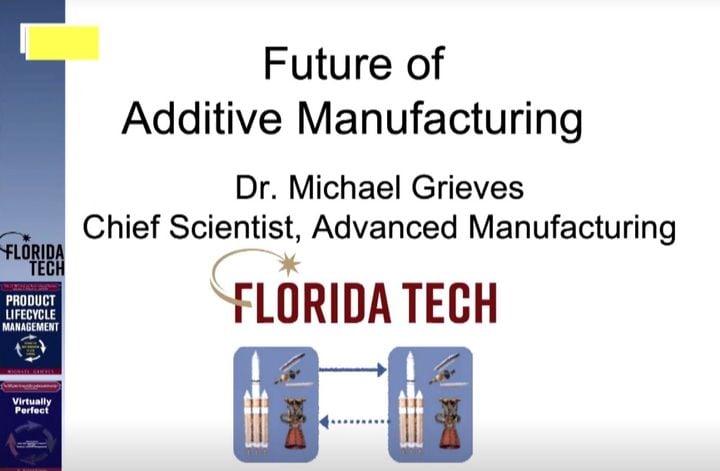
An interesting talk at the third episode of the ongoing 3DEXPERIENCE: A Virtual Journey revealed some hints about what may happen in additive manufacturing’s future.
The 26-minute talk was given by Dr. Michael Grieves, who is the Chief Scientist in Advanced Manufacturing at Florida Tech. Grieves explained his thoughts on where he thinks things are headed in the technology.
With the expected massive growth in additive manufacturing usage over the next two decades, there are some challenges that must be overcome along the way.
AM and Digital Twins
Grieves is fascinated with the idea of “digital twins”. What’s a digital twin? Wikipedia explains:
“A digital twin is a digital replica of a living or non-living physical entity. Digital twin refers to a digital replica of potential and actual physical assets (physical twin), processes, people, places, systems and devices that can be used for various purposes. The digital representation provides both the elements and the dynamics of how an Internet of things (IoT) device operates and lives throughout its life cycle.”
Grieves believes digital twins could hold an important influence over additive manufacturing in the future, as they can be used to provide advanced ways to provide quality control, among other things. The idea is to be able to design, build and test an object entirely virtually, and this will enable one to far more quickly evaluate the part’s performance, quality and cost.
Grieves calls this “moving work from the physical to the virtual”. He believes additive manufacturing could work very well in this digital twin environment.
If this isn’t clear, it works like this: simulate the design, build and test phases virtually as many times as required to “get it right”, and only then push the button to physically produce the part. This will dramatically increase the likelihood of physical success, because most of the bugs will have already been worked out in the sim.
DfAM in The Future
Grieves is concerned with DfAM, or Design for Additive Manufacturing. This is a particular skill that optimizes designs for 3D printing, and is something that few current designers have been trained to do. Grieves believes overcoming this will require not only technological changes, but also cultural changes to adjust how designers think and overcome years of experience and training in other approaches.
Grieves says:
“Understand it’s not just a technology issue, it’s going to require a change in culture of, in essence, how we design and manufacture products, how we test products, how we educate the engineers and manufacturers of tomorrow in universities of today in terms of how this is going to work.
It really is a change in not only the technology but also in how we think about products and how we think about their manufacture.”
These will require new design rules, new design implications and directly tie design rules to machine types, rather than today’s environment where this doesn’t really matter for milling equipment. Grieves expects to see new ways to capture information and ways to evaluate for quality, and this will all require different cultures.
Grieves expects to see new materials developed for specific additive manufacturing applications, and even expects multi=material approaches to continue to appear.
Additive Manufacturing Barriers
Grieves sees several barriers to additive manufacturing success:
- Internal functional silos where different departments cannot easily work together in the new ways that will be required
- Traditional university education is still focusing on older techniques instead of DfAM, if they teach about manufacturing at all
- Certification and testing is not optimized for use with additive manufacturing
Digital Twin Part Certification
Grieves wants to see parts certified through the use of digital twins as discussed above. This would involve creating an instance of a digital twin to represent a specific, physically printed part. This will require considerable capture of data during the printing process to create the digital twin. Once captured, it should be possible to perform a destructive test on the digital twin, and this will inform us of the probable performance of the physical part.
This could allow for proper quality testing of each and every 3D printed part in an efficient manner.
Indeed, we may be moving in that direction, as I have consistently seen 3D printer manufacturers add more sensors and recording of job activity. This is precisely the type of data that Grieves is looking for, although there’s likely a lot more required for full simulations.
These thoughts are certainly provocative and I agree strongly with Grieves. Some of these things are actually underway, one way or another, already.
The future is coming.