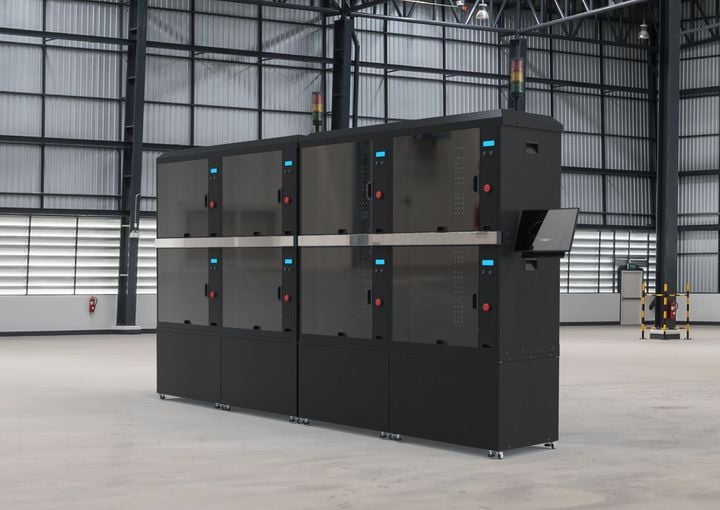
Smart3D International has announced a new 3D printer, the Macro, and it’s intended for use in manufacturing.
You may not recall Smart3D, as much of their recent publicity has been under the KODAK banner. The Argentina-based company obtained a license from KODAK to design, produce and market the powerful KODAK Portrait 3D printer, which we reviewed in 2019.
While the new Macro device is not under the KODAK brand, it is produced by the same folks who made the excellent KODAK Portrait 3D printer.
The two devices are quite a bit different. While the Portrait focuses solely on the professional market, the Macro is more of an industrial device — or system: It seems to include elements to address both prototyping and production.
This is accomplished through two different form factors for the device: a prototyping unit (“PU”) and a production module (“PM”). While these two different units seem to use more or less the same build chamber and extrusion technology, the rest of the device is quite different.
Macro Specifications
Both PU and PM units use a rather large build volume of 350 x 350 x 400 mm, large enough to produce many small objects or a smaller number of larger objects. The 400mm height ensures the ability to produce tall objects as well.
What’s really interesting is the extrusion capabilities on this machine. Unlike the Portrait, the Macro can handle a much wider array of materials. This is due to its high-temperature build chamber, which can be heated up to 120C, and its high-temperature hot end, which can reach an amazing 500C.
This allows the Macro to 3D print materials including: Smart3D ABS, ASA, BVOH, HT Breakaway, PA 6/66, PA 6/66/12, PA12, PAHT, PAHT CF, PC-ABS v0, PEEK, PETG, PMMA, POM, PP CF, PVA, Tough PLA, TPU. Smart3D International also has a materials partner program through which even more materials can be used.
The Macro is a dual extrusion device, and it seems to use a similar technology to what was used in the Portrait: a single motion carriage with two hot ends, but with an ability to raise the unused hot end during operations. On the Portrait this is done by slamming the carriage into the side to “click” it over to the other hot end. I suspect the same approach is used in the Macro.
The Macro includes a live camera and an expanded list of connectivity options. While the usual USB, WiFi and Ethernet options are available, they also list “NFC” as a possibility. This is quite interesting, as I have not seen any 3D printer use NFC yet. I’m not exactly certain what they intend to do with this capability.
The Macro uses the Smart3D cloud network for control, monitoring and job preparation. This is the same cloud used for the Portrait, and it is based on the successful 3DPrinterOS system. I’ve used this on the Portrait and it works quite well, as they can distribute optimized materials profiles instantly to ensure great print quality.
One interesting item is the build plate, which is not fully described. However, you can see one in action in their video above. The video clearly shows a flexible build plate, and that would absolutely speed up production post-processing significantly. This is quite a change from the Portrait’s rigid glass bed.
An integrated filament drying solution is also included, and this is critical for successful use of many high-temperature materials, including PEEK.
There’s also a HEPA filter installed in the Macro devices that should permit operation of the PU in design offices. However, I suspect the PM units will not be in an office as they appear to be intended for a factory floor.
Smart 3D Macro PU and PM
There are two different form factors to permit the full lifecycle of product development. The idea here is that a designer would use PU to iterate on a design until it is finalized. Then, once ready, it would be transferred through the Smart3D cloud to the PM units for low-volume production.
The key here is that the PU and PM build technology are near-identical. This means that the designer can be assured that the production prints will be the same as those that were made during prototyping. This is quite an important step, as some other systems would require two different types of printers to be involved, and thus there’s extra steps to ensure the prints match. Not so with the Macro system.
The PM units are scalable. One PM unit comes equipped with no fewer than FOUR build chambers, so you know right away this is for production purposes. However, it appears that you can add more units to the level required.
At top the image is actually two PM units placed side by side, with each contributing four build chambers for a total of eight. As you can imagine, you can add more of these as required to meet production needs.
To control these devices one simply uses the well-established Smart3D cloud network. You can add all the devices to the company account and manage them centrally. What is not fully described is how jobs are dispatched to this group of 3D printers. I suspect they have some approach for sending work to available machines to avoid queuing and maximize operations. It’s not clear how many of these can be added, but it’s probably a substantial number.
Smart3D does say in their video the following:
“Macro 3D printers interconnect via a serverless neural network that guarantees a level of redundancy and security unseen in additive manufacturing. Their scalable approach can help companies integrate additive into their processes for low initial investment and scale transparently as the production demand grows.”
Smart3D says the new Macro system is shipping now, but we do not yet have pricing for the system.
This is a huge step for Smart3D, as it effectively allows them to enter an entirely new market, and one that could be quite profitable.