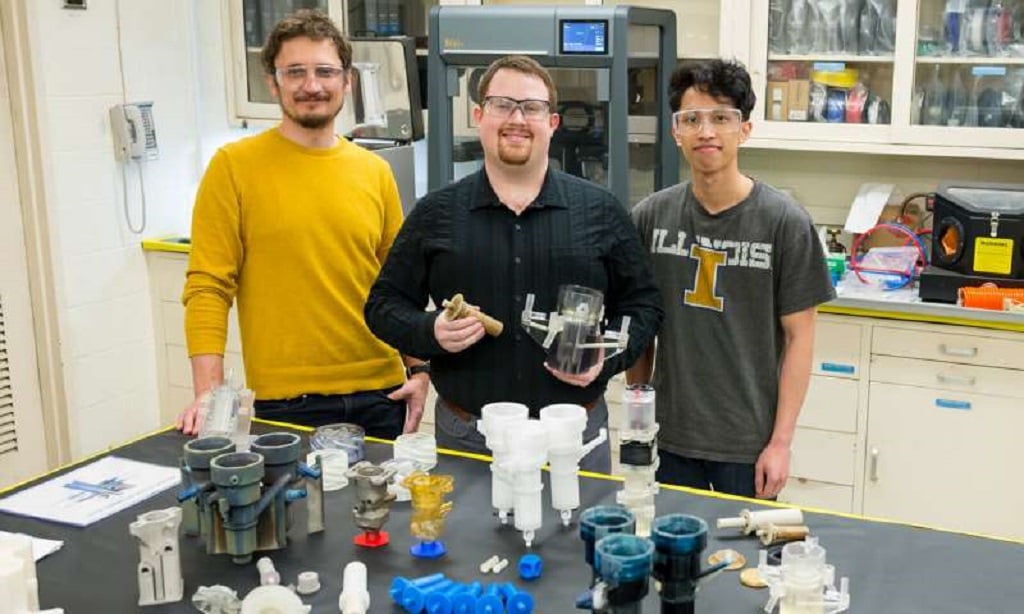
Argonne scientists have developed an innovative method to more accurately, cost-efficiently, and reliably recycle an important medical isotope using 3D printing.
Molybdenum-99
The isotope in question — Molybdenum-99 or Mo-99 — is a medical isotope that significantly aids radiologists diagnose heart disease, bone decay, and cancers that are otherwise difficult to detect. Mo-99 decays to form technetium-99m, which radiologists can now use to create the pharmaceuticals that are used in medical procedures.
The benefits of the isotope however, come at a hefty cost. Enriched molybdenum (which is used to make Mo-99) costs approximately $1,000 per gram, because commercial producers simply haven’t been able to recycle the enriched material for a more affordable cost.
The Discovery
For the first time ever in the U.S., earlier this year scientists at the U.S. Department of Energy’s Argonne National Laboratory came up with a technique to recycle isotopically enriched molybdenum (Mo-98 or 100) by taking advantage of 3D printed parts. Their new findings improve upon the laboratory’s past recycling method, which was pioneered by Peter Tkac in 2015.
The Initial Process
Back in 2015, when Tkac and his team discovered a method to recycle enriched molybdenum, the process was tiring work, to put it simply. They first had to convert the enriched molybdenum into an acidic solution along with some other chemicals. Following this, they had to purify the enriched molybdenum through multiple stages with funnels and test tubes.
“Our original method would have been very difficult to automate,” Tkac says.
The New Technique
A year after the development of the initial procedure, Tkac, Peter Kozak, and others joined forces to do exactly what they had previously claimed difficult — automate the process. The funnels, test tubes, and painstaking manual labor were thrown out in favor of spinning 3D printed acrylic contractors (which would spin and separate chemicals using centrifugal force), which reduce the cost significantly, making the process much more efficient (both in terms of cost and time).
“We printed each contactor as one piece with streamlined features and fewer external connections. This allows us to push the liquid through the system as quickly and reliably as possible,” Kozak explains.
The new process worked. Well, for the most part at least. After about 15 hours in use, the hydrochloric acid began corroding the plastic.
Although theoretically the experiment was a success, Kozak mentioned that in order to go into full production, the material will have to survive much longer than that.
PEEK
This is where the duo stumbled across PEEK, which resists the mineral acids and organic solvents of the recycling process. Because PEEK shrinks as it’s 3D printed — and hence warps — Kozak modified the speed and temperature of the printer’s fan, allowing him to 3D print PEEK materials that are stronger and more flexible than the initially used acrylic plastics.
This material was the cherry on top for the team as it proved to be cheaper, faster, and more efficient of a material that is still able to resist the chemicals involved in the process of recycling enriched molybdenum.
The Impact
At the end of the day, the goal was to simplify an otherwise lengthy, labor-intensive, and costly process while sacrificing as little as possible in terms of the benefits of the original process. As we’ve already established, the new process accommodates for all of these factors, while offering immense long-term benefits.
No matter how much we’ve tried to equalize the playing field for the rich and the poor, people with more money generally have access to better healthcare and, consequentially, the opportunity to live a longer life. This innovation goes much further than the lab — it means that even those who otherwise couldn’t afford healthcare will now be able to receive faster and more reliable diagnoses for a cheaper cost. Yet again, another example of 3D printing making life better for everyone.
Via Phys.org