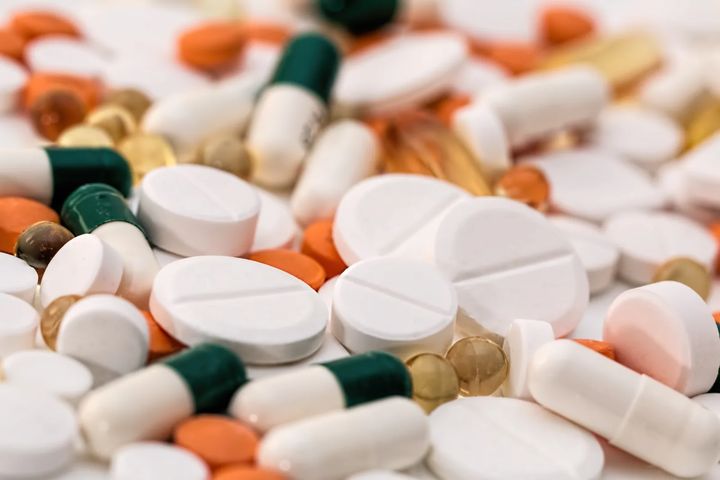
Since its inception during the later decades of the last century, 3D printing (also known as additive manufacturing) has moved far beyond merely fabricating simple plastic parts.
Today the technique can be used to produce much-needed medical supplies such as personal protective equipment for health care workers fighting COVID-19. Among other advances, 3D printing is now also considered a serious tool to advance medicine and pharmacology through bioprinting.
Bioprinting can create anatomical models of patients prior to surgery and some biological tissues, with the goal of progressing to printing whole complex organs such as the heart. However, another emerging and potentially revolutionary use for 3D bioprinting is the production of pharmaceutical drugs that are tailored to meet the needs of specific patients.
In 2015 the U.S. Food and Drug Administration approved the first 3D-printed pharmaceutical, SPRITAM (levetiracetam), created by Aprecia Pharmaceuticals for the treatment of seizures. Although the drug remains the only 3D-printed drug currently approved by the FDA, the many advantages of 3D-printed drugs place them at the forefront of what’s ahead for medicine as the FDA works on formulating a regulatory framework for them.
Bioprinting pharmaceuticals achieves what traditional drug manufacturing cannot, and that is the low-cost production of customized pill medications for patients who need special dosing, quantities or composition of drugs. Pills can be 3D printed in unique sizes, shapes and with slow-release capabilities. 3D printing also allows for the inexpensive creation of the “polypill,” in which a single pill can contain multiple drugs that a patient is prescribed, reducing the number of pills that need to be consumed.
Bioprinting could also theoretically allow pharmaceuticals to be produced wherever there’s a suitable 3D printer, such as a hospital or pharmacy. This could reduce wait times that patients sometimes experience for certain mediations as well as reduce the need for transporting them.
Beyond making medications more convenient to procure and take, bioprinting stands to impact the pharmaceutical industry in much deeper ways. So-called orphan or rare diseases pose a challenge for pharmaceutical companies because they require the development, testing and manufacturing of drugs that will be taken by a very small subset of the population. Some of these medications can even require specialized equipment to produce them. Conversely, 3D printing is well suited to the production of pharmaceuticals to treat orphan diseases because it’s geared for customized pills made in small batches.
In 2017, Aprecia and Cycle Pharmaceuticals partnered to develop a ZipDose 3D printing technology that utilizes a fluid to bind together a multilayered powder, resulting in pills that dissolve quickly with the addition of water, support high dose loading of up to 1,000 mg, and can be easily made to taste pleasant. This patented method can help simplify and ease the medication schedule for patients with chronic conditions. ZipDose works by using something similar to a conveyor belt to deposit a powder layer containing an active drug. The layer then goes under an inkjet that adds the fluid as a binding agent at various junctures. This process is repeated layer by layer, producing a multilayered 3D printed tablet. Once moisture hits the sporadic bound junctures of a given tablet, it immediately dissolves.
Read more at ENGINEERING.com